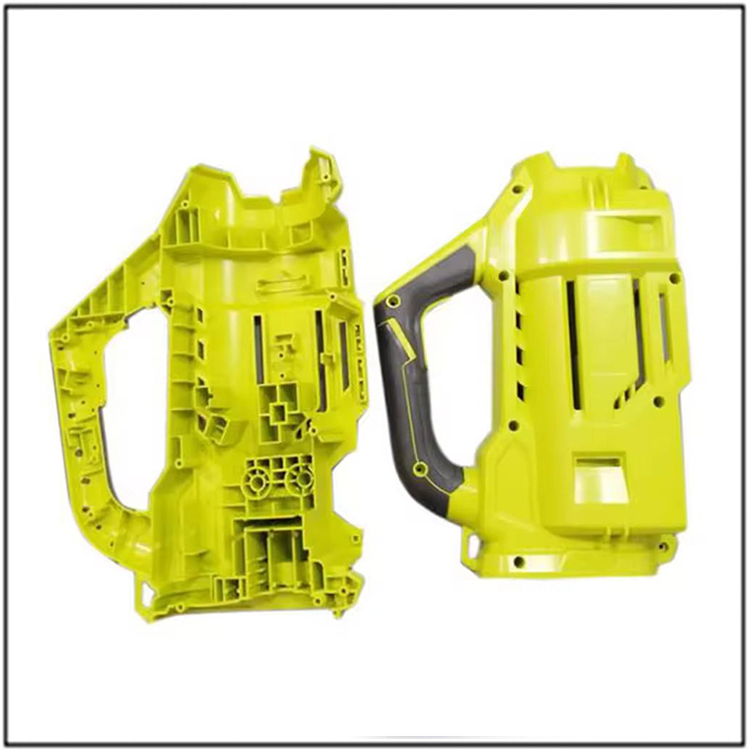
Shrinkage Rate of ABS Plastic In Plastic Molds
The shrinkage rate of ABS plastic in plastic molds is an important process parameter that directly affects the dimensional accuracy and appearance quality of injection molded products. The shrinkage rate of ABS (acrylonitrile butadiene styrene copolymer) is influenced by various factors, including the type of material, molding process, mold design, and environmental conditions.
Generally speaking, the shrinkage rate of ABS plastic is usually between 0.4% and 0.9%, but the specific value may vary depending on different ABS varieties, molding processes, and molding conditions. For example, data shows that the actual mold shrinkage rate of ABS plastic under certain specific conditions is 0.0045 (0.45%), while in other cases it may be 0.005 (0.5%) or higher. These differences mainly stem from differences in process parameters such as material formulation, molding temperature, pressure, and cooling time.
In addition, it should be noted that the shrinkage rate is not a fixed and unchanging value, and it will fluctuate within a certain range. Therefore, in the process of mold design and injection molding, it is necessary to fully consider the shrinkage rate of ABS plastic and take corresponding measures to reduce its impact, in order to ensure the dimensional accuracy and appearance quality of the product.
To more accurately control the shrinkage rate of ABS plastic, the following measures can be taken:
1. Increasing the molding temperature: Properly increasing the molding temperature can increase the flowability of ABS and help reduce shrinkage. However, it should be noted that excessively high temperatures may cause defects such as plastic decomposition or the formation of bubbles.
2. Extending the molding time: Properly extending the molding time can allow the plastic to fill the mold more fully, thereby reducing the shrinkage rate. However, excessively long molding time can reduce production efficiency, so it is necessary to find a balance point.
3. Optimize mold design: Reasonable mold design can reduce the shrinkage rate of ABS. For example, increasing the wall thickness of the mold, optimizing the flow channel design, and adding support structures can effectively reduce the shrinkage rate.
4. Control environmental conditions: Maintaining stable environmental temperature and humidity conditions can reduce the dimensional changes of ABS plastic during injection molding.
In summary, the shrinkage rate of ABS plastic in plastic molds is a complex parameter influenced by multiple factors. In practical applications, it is necessary to comprehensively consider and adjust according to specific situations to ensure the quality and dimensional accuracy of the product.