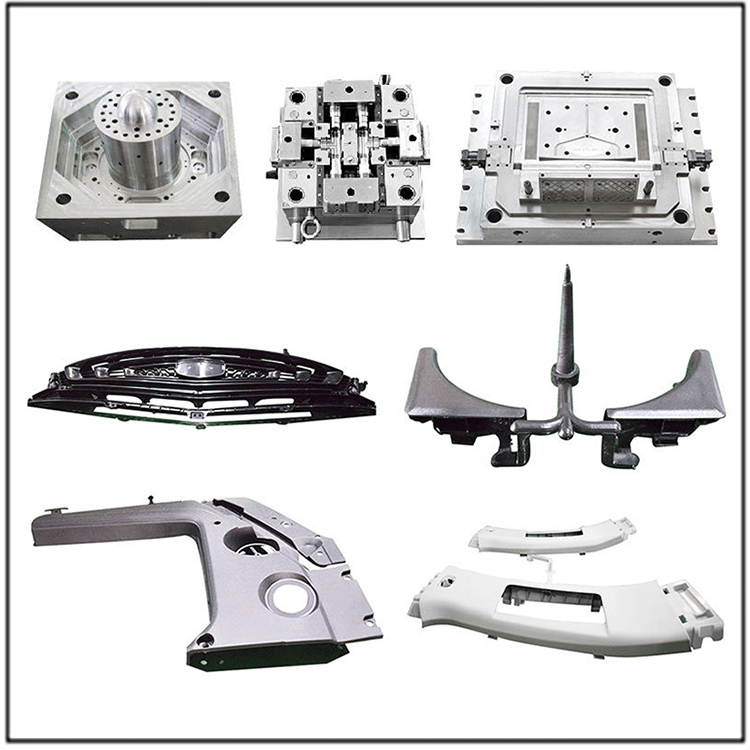
What Are The Items For Plastic Mold Appearance Inspection?
The appearance inspection of plastic molds covers multiple aspects to ensure the quality and performance of the molds. Here are some of the main testing items:
1.Nameplate and identification inspection
1-1.Nameplate content: Check whether necessary information such as mold number, mold weight (KG), mold size (mm), etc. are printed on the mold. These information should be clear in characters and neatly arranged.
1-2.Cooling water nozzle identification: Confirm whether the cooling water nozzle has inlet and outlet markings, with IN for inlet and OUT for outlet, and check if the corresponding serial numbers, such as INI and OUTI, have been added.
2.Inspection of formwork and accessories
2-1.Template identification: Check if each template on the mold frame has a reference angle symbol and if each template has a part number.
2-2.Mold accessories: Check whether the mold accessories (such as oil cylinders, faucets, pre reset mechanisms, etc.) affect the lifting and storage of the mold. If there is an impact, support legs should be used for protection. At the same time, check whether the installation method of the support legs is firm and reliable.
3.Positioning and installation inspection
3-1.Positioning ring: Check whether the positioning ring is securely fixed, whether the diameter meets the requirements (usually 100 or 150mm), and whether it is 10mm higher than the heat shield (or as agreed in the contract). The installation hole of the positioning ring must be a countersunk hole and is not allowed to be directly attached to the top surface of the mold frame.
3-2.Installation direction: For molds with directional requirements, check if the installation direction is marked with an arrow and mark the word "UP" next to the arrow. Arrows and text should be coated with lining and painted yellow, with a height of 50mm.
4.Mold frame and appearance inspection
4-1.Mold frame surface: Check the standard mold frame for defects such as pitting, rust, excess rings, water inlet and outlet, gas, oil holes, etc. that affect the appearance of the product during surface work.
4-2.Chamfering: Check if each panel of the mold frame has a chamfer greater than 1.5mm.
5.Inspection of ejector and closing device
5-1.Top out system: Check whether the cylinder core extraction and top out are controlled by the travel switch, and whether the installation is reliable. At the same time, check if there are any garbage nails, garbage chutes, or dust removal plates on the top needle plate.
5-2.Mold closing device: Check whether the mold closing device is installed reliably, has positioning pins, and is symmetrically installed, with no less than 4 pieces (small molds can have 2 pieces).
6.Three board mold and large mold inspection
6-1.Three board mold: Check if there is a spring assisted mold opening between the front template of the three board mold and the nozzle plate.
6-2.Large mold: Check whether there is interference when closing the mold after the installation of each part of the large mold.
7.Other inspections
7-1.Processing quality: Check whether the processing surface of the mold is flat, and whether there are burrs, cracks, and other problems; Whether the dimensional accuracy meets the design requirements; Whether there are chamfers, whether the hole bottom is smooth, whether the contour is clear, and other issues.
7-2.Auxiliary system: Check whether the lubrication system, cooling system, electrical system and other auxiliary systems are operating normally.
7-3.Safety performance: Check whether there are any safety hazards in the use of plastic molds, such as whether the machine is running normally and whether the emergency cut-off switch is functioning properly.