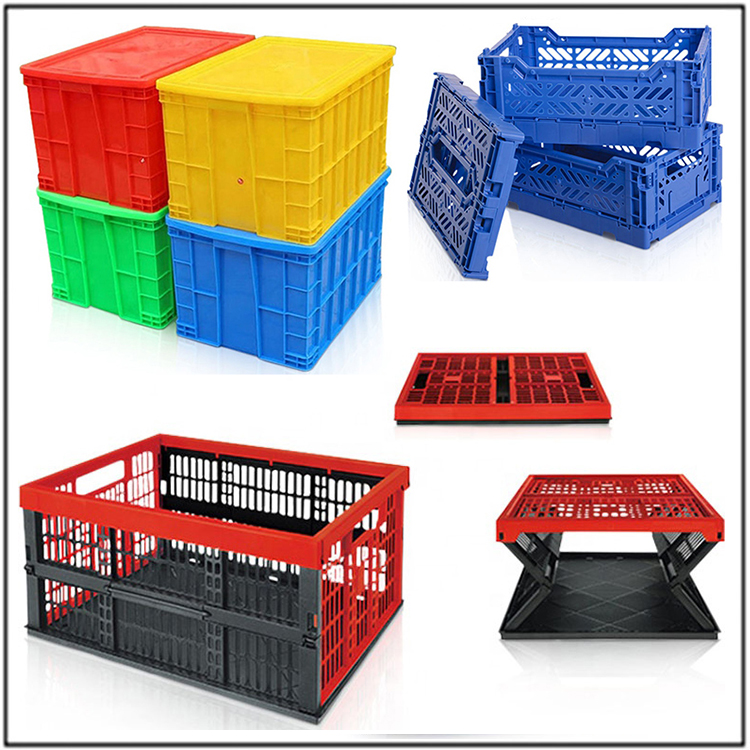
What Are The Sources of Gas in The Plastic Mold Cavity During Injection Molding?
In the process of mold injection molding, the main sources of gas in the mold cavity are as follows:
1.Air stored in the cavity during mold closing: Before the mold is closed, there is usually a certain amount of air left in the cavity. If this air is not discharged in time during the injection molding process, it will become one of the sources of gas in the cavity.
2.Water evaporation in plastics: If the water in plastic raw materials is not fully dried and removed, then at high temperatures during injection molding, this water will evaporate into water vapor, which will then become gas in the mold cavity.
3.Gases produced by plastic decomposition: When the injection molding temperature is high, certain unstable plastics may decompose, resulting in the production of low molecular weight volatile gases. These gases will also remain in the mold cavity.
4.Gases generated by volatilization or chemical reactions of plastic additives: Some additives such as plasticizers, stabilizers, etc. are usually added to plastic raw materials. These additives may evaporate or undergo chemical reactions with each other at high temperatures, generating volatile gases. In addition, thermosetting plastics also release gases during the cross-linking and hardening process.
5.Gas released by plastic volume shrinkage: During the injection molding process, as the plastic cools and solidifies, its volume will shrink. This contraction may cause the gas inside the mold cavity to be compressed or released.
In summary, there are various sources of gas in the mold cavity during injection molding, including air stored in the cavity during mold closing, water evaporation in the plastic, gases produced by plastic decomposition, gases produced by plastic additives evaporation or chemical reactions, and gases released by plastic volume shrinkage. The presence of these gases may have adverse effects on the quality of injection molded products, so appropriate exhaust measures need to be taken during the injection molding process to ensure the quality of the products.