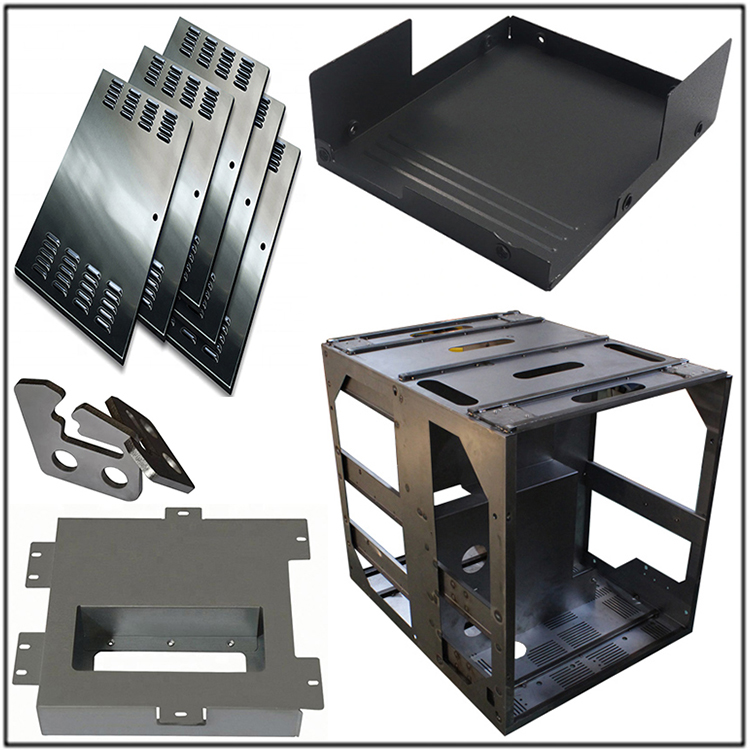
Summary of Welding Knowledge in Sheet Metal Processing
What is welding? Summary of Welding Knowledge in Sheet Metal Processing
Welding is a metal connection process. It is widely used in various fields, including machinery and metal parts, transportation vehicles such as automobiles and ships, as well as construction industries such as steel bars and steel frames. This section focuses on welding in sheet metal processing.
What is welding
Welding is a method of metal connection. The connection structure between the metal components to be connected is completed by heating or applying pressure to melt them, then cooling and solidifying them. The principle is to cause molecular bonding of the metal at the joint through melting and mixing, forming a very strong joint. Welding is a widely used processing method in various fields and is also a part of sheet metal processing technology. It is used to connect parts together or bend adjacent parts together at the same time.
Welding in sheet metal processing is no different from welding in other fields. However, some welding methods (such as friction welding) are not common in sheet metal processing.
Welding usually has the following advantages.
High strength of the joint
Good airtightness at the joint
No other parts are required for connection
No need for large welding machines or equipment
On the other hand, welding usually has the following drawbacks.
Possible thermal deformation and residual stress caused by thermal energy
The connecting part cannot be disassembled
In addition, different welding methods also have their own advantages and disadvantages. Therefore, when welding, it is necessary to understand different processing methods and their characteristics, and choose the most suitable welding method.
Welding types of sheet metal
There are many types of welding, which can be roughly divided into three categories: fusion welding, pressure welding, and brazing. This section will introduce the most commonly used welding types in sheet metal processing.
Melting welding
In fusion welding, the material to be connected (base metal) is also heated and melted, which is closest to the basic concept of welding. In the process of fusion welding, a metal rod called a welding rod is melted and then applied like glue between the materials to be welded, or the base metal is melted and joined together without using a welding rod. The advantages of fusion welding are high welding strength and easy processing of large-sized materials. On the other hand, except for some welding, welding is usually done manually, which may result in differences in welding quality among different operators.
Arc welding
Arc welding is a method of welding that utilizes the heat generated by arc discharge. Connect the base metal potential to the negative electrode and the welding rod (or electrode) to the positive electrode, and use the spark (arc) generated when the welding rod is close to the base metal to melt the base metal for welding. The advantage of arc welding is that it uses a high-temperature arc, which makes it easier to melt the base metal and works faster. In addition, the structure of the welding machine is also very simple. On the other hand, welding personnel need to have the qualification of "arc welder". In addition, since the base material must also be electrified, it cannot be used for non-conductive materials covered with oxide films, etc. The most commonly used arc welding in sheet metal processing are self-protection arc welding and TIG welding. Self shielded arc welding is an arc welding process that uses welding rods covered with a coating containing special components. This coating burns under the action of an arc and isolates oxygen from the air. Although this welding equipment is simple and easy to operate outdoors, its disadvantage is that it is difficult to weld thin sheet materials. The characteristic of TIG welding is the use of materials with extremely high melting points such as tungsten as electrodes. Unlike self-protection arc welding, its electrodes do not melt. Its characteristic is that the voltage is easy to adjust, and it can even weld thin sheet materials.
Laser welding
Laser welding is a method of welding that uses the heat generated by laser irradiation to melt the base material. Compared with other welding heating methods, the intensity of laser is easier to adjust, so even thin plate materials can be easily welded. In addition, the heating area is very small and can be locally heated to very high temperatures, making it easy for precision welding. Due to the low possibility of thermal deformation, the dependence of welding quality on operator skills is also minimal. However, due to the high intensity of the laser used, specialized equipment (room) is required. In addition, this method is not applicable to materials that reflect laser light, such as mirror stainless steel and aluminum. The most commonly used laser welding in sheet metal processing are CO2 laser and YAG laser. Especially YAG lasers have been used for laser welding for a long time.
