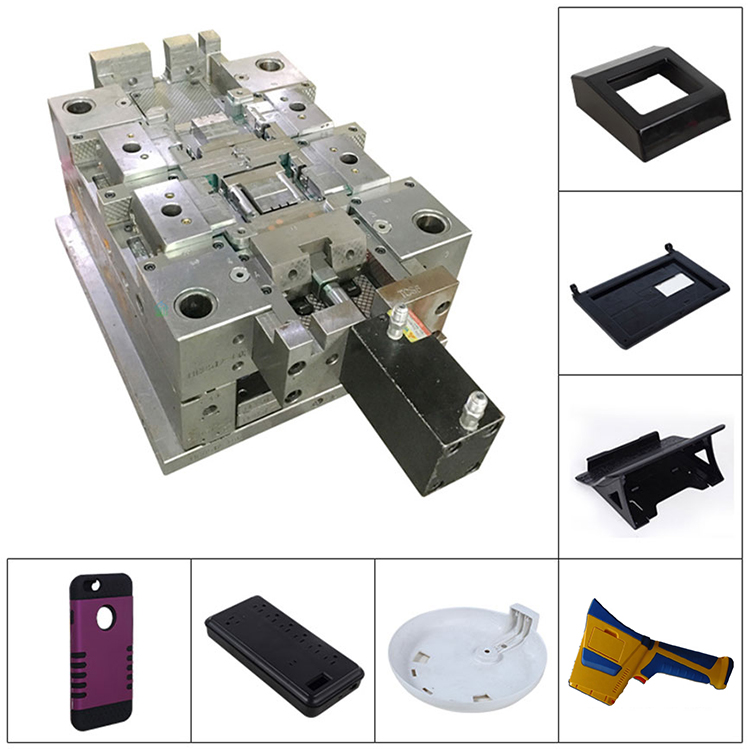
What Are The Requirements For Injection Molding Machines In Precision Injection Molding?
Precision injection molding has extremely strict requirements for injection molding machines, mainly reflected in the following aspects:
1,Accuracy of injection volume
It is usually required that the capacity deviation of the injection molding machine does not exceed about 20% of the tolerance of the injection molded product, in order to ensure that the amount of plastic injected each time is consistent and avoid unstable product dimensions caused by large fluctuations in injection volume.
2,Stability of plasticizing quality
This includes small fluctuations in plasticizing temperature and high precision in temperature control to ensure consistency between the plasticizing degree and temperature of the plastic. High precision temperature control helps ensure the fluidity and formability of plastics during injection molding, thereby improving the quality of products.
3,Accuracy of pressure control
The pressure control device of the injection molding machine needs to have high precision and sensitive response speed to achieve precise pressure control. This helps to reduce shrinkage deformation of the product, improve its density and dimensional stability.
4,Operational stability
The injection molding machine needs to be able to operate continuously for a long time to avoid malfunctions and shutdowns. This requires that all components and systems of the injection molding machine have high reliability and stability to ensure the smooth progress of the production process.
5,The adequacy of maintenance and upkeep
Operators need to strictly follow the equipment operating procedures for operation and maintenance, and conduct regular maintenance and inspections. This includes cleaning equipment, checking the wear and tear of various components, replacing damaged parts, etc., to ensure the normal operation of the equipment and compliance with hygiene requirements.
6,Other special requirements
6-1.Injection pressure: Precision injection molding machines typically require higher injection pressure to increase the density of plastic parts, reduce shrinkage and deformation, and ensure the accuracy of the parts. The injection pressure requirement for general precision injection molding machines is between 216 and 243 MPa, or even higher.
6-2.Injection speed: Injection speed is an important indicator of precision injection molding machines. A higher injection speed helps shorten the molding cycle and improve production efficiency. Meanwhile, the stability and controllability of injection speed also have a significant impact on the quality of the product.
6-3.Temperature control accuracy: Precision injection molding requires extremely high temperature control accuracy. The temperature control system of the injection molding machine needs to have high-precision PID proportional, integral, and derivative control to ensure the temperature stability of the plastic during the injection molding process. The temperature control accuracy is usually required to be within ± 1 ℃, or even higher.
6-4.Hydraulic system response speed: Due to the fact that precision injection molding is usually completed under high injection pressure and high elastic speed, and the filling time is very short, it is required that the hydraulic system of the injection molding machine has a high response speed. This helps ensure consistency between the system output signal and input signal requirements, improving the stability and controllability of the molding process.
6-5.Clamping system stiffness: Precision injection molding machines require a high clamping system stiffness to ensure the stability and accuracy of the mold during the injection molding process. The flatness of the template needs to be maintained within the range of 0.08~0.10mm to ensure the dimensional accuracy and surface quality of the product.