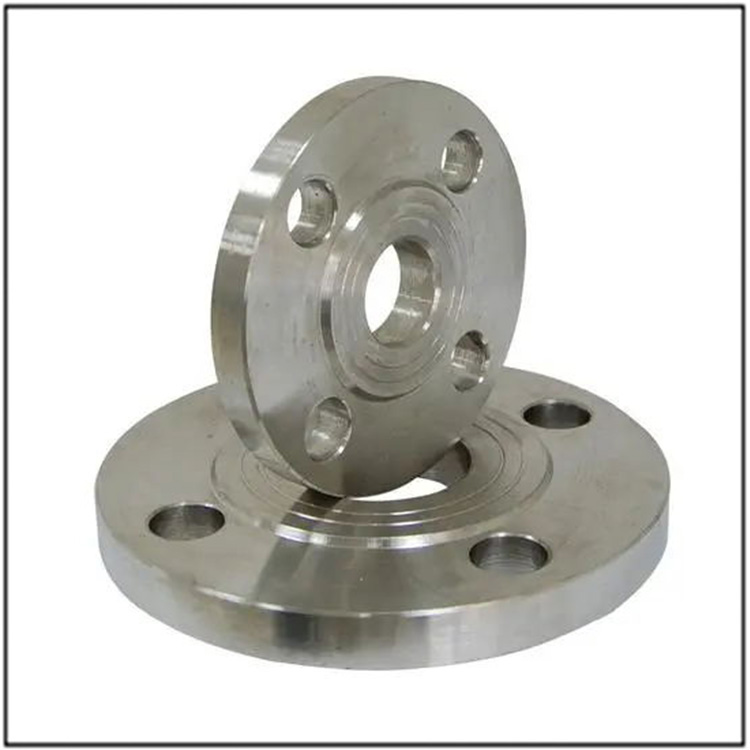
Process Standards and Flow for Precision CNC Machining Parts Processing
Regarding the Process Standards and Process Flow for Precision Machinery Parts Processing
The process of part processing is the direct change of the appearance of raw materials to make them semi-finished or finished products. This process is called the process flow, which is the benchmark for part processing and precision mechanical part processing. This process is more complex.
The machining process standards for precision mechanical parts can be divided into different categories according to different processes, such as casting, forging, stamping, welding, heat treatment, machining, assembly, etc. It refers to the general term for the CNC machining and machine assembly process of the entire part. And other processes such as cleaning, inspection, equipment maintenance, oil seals, etc. are only auxiliary processes. Turning methods change the surface properties of raw materials or semi-finished products, and the CNC machining process is one of the main processes in the industry.
The process standards for precision mechanical parts processing include positioning standards, which are used by CNC lathes or fixtures during machining. Measurement benchmark, which usually refers to the standard of size or position that needs to be followed during inspection. Assembly benchmark, which usually refers to the standard position of parts during the assembly process.
Precision mechanical parts processing requires the production of high-quality and stable products. In order to achieve this goal, the staff must have rich experience in mechanical processing and excellent skills. As is well known, mechanical processing is a delicate job that requires excellent skills to do well.
Secondly, the standardization of the precision machining process also determines the quality of the product. Production and management inevitably require a perfect set of processes, which serve to produce perfect products. Again, communication must be emphasized in the production process, whether it is timing or when there are problems, communication should be strengthened. Communication between processing plants and equipment manufacturers is an important condition for doing a good job in the processing of automation equipment parts.
When precision mechanical parts are machined, digital program controlled contour systems are widely used on milling machines, including phase systems with extensive process capabilities, simple reliability, and low cost. These systems are adopted by many factories, especially for controlling the precision machining of large three-dimensional surfaces.
Proper programming of control programs is one of the main conditions for ensuring the quality of precision mechanical parts processing. For digital program controlled phase systems, the preparation of control programs is carried out by using an automatic program preparation system, and the quality level largely depends on the price of preparing control programs.
Other processing errors are generated when manually controlling equipment, including accidental errors and systematic errors in the process system. Among all processing errors, systematic errors play a major role and can cause a series of CNC machining process system errors for precision mechanical component processing as a whole. For example, gaps, the consequences of gaps are like insensitive belts in the transmission chain of a machine tool, but do not include the amplification factor of unstable transmission caused by reverse transmission chain gaps.
Rainbow is specialized in precision machining of mechanical parts and can customize various precision mechanical components according to customer needs. Its products cover fields such as machinery, electronics, automation, automotive, medical, and new energy. Five axis machining center (DMG), precision machining and testing equipment such as CNC, turn milling composite, slow wire walking, mirror spark machine, internal/external cylindrical grinding, Zeiss coordinate system, height meter, hardness tester, glossiness meter, material analyzer, etc. We have sufficient precision machining equipment and strict quality management system, and the quality of our products can meet global industry standards. Our products are exported both domestically and internationally. The materials we commonly use are stainless steel, aluminum, copper, carbon steel, engineering plastics, and various other alloy steels. We can also provide customers with heat treatment and various surface treatments such as polishing, anodizing, galvanizing, nickel plating, silver plating, passivation, and powder coating.