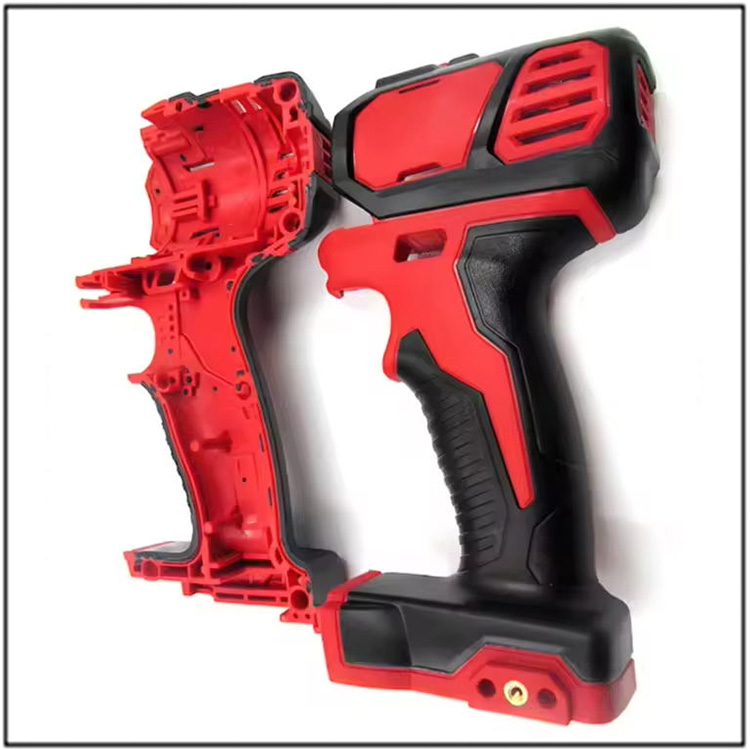
What are The Injection Molding Cycle of Plastic Molds?
What are the stages involved in the injection molding cycle of plastic molds?
The injection molding process of plastic molds is a complex and intricate process that involves multiple key links, aimed at ensuring excellent quality and efficient production of plastic products. The following is an in-depth analysis of the main stages of injection molding technology:
1,Mold closing and locking
The closure of the mold is the primary step in the injection molding process, which includes multiple stages such as rapid closure, medium speed adjustment, low-pressure pre tightening, and high-pressure locking. This process not only requires smooth and steady movements, but also ensures that the mold is effectively protected during the closing process, and ultimately achieves a tight locking state, laying a solid foundation for the subsequent injection molding process.
2,Injection of molten material
The injection process is the core of injection molding technology, which involves the advancement of screws and the extrusion of molten materials. The injection process is divided into two stages: injection and pressure maintenance. During the injection stage, the molten material at the screw head is injected into the mold according to preset parameters, gradually filling the mold space. The pressure holding stage is to cope with the shrinkage of the molten material during the solidification process, by maintaining continuous pressure to ensure the compactness and dimensional stability of the product.
3,Molten material reserve
After the injection is completed, in order to replenish the molten material required for the next injection cycle, a storage operation is required. During the storage process, the screw rotates to transport the material from back to front, and melts it through shearing and heating. As the amount of molten material at the front end of the screw increases, the pressure gradually increases, pushing the screw back to the preset measuring point.
4,Screw retreat adjustment
After the storage is completed, in order to reduce the pressure on the screw head and prevent molten material from overflowing, the screw will actively retreat a small distance. This step is called shot back, which helps maintain the stability and controllability of the injection molding process.
5,Mold cooling and shaping
After injection molding is completed, the plastic mold needs to be cooled to solidify the molten material. The injection molding machine is mainly responsible for timing during this process, while the cooling system on the mold is responsible for heat exchange. The length of cooling time has a direct impact on the molding cycle and production capacity of the product. Therefore, while ensuring product quality, the cooling time should be optimized as much as possible to improve production efficiency.
6,Mold opening and product removal
After cooling is complete, the mold needs to be opened to remove the product. The process of mold opening is divided into multiple stages, including high-pressure opening, rapid opening, medium speed adjustment, and slow stability. The mold opening action should be smooth and steady, ensuring accurate positioning and no shaking when approaching the finish line. Subsequently, the ejector mechanism on the plastic mold pushes the product out, and the ejector pin of the injection molding machine pushes the push plate and ejector pin forward to remove the product from the mold.