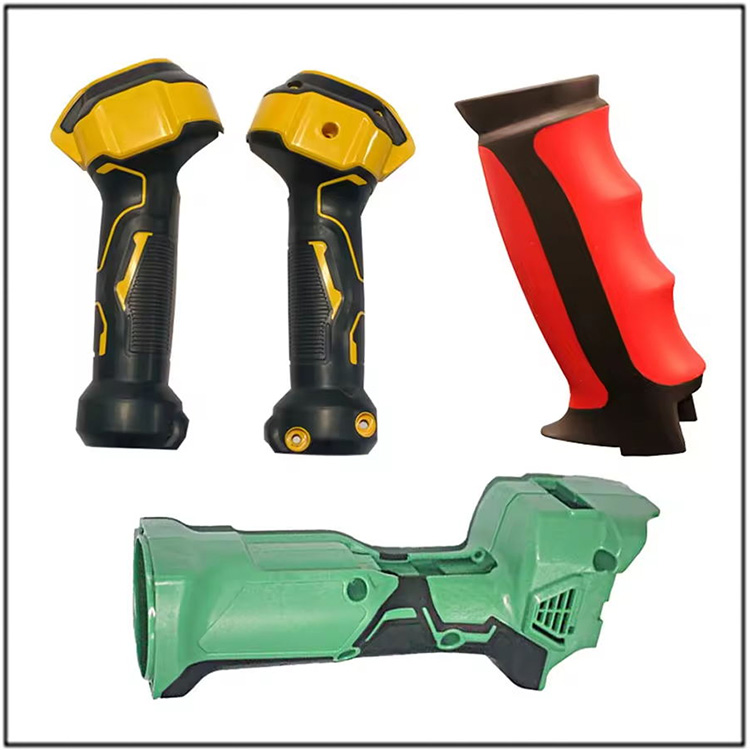
Glass Fiber Reinforced Nylon Injection Molding
Advantages and disadvantages of glass fiber reinforced nylon and solutions to injection molding problems
In modern industry, Glass Fiber Reinforced Nylon (GFN), as a high-performance engineering plastic, is widely used in various fields such as automobiles, electronics, and machinery due to its unique physical and chemical properties. However, this material also faces some challenges during the injection molding process. This article will explore in detail the advantages and disadvantages of glass fiber reinforced nylon, and provide solutions to common problems in the injection molding process to help enterprises improve production efficiency and product quality.
Advantages of Fiberglass Reinforced Nylon
1.Significant enhancement of mechanical properties: After adding fiberglass, the mechanical strength, rigidity, heat resistance, creep resistance, and fatigue resistance of nylon are greatly improved, and the fatigue resistance is 2.5 times higher than before reinforcement.
2.Improved heat resistance and dimensional stability: The addition of fiberglass restricts the mutual movement between plastic polymer chains, significantly reducing the shrinkage rate of the material and significantly improving the dimensional stability of the product, which can maintain excellent performance in high temperature environments.
3.Wear resistance and self-lubricating properties: Fiberglass reinforced nylon has a low friction coefficient, superior wear resistance, and good self-lubricating properties, making it very suitable for applications that require high wear resistance.
4.Good electrical insulation and weather resistance: The material has excellent electrical insulation, is non-toxic, odorless, and has strong weather resistance, and can be used for a long time in various harsh environments.
5.Oil resistance, weak acid resistance, and alkali resistance: Fiberglass reinforced nylon has good resistance to various chemical solvents, expanding its application fields.
shortcoming
5-1.Decreased toughness and increased brittleness: Although the strength increases, the toughness of the material will correspondingly decrease and brittleness will increase. This can be improved by adding toughening agents.
5-2.Deformation and warping during injection molding: Fiberglass will be oriented along the flow direction during injection molding, resulting in increased shrinkage of the product in the orientation direction, which can easily cause deformation and warping. Reasonable mold design and injection molding process can reduce this problem.
5-3.Surface roughness: During the injection molding process, glass fibers may be exposed on the surface of the product, resulting in rough surface and defects such as floating fibers and material patterns.
5-4.Increased wear of injection molding machines: With the increase of glass fiber content, the wear of plasticizing components such as screws of injection molding machines will also increase. It is necessary to use wear-resistant materials or regularly maintain the injection molding machine.
5-5.Reduced fluidity: The addition of fiberglass will decrease the fluidity of nylon and increase the difficulty of injection molding. By optimizing injection molding process parameters, such as increasing mold temperature and reducing measuring chamber temperature, the flowability problem can be improved.
Solutions to Common Problems in Injection Molding Process:
1.Surface defects (such as material patterns, floating fibers)
Solution: Use a twin-screw extruder for granulation, select nylon specific reinforced glass fibers, and add coupling agents or compatibilizers.
2.Dents
Reason: Insufficient filling material, improper gate position, or gate size that is too small.
Solution: Increase the feeding amount, adjust the gate position and size, increase the injection pressure, etc.
3.Silver pattern
Reason: Low injection speed, low mold temperature, etc.
Solution: Increase injection speed, raise mold temperature and barrel temperature, and consider using multi-stage injection technology.
4.Ripples
Reason: Small gate size, unreasonable runner design, etc.
Solution: Modify gate size, optimize runner design, adjust injection pressure and speed, etc.
5.Overflow edge
Reason: Insufficient clamping force, too fast injection speed, etc.
Solution: Increase mold locking force, reduce injection speed, adopt multi-stage injection technology, etc.