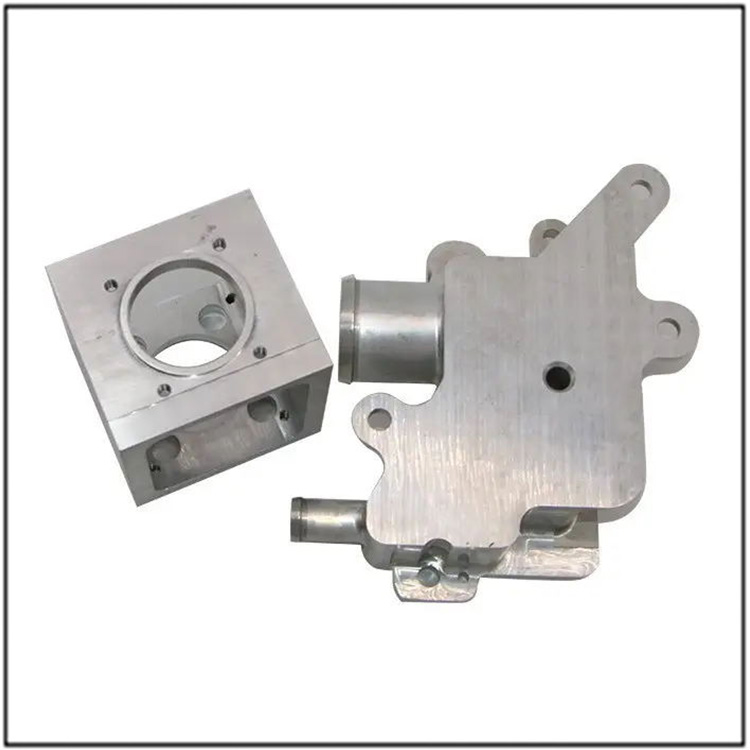
Metal Parts Processing Differences of Six Different Metal Materials
The processing materials are quite extensive, and the materials we commonly use are steel, aluminum, copper, and plastic. ISO standard metal materials are divided into the following 6 types. What are the processing differences of these 6 metal materials?
. P Steel
. M - Stainless Steel
. K - Cast Iron
Non ferrous metals
. S-heat-resistant alloy
H. Quenched steel
(1) P-steel
a. What is steel?
-Steel is the largest material category in the field of metal cutting.
-Steel can be non quenched steel or quenched and tempered steel (with a hardness of up to 400HB).
-Steel is an alloy primarily composed of iron (Fe).
ISO Standard MC Material Review
P1 non alloy steel with a carbon content of less than 0.8%, only iron, and no other alloying elements
P2 low-alloy steel with alloy elements less than or equal to 5%
P3 high alloy steel with alloy elements higher than 5%
P4 cast steel
b. Application Fields
In the field of metal cutting, P group is the largest material group because it covers multiple different industrial fields. This material is usually a long material that can be processed continuously and relatively uniformly.
Low carbon content=hard, sticky material
High carbon content=brittle material
c. Processing characteristics
-Long metal cutting materials.
-Metal cutting is relatively easy and stable.
-Low carbon steel has viscosity and requires sharp cutting edges.
-Unit cutting force: 1500? 3100 N /mm²
-The cutting force and power required to process ISO P materials are within a limited range.
(2) M - Stainless Steel
What is stainless steel?
-Is stainless steel a type with a chromium content of at least 11%? 12% alloy material.
-The carbon content is usually very low (up to 0.01%)
-The alloys are mainly Ni, Mo, and Ti.
-Form a dense Cr2O3 layer on the surface of steel to make it corrosion-resistant
ISO Standard MC Material Review
Medium P5 ferritic/martensitic stainless steel
M1 austenitic stainless steel
M2 super austenitic stainless steel with nickel content ≥ 20%
M3 duplex stainless steel ferrite/austenite
b. Application Fields
In Group M, most applications belong to the oil and gas, pipeline fittings, flanges, processing industry, and pharmaceutical industry.
c. Processing characteristics
-Long metal cutting materials.
-Cutting ferritic metals is relatively smooth, but cutting austenitic and biphasic metals is more difficult.
-Unit cutting force: 1800? 2850 N /mm²
-High cutting force, high heat, and work hardening during the machining process.
(3) K - Cast iron
What is stainless steel?
-There are three main types of cast iron: gray cast iron (GCI), ductile iron (NCI), and compressed graphite cast iron (CGI).
-Cast iron is mainly composed of Fe-C and has a high silicon content (1% ± 3%).
-Carbon content exceeding 2% is the maximum solubility of carbon in austenite.
-Adding chromium (chromium), molybdenum (molybdenum), and vanadium (vanadium) to form carbides increases strength and hardness, but reduces workability.
ISO Standard MC Material Review
K1 malleable cast iron
K2 gray cast iron
K3 ductile iron
K4 vermicular graphite cast iron
K5 austenitic ductile iron
b. Application Fields
K group is mainly used for automotive parts, mechanical manufacturing, and ironmaking.
c. Processing characteristics
-Short metal cutting materials.
-Has good metal cutting control under all working conditions.
-Unit cutting force: 790? 1350 N /mm²
-High speed machining can cause abrasive wear.
-Moderate cutting force.
(4) N - Non ferrous metals
What is non-ferrous metal
-Contains non-ferrous metals and soft metals with a hardness of less than 130 HB.
-Nonferrous metal alloys with silicon content close to 22% account for the largest proportion.
ISO Standard MC Material Review
N1 alloy based on non-ferrous metals
N2 magnesium based alloy
N3 copper based alloy
N4 zinc based alloy
b. Application Fields
Aircraft manufacturing and aluminum alloy wheel manufacturers dominate in Group N.
c. Processing characteristics
-Long metal cutting materials.
-Controlling metal cutting is relatively easy.
-Nonferrous metals are very sticky and require sharp cutting edges
-Unit cutting force: 350? 700 N /mm²
-The cutting force and power required to process ISO N materials are within a limited range.
(5) S-heat-resistant alloy
What is heat-resistant alloy?
-Heat resistant alloys (HRSA) include many high-speed iron, nickel, cobalt, or titanium substrates.
-A higher alloy content (cobalt is higher than nickel) can ensure better heat resistance, higher tensile strength, and higher corrosion resistance.
ISO Standard MC Material Review
Small S1 iron-based alloy
S2 nickel based alloy
S3 cobalt based alloy
S4 titanium alloy
S5 tungsten based alloy
S6 molybdenum based alloy
b. Application Fields
Difficult to process S-group materials are mainly used in the aerospace, gas turbine, and generator industries.
c. Processing characteristics
-Long metal cutting materials.
-Controlling metal cutting is relatively difficult.
-For ceramics, a negative rake angle is required, while for hard alloys, a positive rake angle is required.
-Unit cutting force:
Heat resistant alloy: 2400? 3100 N /mm²
Titanium alloy: 1300? 1400 N /mm²
-High cutting force and power are required.