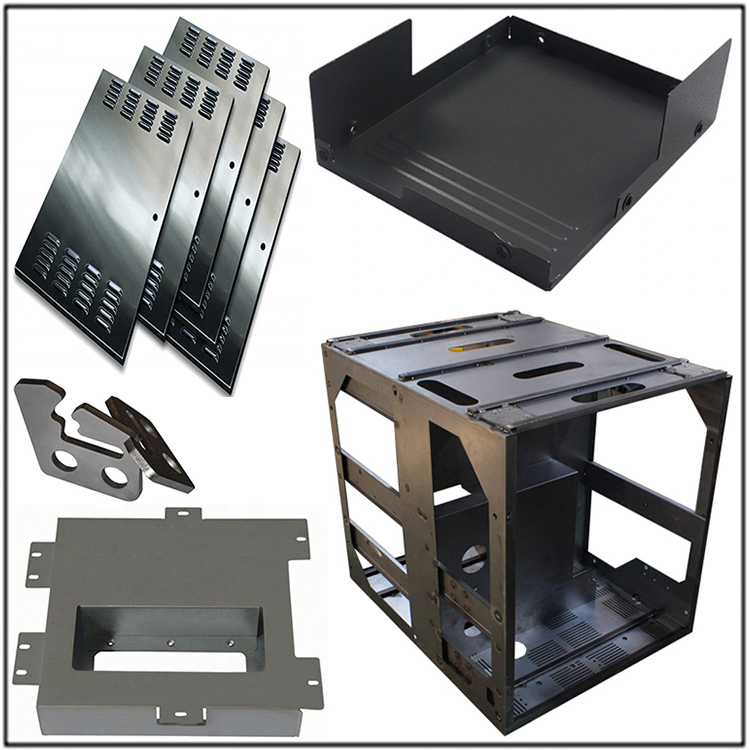
Basic Knowledge of Sheet Metal Processing
Basic knowledge of sheet metal processing - its advantages and disadvantages, and methods to reduce costs
Sheet metal processing is a machining technique that applies force to thin sheet metal to deform it, resulting in a three-dimensional shape. The processing methods of sheet metal can be roughly divided into two types: manual sheet metal and mechanical sheet metal. Manual sheet metal is formed by manually applying force to the metal plate using tools such as hammers, while mechanical sheet metal is formed by clamping the material in a mold and applying hydraulic or other mechanical forces. In this section, we will focus on introducing the basic knowledge of sheet metal processing that designers need to understand. Mechanical sheet metal is a commonly used processing method in industrial products, known as "sheet metal processing"; Parts made through sheet metal processing are called "sheet metal parts".
Key points of sheet metal processing
In sheet metal processing, it is necessary to apply force to the plate-shaped metal material through various methods to create the desired shape, and the principle is related to the characteristics of the metal material. When a load is applied to a metal material, the distance between its constituent atoms changes, resulting in deformation while generating strain. If the load is small, the metal will return to its original state (elastic deformation) after removing the load. If a load is continuously applied to the metal and exceeds a certain point (yield point), the metal will not be able to recover to its original state (plastic deformation). If a larger load continues to be applied, it will break due to inability to withstand it. In the process of sheet metal processing, it is important to master the processing techniques and adjust the metal state in real time in order to obtain the desired shape through plastic deformation.
Sheet metal processing process
From sheet metal processing to shipment, there are approximately 8 processes that need to be completed. Let's take a closer look at each process below.
1.Expand and Program
Design drawings are usually created using 3D CAD, but sheet metal processing always starts from a single sheet metal, so CAD or professional software must be used to "unfold" the 3D shape into a single sheet metal before processing. After the drawing is completed, it is necessary to carry out "nesting" to arrange the parts, so that the parts can be efficiently and waste free arranged from fixed specifications of materials, and at the same time, a machining program can be developed.
2.Punching and cutting
In the process of cutting the outer and inner holes of metal sheets (also known as blanks), two main types of processing equipment are used: laser cutting machines and turret punch presses. The characteristic of laser cutting machine tool is its ability to quickly cut the outer periphery and large holes, while turret punch can correspond to a large number of hole processing and forming processing. In addition, there is a "laser punch press composite machine" that can simultaneously achieve these two advantages. Due to the different equipment owned by different sheet metal factories, it is recommended to allocate processing tasks based on the contractor's equipment when placing an order.
