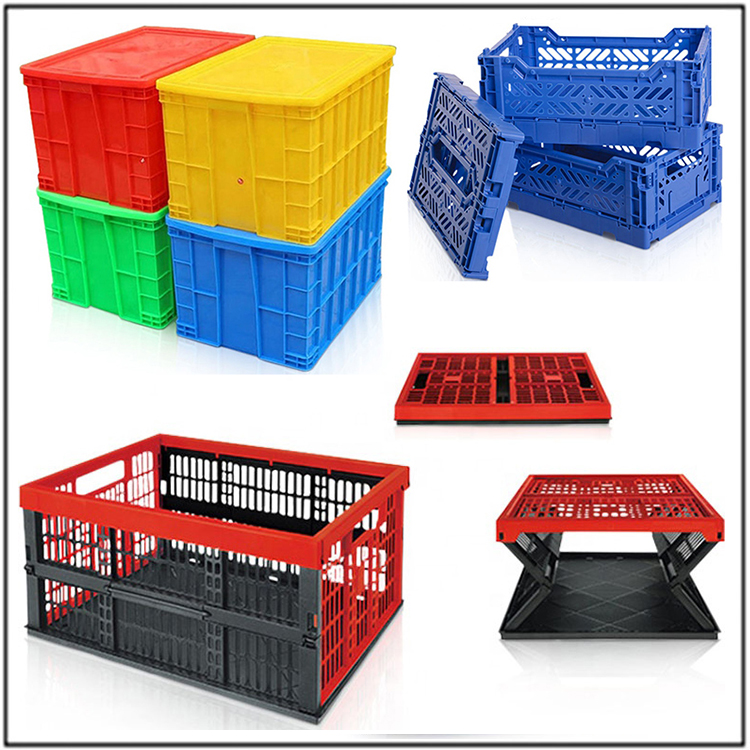
How To Solve The Plastic Deformation Problem Caused By Injection Molding?
Injection molding is an efficient processing technology for polymer composite materials, widely used in the production of plastic products. However, plastic deformation often occurs during the injection molding process, which not only affects the appearance quality of the product, but may also affect its performance. This article will explore how to effectively deal with plastic deformation problems in injection molding, helping manufacturers improve product quality and production efficiency.
1.The causes of the plastic deformation
During the injection molding process, plastic deformation is mainly caused by the following factors:
1-1.Poor demolding: The uneven distribution of stress field during mold demolding can easily lead to product deformation.
1-2.Improper forming specifications: Excessive injection pressure, uneven mold temperature, improper resin temperature, etc. can all generate residual stress and cause deformation.
1-3.Uneven cooling: Insufficient cooling time or improper cooling method can result in uneven cooling of the product, leading to deformation.
1-4.Mold design issues: Unreasonable mold design, such as uneven wall thickness and improper gate position, can also lead to product deformation.
2.Specific methods for handling plastic deformation
1-1.Optimize demolding design
Regarding the deformation caused by poor demolding, it can be improved by increasing the number of swing rods or occupying an area, and setting a reasonable demolding slope. At the same time, in the mold design stage, the deformation trend of the product is predicted through mold flow analysis, and the design is optimized to facilitate subsequent process adjustments.
1-2.Adjust the forming specifications
Reducing injection pressure, increasing mold temperature and ensuring uniform distribution, raising resin temperature or using heat treatment methods can effectively eliminate residual stress and reduce deformation. For example, when the material flowability improves after increasing the barrel temperature and mold temperature, the injection pressure should not be too high. At the same time, extending the cooling time appropriately while the material fluidity improves can also help eliminate internal stress.
1-3.Improve the cooling method
Improper cooling method is a common cause of deformation. Adjusting the cooling method to ensure even cooling of the product is an important measure to avoid deformation. By increasing the depth of the cooling water holes, the product can be cooled more evenly. At the same time, sufficient cooling and solidification inside the mold, and appropriately extending the cooling time, can help reduce deformation.
1-4.Optimize mold design
During the mold design phase, special attention should be paid to the uniformity of the product's wall thickness to avoid deformation caused by significant differences in wall thickness. At the same time, setting up gates in areas with high product thickness, avoiding straight line design, creating large R-curves, increasing the number of ejector pins, and demolding slopes can all help reduce deformation.
3.Material selection and precautions
Different resin materials have different shrinkage rates and stress characteristics. Crystalline materials (such as polyethylene, polypropylene, nylon, etc.) have a high shrinkage rate during molding and are prone to deviation; Non crystalline materials such as polystyrene, ABS, etc. are prone to residual stress. Therefore, when selecting materials, it is necessary to choose them reasonably according to product requirements and take corresponding measures.
In addition, after molding, using a corrector at room temperature can slightly prevent deformation, but it cannot have a significant impact on development. For thin products, attention should be paid to the bending caused by the molding temperature, which is usually due to thermal expansion.