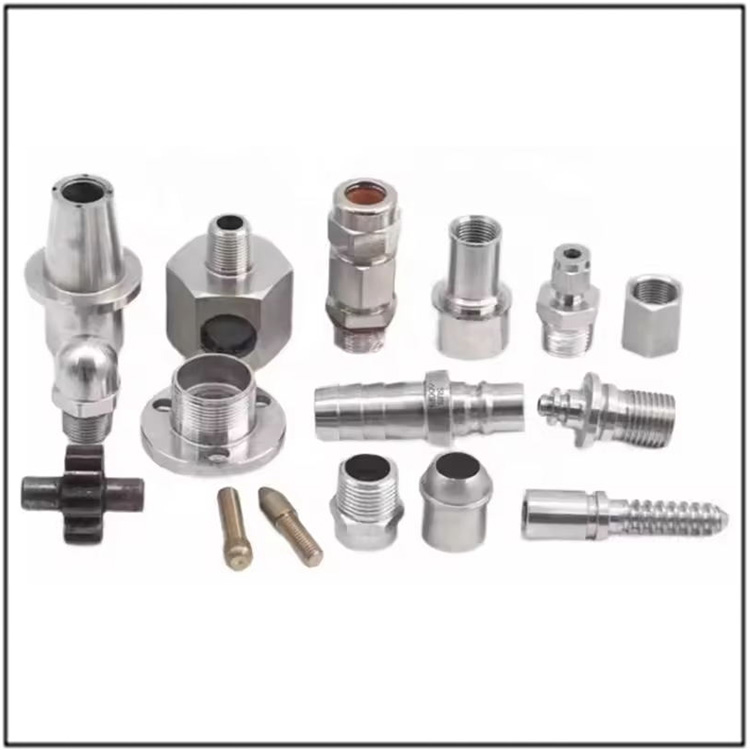
The Machining Process of Precision CNC Mechanical Parts Processing
Precision CNC machining requires high precision. Precision machining has good rigidity, high manufacturing accuracy, and precise tool alignment, so it can process parts with high precision requirements. Precision parts processing cannot complete all surface processing content in one process. The entire processing process of precision CNC machining parts processing can be divided into the following stages:
(1) Rough machining stage. Cut off most of the machining allowance on each processing surface and produce precision standards, mainly considering maximizing productivity.
(2) Semi precision machining stage. Removing possible defects after rough machining to prepare for surface finishing requires achieving a certain level of machining accuracy, ensuring appropriate finishing allowance, and completing the machining of secondary surfaces.
(3) Precision machining stage. At this stage, a high cutting speed, low feed rate, and cutting depth are used to remove the precision machining allowance left by the previous process, so that the surface of the part meets the technical requirements of the drawing.
(4) The finishing stage. Mainly used to reduce surface roughness values or strengthen machined surfaces, mainly used for surface machining with high surface roughness requirements (ra ≤ 0.32 μ m).
(5) Ultra precision machining stage. The machining stage with a precision of 0.1-0.01 μ m and a surface roughness value ra ≤ 0.001 μ m. The main processing methods include precision cutting, mirror surface grinding, precision grinding, and polishing.