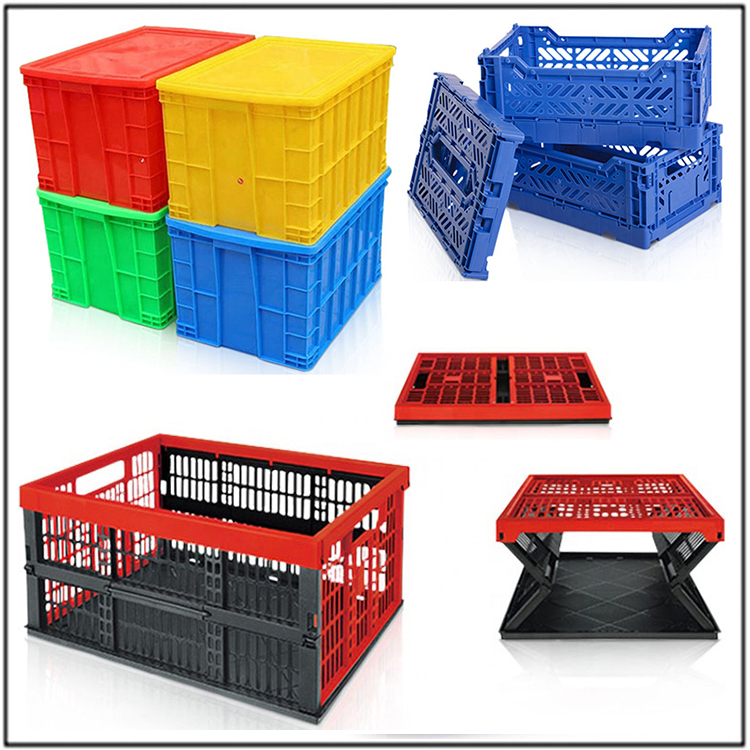
How to Solve The Frequent Breakage of Plastic Mold Ejector Pins ?
In terms of plastic mold design:
Optimize the layout of the ejector pins: Ensure that the ejector pins are arranged reasonably to balance the ejector force as much as possible. Increase the number of ejector pins in areas with complex structures and high demolding forces; Avoid crossing steps or setting ejector pins on slopes; The top pins on both sides of the bone and column positions should be arranged symmetrically as much as possible, and the distance between the top pins and the edges of the bone and column positions should be kept at an appropriate distance, generally around 1.5mm.
Reasonable selection of ejector pin size: When there is sufficient space on the mold, choose a ejector pin with a larger diameter and adjust the ejector pin size to minimize the size specifications. Choose the preferred size series. When the diameter of the ejector pin is less than 2.5mm, a supported ejector pin should be selected to ensure the ejection strength.
Check the design of the top needle hole: The size, roughness, and clearance between the top needle hole and the top needle should be appropriate. It is advisable to have the ejector pin hole 0.01-0.02mm larger than the outer diameter of the ejector pin, and to ensure that the force of the ejector pin passing through and pulling out the male mold core is uniform and unobstructed. When designing, consider using rounded corners or adding stress relief grooves at the variable diameter part of the hole to reduce stress concentration.
In terms of mold manufacturing:
Select high-quality materials: Use needle materials with good quality, high toughness, and strong wear resistance, such as SKH51, SKD61, etc. Avoid using materials with poor quality and brittleness.
Ensure machining accuracy: Strictly control the machining accuracy of the ejector pin and ejector pin hole, ensure the matching accuracy between the ejector pin and ejector pin hole, and avoid uneven force or jamming of the ejector pin due to machining errors.
Proper heat treatment: The ejector pin needs to undergo heat treatment during the manufacturing process to ensure standardized quenching, tempering, and other processes to avoid quality issues such as excessive residual stress.
Regarding the use and maintenance of plastic molds:
Maintain cleanliness: Regularly clean the mold, keep the ejector pin and ejector pin hole clean, and avoid dust, debris, etc. from entering the ejector pin hole, which may affect the normal operation of the ejector pin. Apply anti sticking oil every time the mold is installed. Daily maintenance mainly involves regularly applying lubricating oil or ejector pin oil, but be careful not to apply it forcefully with a brush to avoid oil contamination of the injection molded parts.
Control injection molding process parameters: Reasonably set the ejection speed, pressure, stroke and other parameters of the injection molding machine. The ejection speed and pressure should not be too high, and should be based on the minimum set value at which the product can detach; The ejection stroke is based on the actual ejection distance that can be dropped, and there is no need to reach the limit position; Reduce the number of ejection cycles to avoid mold locking when the ejection plate has not returned to its original position.
Monitoring the operation status of molds: Add mold image protectors and other equipment to monitor the production process in real time, and promptly detect any abnormal situations with the ejector pin, such as bending or jamming, for timely processing.
In terms of plastic mold assembly:
Ensure correct installation of the ejector pin: When installing the ejector pin, ensure its verticality and levelness to avoid lateral forces during operation.
Check the flatness of the mold: The ejector pin plate of the injection molding machine should be kept flat, otherwise it will cause uneven force on the ejector pin. If the top needle plate is bent, it needs to be repaired or replaced in a timely manner.