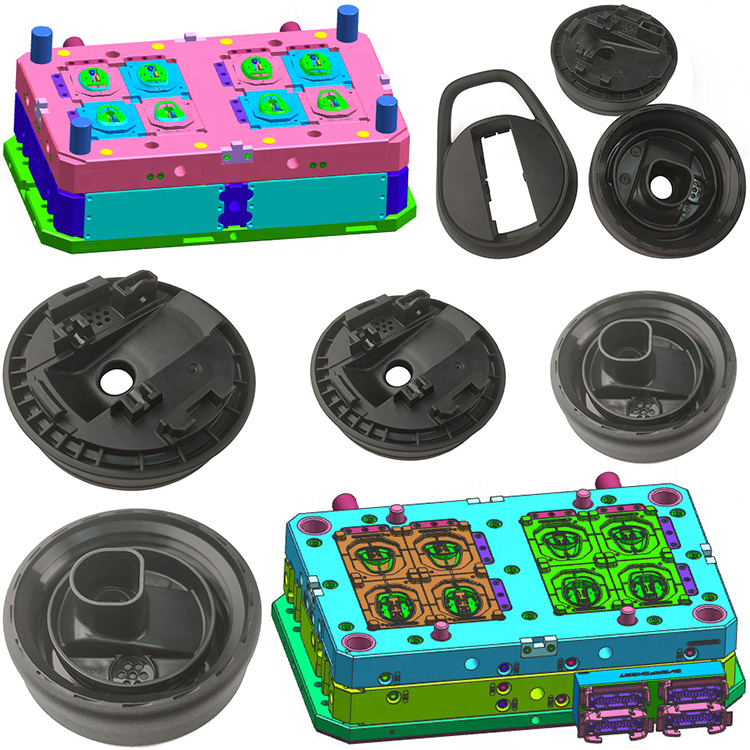
Basic Knowledge of Rubber Mold Design
Classification of rubber molds
Rubber molds are divided into four commonly used molds based on their structure and production process: compression molding molds, die-casting molding molds, injection molding molds, extrusion molding molds, as well as some special rubber molds for producing special rubber products, such as inflatable molds, dipping molds, etc.
1.Compression molding mold
Also known as ordinary compression molding. It is to directly place the semi-finished rubber material that has been mixed, processed into a certain shape, and weighed into a mold, and then send it to a flat vulcanizing machine for pressure and heating. The rubber material is vulcanized and formed under pressure and heating.
Characteristics: The mold structure is simple, versatile, widely used, and easy to operate, so it occupies a large proportion in rubber molded products.
2.Die casting molds
Also known as transfer mold or extrusion mold. It is a process of placing mixed, simple shaped, and limited semi-finished rubber materials or blocks into the die-casting mold cavity, extruding the rubber materials through the pressure of the die-casting plug, and allowing the rubber materials to enter the mold cavity through the pouring system for vulcanization and shaping.
Characteristics: More complex than ordinary compression molding, suitable for making thin-walled, long and easily bent products that cannot be pressed or barely pressed by ordinary compression molding, as well as rubber products with complex shapes and difficult to add materials. The products produced using this mold have good density and superior quality.
3.Injection molding molds
It is the process of injecting pre heated plastic material into the mold through the pouring system of the injection mold for shaping and vulcanization.
Characteristics: Complex structure, suitable for large, thick walled, thin-walled, and complex shaped products. High production efficiency, stable quality, and the ability to achieve automated production.
4.Extrusion molding mold
Various cross-sectional shapes of rubber profiles are made into semi-finished products through the molding die of the machine head, achieving the purpose of preliminary shaping. Then, after cooling and shaping, they are transported to the vulcanization tank for vulcanization or used as pre formed semi-finished rubber materials required for compression molding.
Features: High production efficiency, stable quality, and the ability to achieve automated production.