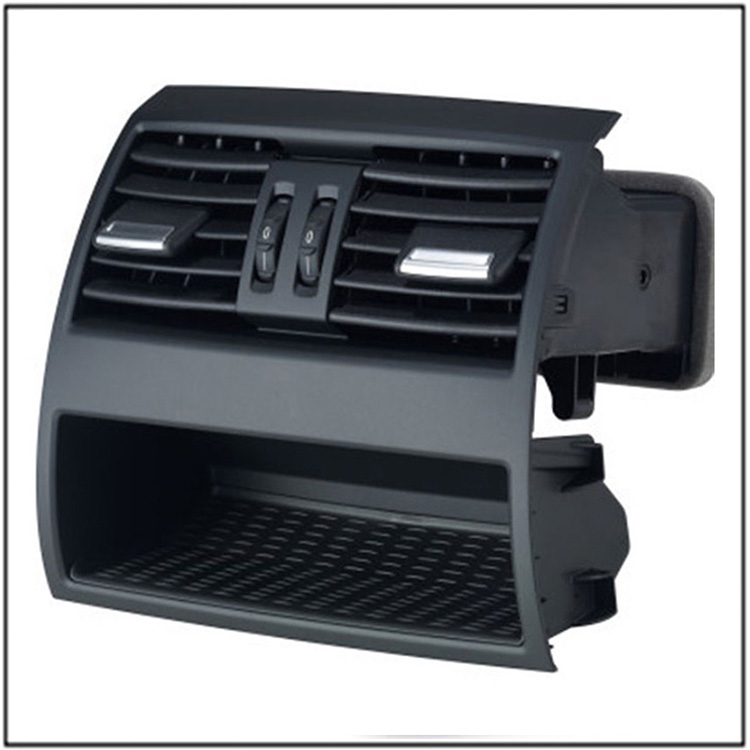
How to Determine The Position of The Injection Mold Parting Line?
The Injection Mold Parting Line, also known as the parting surface, is the contact surface between the upper and lower parts of the plastic mold, and is the boundary that separates the plastic mold during the injection molding process. The reasonable design of the parting line directly affects the demolding effect, surface quality, and ease of maintenance during injection molding. Therefore, selecting the appropriate parting line position is crucial for optimizing mold design.
The principles for determining the position of the parting line include the following aspects:
-The appearance characteristics of the product: The parting line should usually be set along the geometric features of the product's appearance, avoiding setting parting lines in prominent parts of the product to reduce visual defects. For example, avoid setting parting lines in the middle or difficult to repair parts of the product, especially for components with high appearance requirements.
-The opening and closing direction of the mold: The parting line should be as parallel as possible to the opening and closing direction of the mold. This can avoid the situation of mismatched parting lines and ensure smooth opening and closing of the mold.
-Easy demolding: When designing the mold, the position of the parting line should be conducive to the smooth demolding of the product. Avoid dead corners, dents, or nested areas that may cause difficulty in demolding and affect production efficiency.
-Strengthening product structure: The setting of parting lines should also consider the structural strength of the product. Avoid setting it in thin-walled parts to prevent uneven product strength or stress concentration caused by the presence of parting lines.
-Avoid high processing difficulty: Try to avoid selecting parts with high processing difficulty and complex processing techniques as the parting line positions. For example, selecting parts with large curvature or small holes not only increases processing difficulty, but may also affect the accuracy of the mold.
In the specific mold design process, determining the position of the parting line requires consideration of the following factors:
1.1. Appearance and functional requirements of the product
When determining the position of the parting line, the first consideration should be the appearance and functional requirements of the product. If the appearance of the product is very important, it is best to choose the parting line in inconspicuous areas, such as the back or hidden areas of the product. At the same time, during design, it is advisable to avoid setting parting lines on smooth surfaces or areas with complex curved surfaces to avoid affecting the appearance of the product.
1.2. Types and shapes of molds
Different types of molds have different requirements for the parting line. For injection molding molds, the parting line is usually located in the direction of the mold opening; For die-casting molds, the parting line may need to be set according to the shape of the product and the needs of the die-casting process. In any case, it is necessary to ensure that the design of the parting line can effectively match the working principle of the mold and reduce interference during processing.
1.3. Consideration of Production Efficiency
Production efficiency is an important factor that enterprises cannot ignore when designing molds. Reasonably setting the position of the parting line can effectively reduce the resistance and friction during the injection molding process, and improve production efficiency. Avoiding complex parting line design can reduce the time for secondary processing and correction, thereby improving the service life of the mold.
2. Common problems and solutions in parting line design
2.1. The parting line affects the appearance of the product
Sometimes, designers fail to fully consider appearance issues when selecting parting lines, resulting in obvious parting line marks on the surface of the mold product. To solve this problem, designers can choose to use more refined finishing techniques or adjust the position of the parting line to avoid placing it in a more prominent position.
2.2. Difficulty in demolding caused by the position of the parting line
In some cases, unreasonable mold design can lead to difficulties in demolding, especially in complex products. To avoid this problem, auxiliary devices such as inclined surfaces and sliders can be installed near the parting line to assist in demolding and reduce the difficulty of demolding caused by the parting line.
By scientifically and reasonably designing the parting line, the production efficiency, service life, and product quality of injection molds can be effectively improved. Therefore, in every stage of injection mold design, the setting of parting lines cannot be ignored.