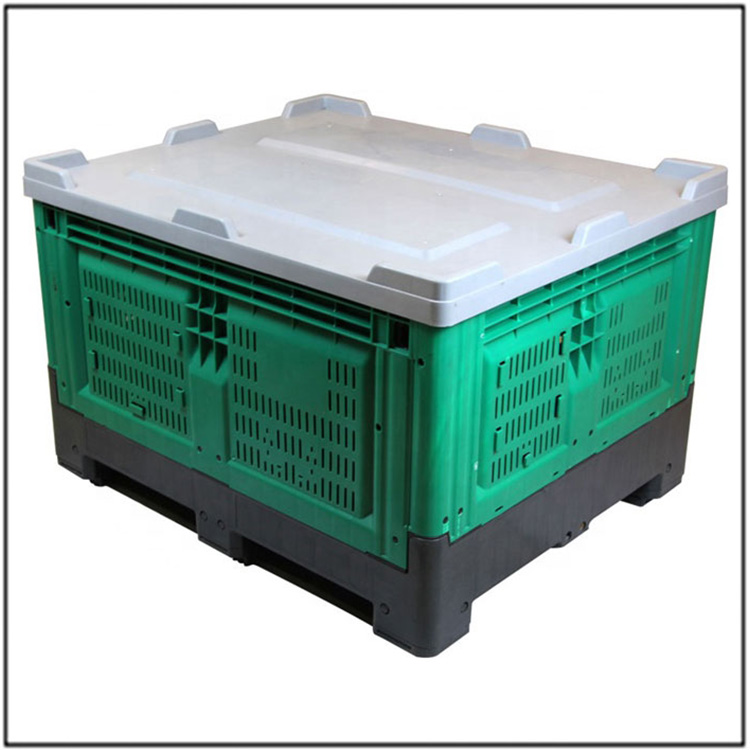
Analysis of Components in Plastic Mold Manufacturing
Analysis of Components and Their Interactions in Plastic Mold Manufacturing
In the precise and complex field of plastic mold manufacturing, the collaborative operation of various components is the key to ensuring efficient and high-quality production of plastic products. The following is a deep analysis of the core components and precision interaction mechanism of plastic mold manufacturing:
1.As the cornerstone of plastic molds, the mold frame has a sturdy structure and reasonable design, providing a stable support platform for the mold. The mold frame is usually composed of upper and lower mold seats, as well as guiding components such as guide columns and guide sleeves, which together ensure the precise alignment and stable operation of the mold during the injection molding process. The size, shape, and material selection of the mold base are based on the design requirements of plastic products and the specifications of injection molding machines to achieve optimal mold compatibility and production efficiency.
2.Mold core, as the core component of plastic molds, directly determines the internal and external shape and dimensional accuracy of plastic products. Mold core is usually composed of two parts: cavity and core, which ensure the high hardness and wear resistance of the mold through precision machining and heat treatment processes. During the injection molding process, molten plastic flows, cools, and solidifies between the cavity and core of the mold, ultimately forming the desired plastic product.
3.The auxiliary components of plastic molds include but are not limited to positioning rings, sprue sleeves, ejector pins, reset rods, etc. These components play a crucial role in the opening and closing process of the mold. The positioning ring and sprue sleeve ensure precise alignment between the injection molding machine nozzle and the mold, avoiding plastic leakage and mold damage. The ejector pin and reset rod are responsible for pushing the plastic product out of the mold after injection molding is completed, ensuring the continuity and efficiency of production.
4.The precision system of plastic molds includes pouring system, ejection system, cooling system, and exhaust system. The pouring system is responsible for introducing molten plastic into the mold cavity, and its design directly affects the molding quality and production efficiency of plastic products. The ejection system is responsible for smoothly ejecting plastic products from the mold, avoiding product damage and mold wear. The cooling system reduces the temperature of the mold through circulating cooling medium, ensuring rapid cooling and solidification of plastic products. The exhaust system is responsible for expelling the air inside the mold cavity and the gas in the plastic melt, avoiding adverse phenomena such as gas marks and burning on the surface of the product.
In the process of plastic mold manufacturing, precise coordination and collaborative operation between various components are the key to achieving efficient and high-quality production. The stable support of the mold frame and mold base provides a stable working environment for the mold core and auxiliary components. The precise construction of the mold ensures the molding accuracy and surface quality of plastic products. The precise coordination of auxiliary components ensures the smooth opening and closing of the mold and the continuity of production. The collaborative operation of precision systems further improves the production quality and efficiency of plastic products.