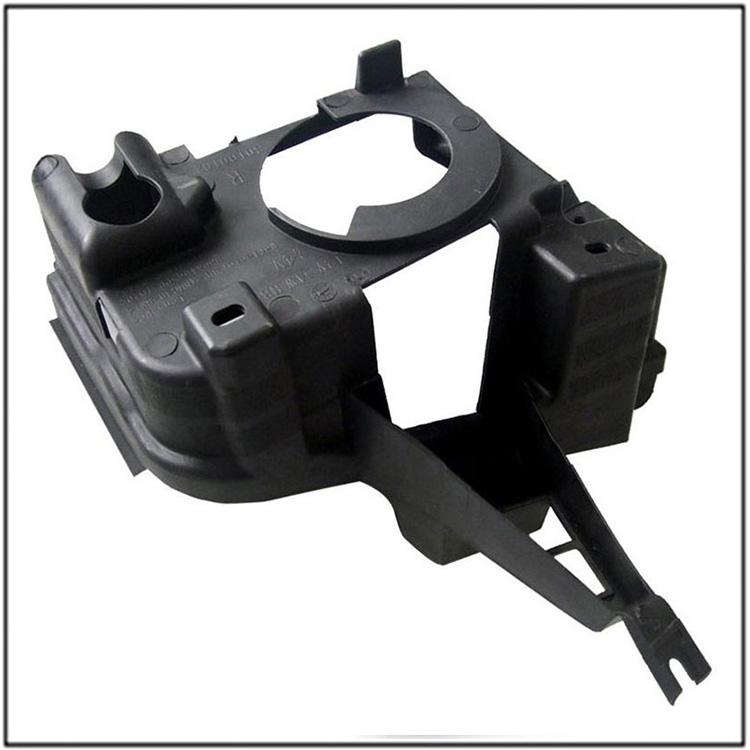
Process Knowledge Points of PPS Injection Molding
Speaking of injection molding, I believe everyone is familiar with it. Many of the commonly seen molded products in our daily lives are made through injection molding technology, and PPS injection molding is one of the injection molding processes that involves precise control of multiple process parameters to ensure the quality and performance of the final product. The following is a detailed analysis of the knowledge points of PPS injection molding process:
·1.PPS material characteristics
·High temperature resistance: PPS has excellent heat resistance and can be used for a long time in the temperature range of 180 ℃~220 ℃, with a thermal deformation temperature of up to 260 ℃.
·Corrosion resistance: PPS has a corrosion resistance similar to polytetrafluoroethylene and can resist corrosion from various acids, alkalis, salts, and organic solvents.
·Mechanical properties: PPS has excellent mechanical properties, especially after being reinforced and modified with glass fibers, its impact strength, tensile strength, and other properties are significantly improved.
·Electrical performance: PPS has excellent electrical insulation performance, high resistivity, low dielectric constant, and is suitable for electrical insulation materials.
·Flame retardancy: PPS has good flame retardancy, with an oxygen index of up to 46%~53%, making it a highly flame-retardant material.
2. Injection molding process parameters
2-1. Barrel temperature
·To prevent material oxidation and discoloration, the temperature should not be too high, usually between 310 ℃ and 340 ℃. Large components use lower barrel temperatures, while small components use higher barrel temperatures.
2-2. Mold temperature
·The mold temperature has a significant impact on the crystallinity and product performance of PPS, and it is generally recommended to use a temperature range of 140 ℃ to 170 ℃. A higher mold temperature can achieve higher crystallinity, but attention should be paid to avoiding problems such as product shrinkage and indentation.
2-3. Injection pressure
·PPS products with high injection pressure are preferred, especially for complex thin-walled parts. The injection pressure is usually between 80 and 150 Mpa
2-4. Injection speed
·The faster the injection speed, the better the surface glossiness of the product, but it is prone to phenomena such as product warping, overflow, and burning. Therefore, a moderate injection speed is generally used.
2-5. Holding pressure
·In order to prevent internal pressure, the holding pressure should be as low as possible, and the judgment criteria should be based on the absence of defects such as bubbles, dents, and material shortages in the product.
2-6. Screw speed
·The screw speed during PPS injection molding is generally 40-110r/min. Although higher rotational speeds can be used during high cycle molding, it is necessary to simultaneously reduce the temperature of the barrel to prevent resin degradation due to shear heating.
2-7. Molding cycle
·The typical cycle for thin-walled molding is 20-30 seconds. When thin-walled forming, in order to improve crystallinity and mechanical properties, it is necessary to extend the cooling time appropriately.
3.Precautions
3-1. Annealing treatment
·For products formed at low temperatures, annealing treatment can be performed to improve their performance, eliminate internal stress, and maintain product performance and dimensional stability. The annealing temperature is usually 200 ℃ and 240 ℃, with a duration of 24 hours.
3-2. Mold design
·When designing molds, the high temperature characteristics of PPS should be considered, and the heating temperature of the mold should be higher than 130 ℃. Mold steel should undergo heat treatment hardening to reduce wear. The mold must be fully ventilated and equipped with exhaust slots to avoid insufficient filling and mold corrosion.
3-3. Gate design
·PPS molded products have high hardness and low molding shrinkage, so submersible gates cannot be used. Circular, trapezoidal, or edge type gates can be used, and consideration should be given to setting up cold material wells to collect cold materials.
3-4. Use of recycled materials
·The proportion of recycled materials used depends on the required performance of the molded product, generally not exceeding 30%. Excessive proportion of recycled materials may lead to a decrease in product performance.
3-5. Drying conditions
·PPS should be dried before processing, with a recommended drying temperature of 150 ℃ to 160 ℃ and a duration of 23 hours. To remove moisture and volatile substances from the material and improve processing performance.