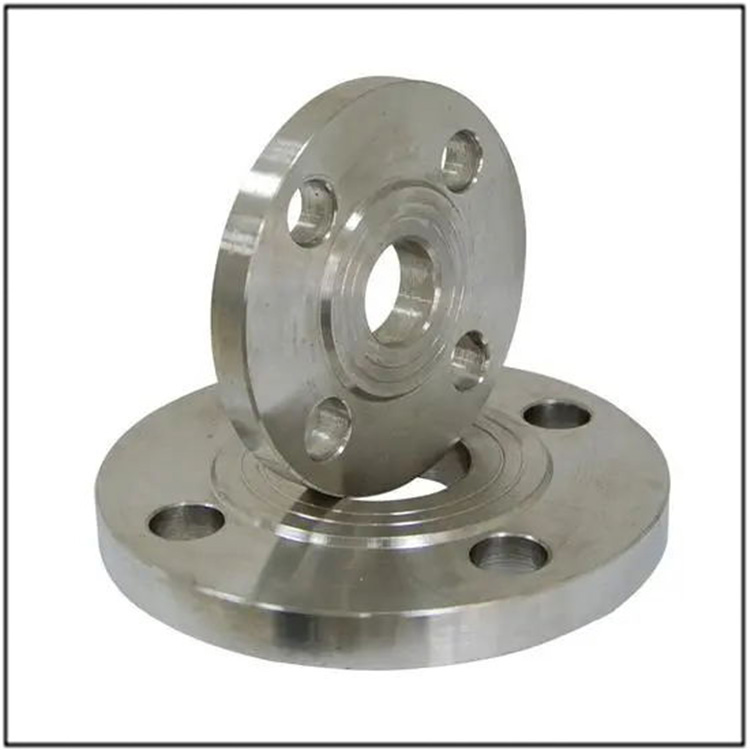
6.How to monitor and adjust during CNC machining process?
After the workpiece is aligned and the program debugging is completed, it can enter the automatic machining stage. During the automatic machining process, the operator should monitor the cutting process to prevent abnormal cutting from causing quality problems and other accidents.
The monitoring of the cutting process mainly considers the following aspects:
The monitoring of the machining process for rough machining mainly considers the rapid removal of excess residue on the surface of the workpiece. In the automatic machining process of machine tools, the cutting tool automatically cuts according to the predetermined cutting trajectory based on the set cutting parameters. At this time, the operator should pay attention to observing the changes in cutting load during the automatic machining process through the cutting load table, adjust the cutting amount according to the tool's bearing capacity, and maximize the efficiency of the machine tool. Monitoring of cutting sound during the cutting process. In automatic cutting, the sound of the cutting tool cutting the workpiece is generally stable, continuous, and light at the beginning of cutting, and the movement of the machine tool is smooth at this time. As the cutting process progresses, when there are hard spots on the workpiece, tool wear, or tool clamping, the cutting process becomes unstable. The manifestation of instability is that the cutting sound changes, and there will be collision sounds between the tool and the workpiece, causing the machine tool to vibrate. At this time, the cutting amount and cutting conditions should be adjusted in a timely manner. When the adjustment effect is not obvious, the machine tool should be paused to check the condition of the cutting tools and workpieces. The precision machining process should be monitored to ensure the machining size and surface quality of the workpiece. The cutting speed should be high and the feed rate should be large. At this point, special attention should be paid to the impact of chip deposits on the machined surface. For cavity machining, attention should also be paid to over cutting and tool allowance at corners. To solve the above problems, firstly, attention should be paid to adjusting the spraying position of the cutting fluid to keep the machined surface in a cooling condition at all times; Secondly, it is important to observe the quality of the machined surface of the workpiece and adjust the cutting parameters to avoid any changes in quality as much as possible. If the adjustment still has no significant effect, the machine should be stopped to check whether the original program is reasonable. Special attention should be paid to the position of the tool when pausing or stopping the inspection. If the cutting tool stops during the cutting process and the spindle suddenly stops rotating, it will cause tool marks on the surface of the workpiece. Generally, shutdown should be considered when the tool leaves the cutting state. The quality of tool monitoring largely determines the machining quality of the workpiece. In the process of automatic machining and cutting, it is necessary to determine the normal wear condition and abnormal damage condition of the tool through methods such as sound monitoring, cutting time control, pause inspection during the cutting process, and surface analysis of the workpiece. According to the processing requirements, the cutting tools should be processed in a timely manner to prevent processing quality problems caused by untimely processing of the tools. How to choose machining tools reasonably? What are the major elements of cutting quantity? 7.How many types of cutting tools are there? How to determine the rotational speed, cutting speed, and cutting width of the tool?
When milling flat surfaces, non regrinding hard alloy end mills or end mills should be selected. When milling, it is recommended to use a secondary cutting method. For the first cutting, it is best to use an end mill for rough milling, and to continuously cut along the surface of the workpiece. The recommended width for each cutting is 60% -75% of the tool diameter. End mills with end mills and carbide inserts are mainly used for machining bosses, grooves, and box mouth surfaces. Ball knives and round knives (also known as round nose knives) are commonly used for machining curved surfaces and variable angle contour shapes. And ball cutters are mostly used for semi precision machining and precision machining. Round knives with embedded hard alloy cutting tools are often used for rough cutting.
8.What is the function of a processing program sheet? What should be included in the processing program sheet?
The machining program sheet is one of the contents of CNC machining process design, and it is also a regulation that operators need to follow and execute. It is a specific description of the machining program, with the purpose of allowing operators to clarify the content of the program, clamping and positioning methods, and issues that should be noted when selecting cutting tools for each machining program. In the machining program sheet, it should include: drawing and programming file names, workpiece names, clamping sketches, program names, tools used in each program, maximum cutting depth, machining properties (such as rough machining or precision machining), theoretical machining time, etc.
9.What preparations should be made before CNC programming?
After determining the processing technology, it is necessary to understand:
Workpiece clamping method; The size of the workpiece blank - in order to determine the processing range or whether multiple clamping is required; The material of the workpiece - in order to select which cutting tool to use for processing; What are the tools in stock? To avoid modifying the program due to the lack of such tools during processing, if it is necessary to use this tool, it can be prepared in advance.
What are the principles for setting a safe height in programming?
The principle of setting a safe height: generally higher than the highest surface of the island. Alternatively, the programming zero point can be set to the highest surface to minimize the risk of tool collision.
10.Why do post-processing still need to be done after the tool path is created?
Because different machine tools can recognize different address codes and NC program formats, it is necessary to choose the correct post-processing format for the machine tool used to ensure that the program can run.
There are three major elements of cutting parameters: cutting depth, spindle speed, and feed rate The overall principle for selecting cutting parameters is: cutting less, fast feed (i.e. cutting depth is small, feed rate is fast). According to material classification, cutting tools are generally divided into ordinary hard white steel tools (made of high-speed steel), coated tools (such as titanium plated tools), and alloy tools (such as tungsten steel, boron nitride tools, etc.).