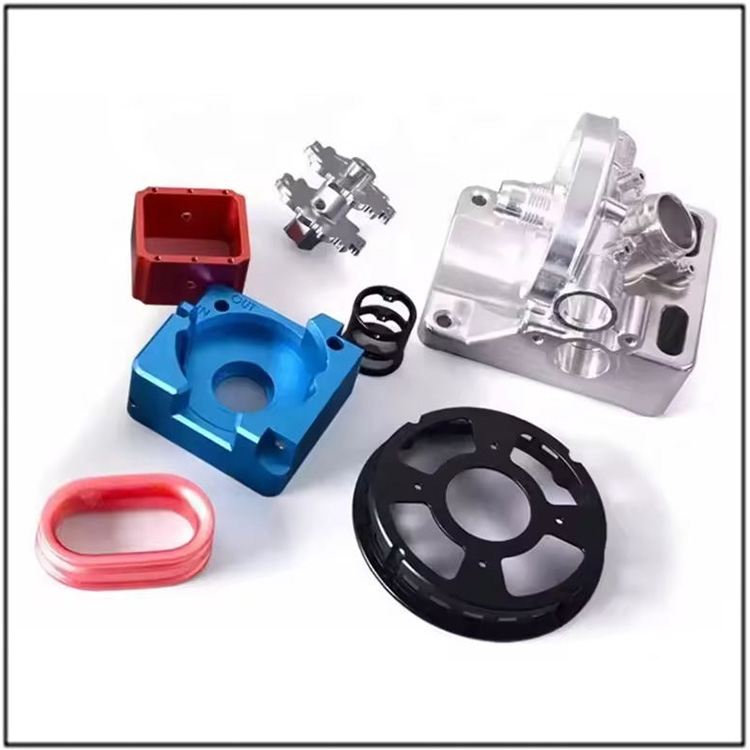
Diversity of CNC Prototype Model Processing Methods
With the gradual growth of the prototype industry, manufacturing processes are also constantly updated, including 3D printing and silicone replication. However, CNC machining remains the most common way of producing parts. There are currently several common methods for CNC machining of prototype models, including:
1.Turning
Turning simply involves firmly clamping the workpiece onto a rotating plate or spindle. When the workpiece rotates, the cutting tool is fixed against it in a fixed device installed on the moving slider. The slider can move up and down along the length of the workpiece, as well as closer or farther away from the centerline, making this simple operation ideal for quickly removing large amounts of material. In addition, the drill bit installed on the lathe tailstock can drill precise holes; A lathe is used to form concentric shapes on the outer circumference of circular components; Manufacturing grooves, ring grooves, step shoulders, internal and external threads, cylinders, and shafts on lathes - many circular or circular features.
2.Milling
Milling is fundamentally different in that the workpiece remains stationary and the cutting tool rotates on the spindle. The workpiece is usually held horizontally in a machine vise and installed on a worktable that moves in the X and Y directions. The spindle can hold various cutting tools and move on the X, Y, and Z axes. Milling cutters are used to manufacture squares/planes, notches, chamfers, channels, profiles, keyways, and other features that rely on precise cutting angles. Like all metalworking operations, cutting fluid is used to cool workpieces and cutting tools, lubricate them, and flush away metal particles or chips.
3.Grinding
Grinding to create very flat surfaces on metal parts is important for many applications, and the best way to manufacture such precise surfaces is to use a grinding machine. A grinder is a rotating disc covered with abrasive grains of specific roughness. The workpiece is installed on the worktable and moves laterally back and forth on the sliding table below the grinding wheel, or sometimes remains stable while the grinding wheel is moving. Depending on the material being ground, different types of abrasives are used. The thermal and mechanical stresses during the grinding process may adversely affect the workpiece, so careful control of tool speed and temperature is necessary.
4.EDM
Solid EDM is used to create pits, holes, and square features inside hardened tool steel, which is difficult, if not impossible, to achieve in any other way. It is usually used for plastic injection and pressure molding molds, and is rarely used for finished parts themselves. EDM is also used to create textured surfaces or recessed letters and logos on molds.
5.Wire cutting
Wire cutting uses copper wire as a conductor for high-voltage charges. Due to the stable corrosion of the conductor during the cutting process, new wire is supplied from the spool. This technology requires approval and cannot be used for blind holes. Wire cutting is used on thick, hardened tool steel to create circular or semi-circular features, which will be very difficult to manufacture with conventional cutting tools.
6.Optical grinding
We only discuss optical grinding for processing metals, but CNC machining is also used for manufacturing special optics for glass or plastic. Optical devices require very fine surfaces with very tight tolerances, so specialized grinding equipment is used to rotate the grinding wheel relative to the surface on multiple axes.
By using the manufacturing and processing methods of the above-mentioned prototype models, the quality of CNC products produced by many prototype processing factories has been rapidly improved, thus reaching the world.