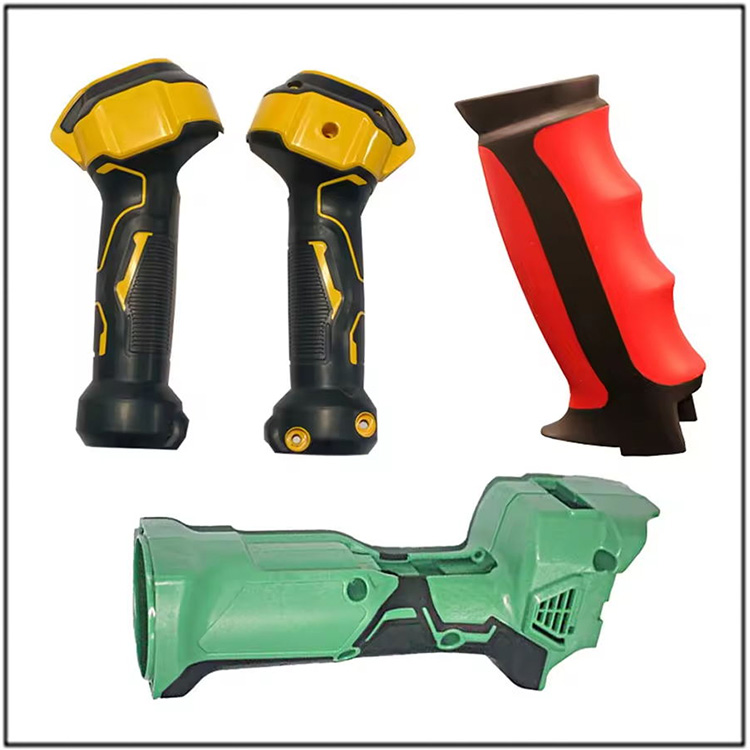
The Main Reasons For Rust Spots On Plastic Injection Molds
The main reasons for rust spots on plastic injection molds include the following:
1.Plastic melt decomposition: When the temperature of the molten material in the barrel is too high, many raw materials will produce volatile gases due to overheating. This gas has strong corrosiveness and can corrode molds and machines.
2.Carbides generated by injection molding: After the mold works for a long time, carbides that precipitate or decompose from the melt will adhere to the mold cavity. They have greater hardness and corrosiveness, often causing mold corrosion or wear.
3.Cooling water: Cooling water needs to be introduced into the mold for cooling. If the cooling water cools the mold below freezing point, the moisture in the air will condense into water droplets on the surface of the injection mold. These water droplets can easily cause rusting of the mold.
4.Defects in electroplating layer: If the electroplating process is not handled properly, resulting in loose electroplating layer and loose structure, volatile corrosive gases may enter the bottom of the electroplating layer through analysis of these basic weaknesses, causing corrosion of the coating.
5.Storage environment: If the mold is stored in humid air, oxygen and water molecules will form oxides on the surface of the mold, causing it to rust.
6. Improper cleaning: If the mold is not cleaned thoroughly and rust inhibitor is used directly, it may cause some weak acid substances to remain on the inner wall of the mold, leading to corrosion and rusting of the mold.
To address the issue of rust spots on injection molds, the following measures can be taken:
6-1.Control the temperature of the material barrel: Avoid excessive temperature of the material barrel, which may cause the decomposition of plastic melt and produce corrosive gases.
6-2.Timely cleaning of carbides: Once carbides are found on the mold, they should be immediately wiped off with a dry cloth. If it is difficult to remove, a strong mold cleaner can be used for cleaning.
6-3.Manage cooling water: It is best not to stop molding operations arbitrarily during the production process. If you want to stop, you should also turn off the cooling water in a timely manner. If water droplets are found on the injection mold, they should be wiped dry in a timely manner.
6-4.Handling plating defects: reprocess the plating layer or apply a drug-resistant adhesive to fill loose areas to improve the rust prevention ability of the mold.
6-5.Improve storage environment: Store the molds in a clean, ventilated, and dry place to avoid direct exposure to humid air.
6-6.Proper cleaning of molds: After the injection molding production cycle is completed, the molds must be disassembled and cleaned according to standard procedures. After cleaning, spray rust inhibitor evenly.
In addition, if rust spots have appeared on the surface of the injection mold, professional cleaning agents can be used for cleaning. For example, MOULD FRESH cleaning agent, whose main ingredient is abrasive material, is safe and environmentally friendly. When using MOULD FRESH to clean rust spots, the cleaning agent components will quickly penetrate the rust spots, and the extremely fine grinding factor in the product will physically rub against the rust spots. Under the double-layer cleaning effect, the rust spots can be quickly removed. However, please note that rust cleaning can only be used as an emergency measure, and daily attention to rust prevention and maintenance is the long-term solution.