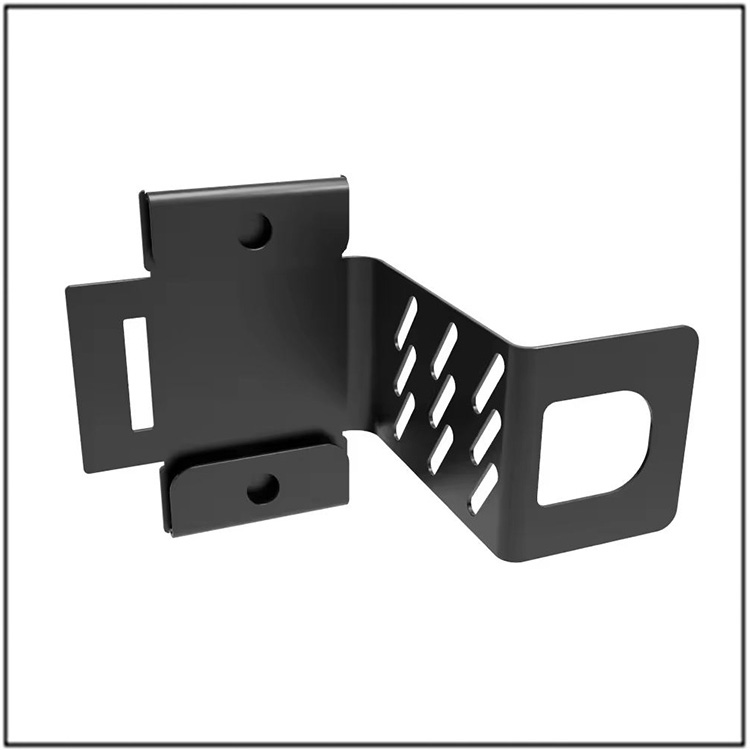
How to Prevent Problems in The Processing of Metal Stamping Parts?
As an important component of modern manufacturing, metal stamping parts are widely used in various industries. However, its processing is often accompanied by a series of challenges, such as burrs, dimensional deviations, surface scratches, and mold damage, which not only affect product quality but may also lead to a decrease in production efficiency. Therefore, it is crucial to take preventive measures to ensure the stability and high quality of the metal stamping process.
The maintenance and upkeep of molds are key to preventing problems in the processing of metal stamping parts. As the foundation of stamping parts, the precision and condition of molds directly affect the quality and processing efficiency of products. Therefore, the mold should be cleaned, lubricated, and inspected regularly to promptly detect and restore worn or damaged parts. At the same time, the blade clearance of the mold needs to be adjusted according to the material thickness and processing requirements to avoid burrs or dimensional deviations caused by excessive or insufficient clearance.
Secondly, selecting appropriate materials and lubricants is equally important. The selection of materials should consider their physical properties and processability, ensuring good plasticity and toughness during the stamping process, and reducing the risk of cracking and deformation. The use of lubricants can reduce friction between molds and materials, and lower the likelihood of surface scratches and mold wear. Choosing the appropriate lubricant also requires consideration of its lubricity, cooling performance, and cleanliness to ensure the stability of the stamping process and product quality.
In addition, strict control of stamping process parameters is also an important means to prevent processing problems. This includes key parameters such as stamping speed, pressure, temperature, etc. The reasonable setting of these parameters can ensure the stability and accuracy of the stamping process. In practical operation, process parameters should be continuously optimized and adjusted based on material characteristics, mold structure, and product requirements to achieve optimal processing results.
At the same time, strengthening employee training and skill improvement is also an important way to prevent problems in the processing of metal stamping parts. Employees should have good operational skills and quality awareness, be able to operate equipment and molds correctly, and promptly detect and handle abnormal situations during the processing. Through training, employees can understand the basic principles and common problems of metal stamping processing, master preventive measures and solutions, and improve production efficiency and product quality.
Establishing a comprehensive quality inspection and monitoring system is also an important guarantee for preventing processing problems. Through comprehensive inspection and monitoring of the processing and product quality, potential problems can be identified and corrected in a timely manner, ensuring that product quality meets customer requirements and industry standards. Meanwhile, the collection and analysis of quality data can also provide strong support for continuous improvement and optimization.
In summary, preventing problems in the processing of metal stamping parts requires starting from multiple aspects such as mold maintenance, material selection, process parameter control, employee training, and quality inspection. By implementing these preventive measures, the stability and high quality of the metal stamping process can be ensured, providing strong support for the development of the enterprise.