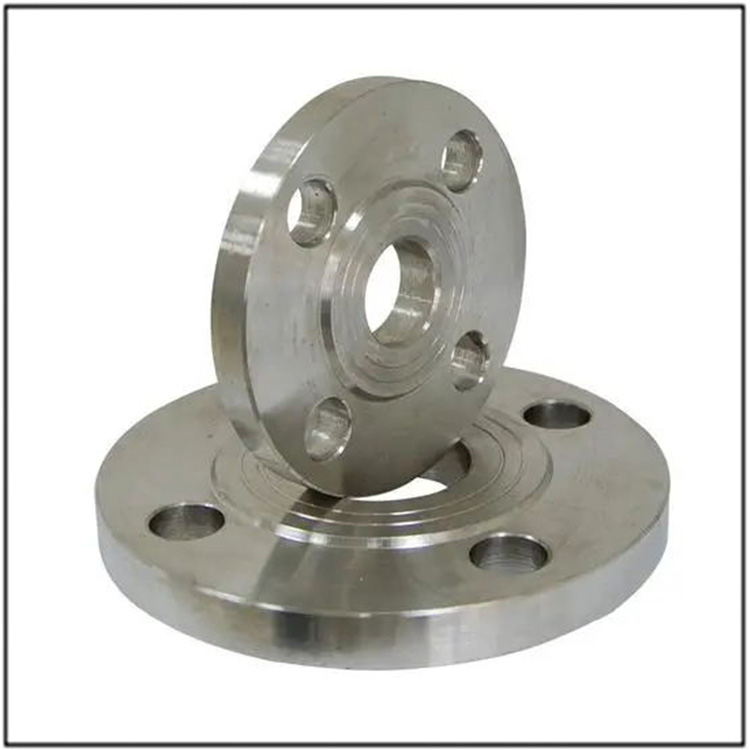
In the vast starry sky of manufacturing, CNC (Computer Numerical Control) precision parts machining is like a shining star, leading the trend of modern industrial production with its high precision, efficiency, and flexibility. This technology not only profoundly changes the face of mechanical processing, but also greatly promotes the improvement of product quality and the reduction of manufacturing costs. This article will delve into the technical principles, application areas, machining processes, quality control, and future development trends of CNC precision parts machining, taking you into the world of precision manufacturing.
1.Technical principle: Perfect integration of digital and mechanical elements
The core of CNC precision parts machining lies in the close integration of computer technology with traditional mechanical machining techniques. Through pre written machining programs, CNC machine tools can automatically perform various complex cutting, drilling, milling and other process operations. The key to this process is to convert the two-dimensional or three-dimensional models on the design drawings into machine recognizable codes, namely G code and M code. These codes provide detailed descriptions of the tool's motion trajectory, speed, feed rate, and other parameters, ensuring the accuracy of the machining process.
2.Application areas: extensive and in-depth
The application fields of CNC precision parts machining are extremely wide, covering almost all industries that require high-precision and complex shaped parts. In the aerospace field, CNC machining technology is used to manufacture key components such as engine parts and precision instruments, ensuring the safety and performance of aircraft; In the automotive manufacturing industry, it helps achieve lightweight body, improve fuel efficiency, and endow cars with smoother lines and personalized designs; In addition, CNC machining also plays an irreplaceable role in fields such as medical equipment, electronic devices, and mold manufacturing.
3.Processing Flow: A Precise Journey from Design to Finished Product
The machining process of CNC precision parts can be roughly divided into the following steps: firstly, design according to product requirements and use CAD (computer-aided design) software to draw the three-dimensional model of the part; Subsequently, the CAD model was converted into executable G-code for the machine tool using CAM (Computer Aided Manufacturing) software; Next, import the G code into the CNC machine for debugging and setting up the machine; Finally, start the machine tool and begin the machining process until all preset cutting actions are completed to obtain the finished parts. Strict process control and precise machine tool equipment are key to ensuring machining quality throughout the entire process.
4.Quality control: precise control of every detail
The quality control of CNC precision parts processing involves multiple aspects. Starting from the selection of raw materials, it is necessary to ensure that the physical properties and chemical composition of the materials meet the design requirements. During the machining process, real-time monitoring of cutting force, temperature, vibration and other parameters is used to adjust machining parameters in a timely manner, avoiding problems such as tool wear and workpiece deformation. At the same time, advanced measuring tools and methods such as coordinate measuring machines and laser interferometers are used to accurately measure the processed parts, ensuring that the dimensional accuracy, form and position tolerances meet the design requirements. In addition, establishing a sound quality management system and implementing strict inspection procedures are also important means to ensure processing quality.
5.Future Development Trends: Intelligence, Greening, and Efficiency
With the advancement of technology and the transformation and upgrading of the manufacturing industry, CNC precision parts machining is developing towards intelligence, greenness, and efficiency. In terms of intelligence, by integrating technologies such as the Internet of Things, big data, and artificial intelligence, remote monitoring, fault diagnosis, and predictive maintenance of machine tools can be achieved, improving production efficiency and equipment utilization; In terms of greening, promote the use of environmentally friendly materials, optimize cutting processes, improve energy utilization efficiency, and reduce environmental pollution during the processing; In terms of efficiency, by improving the processing speed, accuracy, and stability of machine tools, shortening the processing cycle, and reducing production costs.
In short, as an important component of modern manufacturing, the importance of CNC precision parts machining is self-evident. With the continuous advancement of technology and the expansion of application fields, we have reason to believe that CNC machining technology will play a more important role in the future, contributing greater strength to the prosperity and development of the manufacturing industry.