Gas welding
Gas welding is a method of welding that utilizes the heat generated by the combustion of flammable gases such as acetylene and liquefied petroleum gas. Compared with arc welding, gas welding is easier to adjust the temperature and check the working area during welding, and welding is also relatively easy. In addition, it also has the characteristics of small size and low cost, making it easy to work in any location. On the other hand, compared with arc welding and laser welding, the material heating speed is slower and the working time is longer. In addition, due to the larger heating range, the material is more prone to deformation. There are also many dangers when dealing with gases, so gas welding requires a 'gas welding technician qualification'.
Pressure welding
Pressure welding is a joining method that applies pressure by heating the joint area through friction or electrification. The friction welding mentioned earlier is also a type of pressure welding, but it is basically not used for plates and is usually used for cylindrical materials. The advantage of pressure welding is that pressure and temperature can be controlled mechanically, resulting in stable welding quality. On the other hand, equipment is often larger and can usually only be used for specialized processing.
Spot welding
Clamp the welding area with electrodes and connect it through current. Its characteristic is that it requires welding at individual points, just like using staples to fix multiple positions.
Seam welding
It uses roller shaped electrodes, similar to spot welding, to apply pressure while passing current for welding. Its characteristic is to connect with continuous lines.
Brazing
Brazing is a joining method that uses a metal material "brazing" with a melting point lower than the base metal as an adhesive. Unlike other welding methods, it does not require heating of the base material. The advantage of this method is that it will not damage the base material, the base material is not easily deformed, and it is suitable for welding different materials. But the welding strength is slightly inferior to other welding methods.
Hard brazing
Hard brazing is a brazing method that uses brazing filler metals with a melting point above 450 ℃. When using brazing materials with a melting point below 450 ℃, it is called soft soldering. Compared with soft soldering, hard soldering has higher strength. In addition, gas burners are used for brazing, while soldering irons are used for soldering.
Robot welding
Some welding can be done not only manually, but also by robots. Spot welding and seam welding were initially mainly completed by robots, while arc welding and laser welding are usually done manually, especially in recent years, the application scenarios of robot automatic welding have gradually increased. Especially in the field of arc welding, more and more robots are being used for teaching, such as welding through manual guidance or automatic recognition of welding range through images.
Welding symbols and graphic methods for welding
The following is the basic form of representing welding symbols in 2D drawings.
Welding characteristics of different materials
The precautions for welding different metal materials are also different. Here we mainly introduce the welding characteristics of iron, stainless steel, and aluminum.
Steel
When welding steel materials, attention must be paid to the influence of compounds mixed with iron. Especially pay attention to carbon. Steel with high carbon content will undergo rapid temperature changes during welding, leading to changes in its internal crystal structure and resulting in cracking and decreased toughness. Therefore, it is recommended to choose low-carbon steel as much as possible when welding steel materials. SS material (rolled steel for general structural use) is a material that is more suitable for welding among steel materials. In addition, SM material (rolled steel used for welding structures) is a material specifically manufactured for welding, making it easy to weld. TIG welding and self-protection arc welding are more suitable for welding steel.
Stainless steel
Generally speaking, stainless steel is considered a material that is difficult to weld. This is because the composition of different types of stainless steel varies greatly, and their welding performance is also very different. Stainless steels suitable for welding include SUS304 and SUS316, which are classified as austenitic systems. However, ferrite SUS430 and martensitic SUS410 are not very suitable for welding.
Aluminium
Aluminum is a representative of difficult to weld materials. As a metal, aluminum does not have a high melting point. However, when it combines with oxygen in the air, it forms a high melting point oxide film. Therefore, if an attempt is made to melt the thin oxide layer on the surface, the aluminum inside may melt first, causing the entire substrate to melt. In addition, aluminum has a high thermal conductivity, which means that heat will spread throughout the entire component during welding. This makes it difficult to raise the temperature of the welding point and also makes the components more prone to deformation. When welding aluminum materials, it is necessary to efficiently and quickly heat the welding area and weld quickly. TIG welding is suitable for welding aluminum materials.
Precautions for welding in design
When specifying welding methods during the design phase, please pay attention to the following points.
Avoid interference between other parts and welds
Usually, welding will result in protrusions. Although the height of the raised part can be specified or the raised part can be removed, especially for manual welding, the amount of raised part in the welding area is uneven. Therefore, it is best to avoid contact between another component and the weld seam as much as possible during design. Therefore, it is best to avoid close contact between another component and the weld seam when designing the weld seam. Some measures can be taken to avoid it, such as setting process holes (escape holes) on the parts.
Pay attention to welding stress
When welding a pipe or cylinder into a hole, the end of the pipe or cylinder cannot be directly inserted into the bottom of the hole. This is to prevent the pipe fittings or cylinders from expanding due to heat during the welding process, thereby generating stress at the welding site.
Avoid overlapping solder wires
If the welding lines overlap or the welds on the front and back of the components overlap, the thermal effect of welding can easily accumulate and cause deformation. So it is recommended to avoid overlapping welding lines and seams.
Summary
Welding is a method of connecting metals by applying heat or pressure to metal components to melt them, and then cooling them to a solid state, thereby connecting them together. Due to molecular bonding of the metal at the junction, a very strong bond is formed. There are three types of welding: fusion welding, pressure welding, and brazing. The most commonly used welding types in sheet metal processing are arc welding, laser welding, and gas welding. Pressure welding usually uses spot welding and seam welding, while brazing usually uses hard welding. JIS Z 3021 specifies the drawing symbols for welding. Attention should be paid to the carbon content when welding steel. The stainless steel suitable for welding is the austenitic series, such as SUS304 and SUS316. Aluminum is not very suitable for welding.