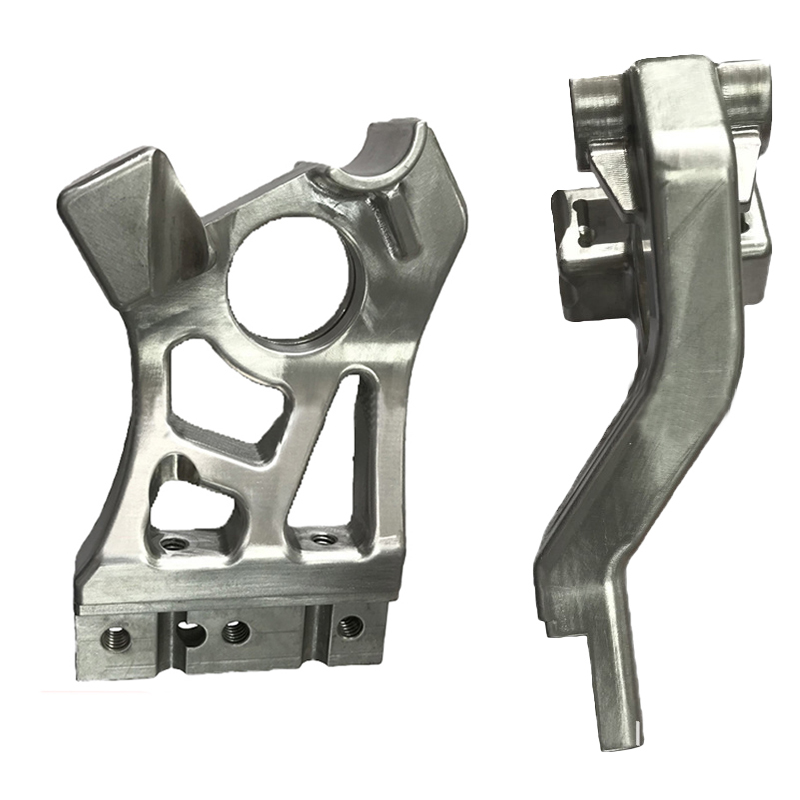
What are the Applications of Aluminum Alloy Precision Forging Parts
Precision forging refers to the forging process of forging complex shapes and high-precision forgings on forging equipment. Like precision forging bevel gears. The tooth shaped part can be directly forged without cutting. The dimensional accuracy of forging can reach IT12~ITL5, and the surface roughness Ra is 3.2~1.6 μ m.
Precision forging has high requirements for the billet, requiring small quality tolerances, small cross-sectional collapse angles, flat end faces, and being perpendicular to the billet axis. The surface of the billet shall not have any pockmarks, cracks, pits, large scratches or bumps; In addition, the surface must be cleaned (polished, polished, pickled, etc.) before forging, and surface oil stains, slag inclusions, bumps, dents, etc. must be removed. Aluminum alloy precision forging mainly adopts sawing and turning cutting, among which sawing cutting is more commonly used.
During precision forging, crankshaft forging machines, precision forging machines, or other different equipment can be used for joint forging. Repeatedly forging multiple times, usually precision forging 2-3 times after ordinary forging, can reach ± 0.2~± 0.3mm, and the surface roughness is lower than Ra6.3. In order to achieve higher dimensions, the cold precision on the precision press can reach ± 0.1mm, with a surface roughness lower than Ra0.80.
Inspection and cleaning must be carried out between several processes in forging production. The next precision forging process can only be carried out by polishing or polishing the surface defects of the billet.
Precision forging is a relatively new type of non cutting processing technology developed on the basis of ordinary molds. It directly forges or leaves only a small amount of grinding scenes to meet the precision requirements of some parts that need to be cut and machined in the past. Therefore, adopting precision mold forging technology requires stricter technical requirements for the relevant links of mold forging, such as controlling the blank cutting quality and surface quality; Reasonably design prefabricated blanks; Less blank space, no oxidation heating; Heating and cooling standards control; Precision control in mold manufacturing and usage; Choose appropriate lubrication and cooling conditions.
Precision forging has significant advantages in saving metal and reducing cutting processing time, but due to the strengthening of relevant links in forging, some costs will increase. Therefore, based on the comprehensive economic indicators of finished parts and the special requirements of part structure and performance, it is necessary to consider whether to choose precision forging technology for specific products.