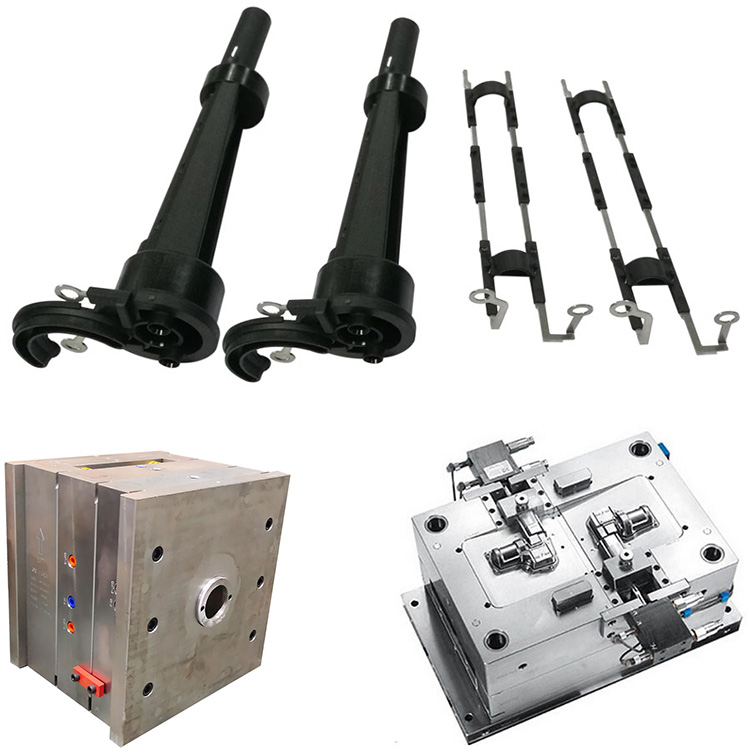
What Parts in Plastic Molds Need to be Avoided When The Mold is Fitting?
In the design of plastic molds, in order to ensure smooth assembly and efficient operation of the mold, the coordination between multiple parts needs to be avoided. Here are some common parts that require air avoidance treatment for coordination:
1.Positioning ring and panel: The positioning ring plays a positioning role in the mold. To ensure smooth fit with other parts, a single-sided clearance of 0.1mm to 0.25mm is usually required between the positioning ring and the panel (different designs or standards may vary, such as 0.15~0.25mm for some designs).
2.Sprue bushing and related parts: sprue bushing is a component used for injection molding in molds, and its coordination with the hanging platform, mold core, and mold base requires clearance. The gap between the nozzle suspension platform and the panel on one side is generally 0.5mm. Except for retaining 20mm of sealant in the mold core, the gap between the nozzle and the mold blank on the other side is 0.5mm. The gap between the nozzle and the mold blank on one side is also 0.5mm.
3.Support pillar and ejector block: The support column is used to support the plastic mold structure, while the ejector block is used to ejector the molded product. The fit of these parts in the mold also needs to be avoided, with one side of the support column with a diameter of less than 50 millimeters being 2 millimeters and the other side with a diameter of more than 50 millimeters being 3 millimeters The clearance of the ejector block and its related components such as ejector pin through holes, ejector pin cup heads, ejector pin mesons, etc. on the B-plate or ejector pin panel is generally 0.5mm.
4.Diagonal guide pillar and inclined guide pillar hole: The inclined guide column is used for the core pulling mechanism of the mold, and its fit with the inclined guide column hole requires a unilateral clearance of 0.5mm. If the inclined guide column is long and extends into the B plate, the B plate must also avoid the inclined guide column, and the single-sided air avoidance can reach 2 millimeters.
5.Sliding block seat and mold base: The fit between the sliding block seat and the mold base also needs to be avoided, and the single-sided avoidance is generally 0.5mm.
6.Spring hole: The clearance of the spring hole on the B plate is generally 0.5mm to 1mm, depending on the size of the spring and the design requirements of the mold.
7.Template screws and mold base: Template screws are used to fix templates, and their fit with the mold base requires a clearance of 0.5mm on one side.
8.Mold locking screw and mold core: Mold locking screw is used to fix the mold core, and its fit with the mold core also requires a unilateral clearance of 0.5mm.
9.Small pull rod sleeve and template: The small pull rod sleeve is used for the mold closing mechanism of plastic molds, and its fit with the template requires a single-sided clearance of 0.5mm.
10.Insert hanging platform and mold core: When designing inserts, a gap should also be designed between the insert hanging platform and the mold core. One side of the insert block is generally 2 mm away from air, and the air gap is rounded to facilitate NC machining and mold matching.
The principles of avoidance processing mainly include: when conditions and space permit, making the avoidance space as large as possible to reduce the need for secondary processing; Meanwhile, the avoidance design should facilitate processing and reduce processing time. Through reasonable air avoidance treatment, the smooth assembly and efficient operation of plastic molds can be ensured, improving the service life and production efficiency of the molds.