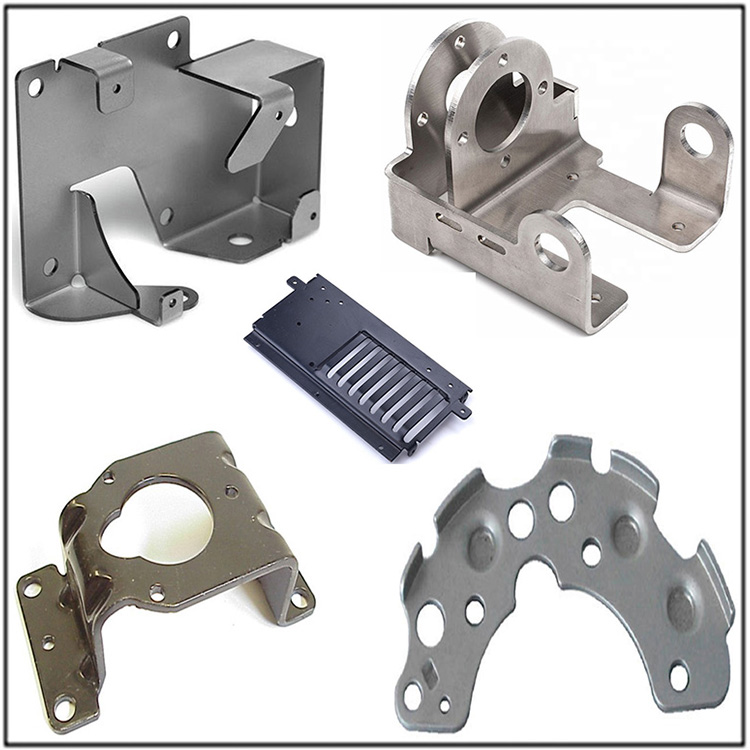
What are The Common Failure Modes of Stamped Parts in Application?
Common Failure Modes and Countermeasures of Stamping Parts in Applications
Stamping metal parts, as an important component of modern manufacturing, are widely used in various fields such as automobiles, home appliances, aerospace, etc. However, in practical applications, stamped parts may encounter multiple failure modes, which not only affect the performance and lifespan of the product, but may also pose a threat. This article will explore the common failure modes of stamped parts in applications and propose corresponding response strategies.
Fracture failure is one of the more severe failure modes of stamped parts. When stamping parts are subjected to external forces, if the stress exceeds the strength of the material, fracture will occur. Fracture failure may stem from defects in the material itself, unreasonable design, or improper manufacturing processes. In order to avoid fracture failure, it is necessary to strictly control the quality of raw materials, select materials with high strength and toughness, and optimize the design of stamped parts to ensure that they can evenly distribute stress under stress.
Secondly, deformation failure is also a common failure mode of stamped parts. Under long-term stress, stamped parts may undergo plastic deformation, resulting in changes in size and shape, thereby affecting their normal function. Deformation failure is usually related to mechanical properties such as yield strength and elastic modulus of the material. In order to reduce deformation failure, it is necessary to select materials with sufficient strength and rigidity, and consider appropriate margins in the design to cope with possible deformation.
In addition, wear failure is another common failure mode of stamped parts in applications. When stamped parts come into contact with other components or media, their surfaces will gradually deteriorate due to friction and wear, leading to a decrease in performance. Wear and tear failure may be caused by poor lubrication, excessive contact pressure, or poor material wear resistance. In order to slow down wear and failure, it is necessary to choose materials with good wear resistance, optimize lubrication conditions, reduce contact pressure, and regularly maintain and replace them.
Corrosion failure is another failure mode that stamping parts may encounter in specific environments. When stamped parts come into contact with corrosive media, a chemical reaction occurs on their surface, causing the material to gradually peel off and break. Corrosion failure may be caused by improper material selection, inadequate surface treatment, or harsh environmental conditions. In order to prevent corrosion failure, it is necessary to choose materials with strong corrosion resistance and carry out appropriate surface treatment, such as galvanizing, spraying, etc., to improve their corrosion resistance.
Fatigue failure is a possible failure mode of stamped parts under long-term alternating stress. When the stress exceeds the fatigue of the material, the stamped part will undergo fatigue fracture. Fatigue failure is usually related to the microstructure of materials, stress concentration, and working environment. In order to reduce fatigue failure, it is necessary to optimize the design of stamped parts, avoid stress concentration, select materials with high strength and high fatigue, and conduct regular fatigue testing and maintenance.
In summary, stamping parts may encounter various failure modes in application, including fracture, deformation, wear, corrosion, and fatigue. In order to ensure the performance and service life of stamped parts, corresponding response strategies need to be adopted for these failure modes, including optimizing material selection, design improvement, process optimization, and regular maintenance. Through these measures, the reliability of stamped parts can be improved to meet the needs of various application scenarios.