3.Deburring
No matter which processing method is used in the previous process, burrs will be generated to a certain extent. For example, laser cutting process will produce burrs, and turret punch cutting will also produce burrs and burrs. These all need to be removed during the deburring process. It can be done manually with a grinder or file, or by a deburring machine that rotates sandpaper. In the deburring process of sheet metal processing, it is difficult to control fine dimensions such as C0.2 or R0.2 like in cutting processing. The drawing indication of 'no burrs' may be ambiguous, but it is considered effective when the customer wishes to remove burrs to a degree that does not cut their hands. It is recommended to reach a consensus with the client regarding the allowable range of deburring when placing an order.
4.Bending
The common bending method in mechanical sheet metal is to install the mold on a machine called a bending machine, and then apply pressure to the cut sheet metal to bend it in a straight line at a fixed angle. Install a punch on the upper part of the pressure bending machine and a fixed die on the lower part. Bend the metal sheet by moving the punch on the upper part of the machine up and down. However, due to different material batches and rolling directions, there are also differences in the angle after bending, which requires fine-tuning every time, making it a difficult processing technique. However, the accuracy of the bending process greatly affects the difficulty and aesthetics of subsequent welding processes, making it one of the most important processes in sheet metal processing. In addition, "pressure bending machine" is sometimes referred to as "bending machine", "bending machine", etc., all of which refer to the same type of machine.
5.Welding
Welding is the process of connecting metals by heating them to melt and then cooling them. TIG welding and laser welding are the most commonly used welding methods in sheet metal processing. TIG welding using tungsten electrodes is sometimes referred to as "argon welding" because it uses argon gas as a shielding gas. TIG welding can use welding rods to fill the melting area, but it also requires a large amount of heat input to the material, which can easily cause thermal deformation. The processing effect largely depends on the worker's technical proficiency. Laser welding is a processing method that can suppress thermal deformation and has the advantage of easy standardization of processing technology. However, because it is based on base metal welding, it is difficult to use this method for parts with welding requirements, and the processing technology needs to be changed.
6.Precision machining
The precision machining process in sheet metal processing includes eliminating thermal deformation caused by welding, grinding off protrusions in the weld seam, electrolytic grinding to remove weld burns, and surface grinding treatment (polishing, buffing).
7.Assembly
This process involves combining multiple parts together and assembling them using fasteners (mainly bolts, nuts, rivets, etc.). Mostly used for parts that do not require welding strength or require disassembly operations in the future. Assembly work, also known as "assembly", covers a wide range of operations and processes, from assembling small components to assembling medium-sized components, and finally assembling the entire machine and equipment. In addition, in the sheet metal processing industry, some companies refer to the above welding assembly process as "assembly" (welding assembly).
8.Inspection
In the inspection of sheet metal processed products before leaving the factory, visual inspection is generally used for size and appearance checks. Dimensional inspection mainly uses vernier calipers, scales, angle gauges, etc. Compare the finished product with the drawing and check for any errors in dimensions, hole positions, and accuracy. Visual inspection is required to check whether the product has defects and burrs. Some factories may use image measuring instruments and coordinate measuring instruments for inspection.
Types of machine tools used for sheet metal processing
As mentioned above, different machines and equipment are used in each process of sheet metal processing. Here are the main machines used in sheet metal processing.
Laser cutting machine
Laser cutting machine uses high-power laser to irradiate metal materials, causing them to melt locally, and then blows off the melted metal with gas for cutting. It is skilled at high-speed cutting of longer perimeter and long holes. On the other hand, when there are a large number of holes on the board, the number of processing holes (through holes) increases and the processing time is longer. But in recent years, with the increasing efficiency of laser cutting machines, high-speed machining of through holes has become possible. But it cannot perform molding processes such as threaded holes and flanged holes.
Rotary tower punch press
Turrepun, also known as a turret punch press, is a machining machine that installs many small molds on a mold support called a turret, and then high-speed punches and cuts metal sheets. Suitable for high-speed machining of porous parts, and capable of forming processes such as tapping, flanging, countersunking, blinds, etc. On the other hand, punching the shape of the outer periphery and waist shaped holes requires many stamping processes to complete, resulting in a longer processing time.
Laser punch press composite machine
This multifunctional device is equipped with both types of processing equipment mentioned above. It can complete punching and forming in one process, using laser processing for time-consuming peripheral and long holes, and using brick tower punching machines for hole and forming processing. Due to the fact that there is no need to replace equipment according to the process, it has the advantage of not causing deviation in the machining position due to multiple clamping of the workpiece.
Deburring machine
Traditionally, deburring in sheet metal factories is done through manual polishing machines and files. But in recent years, more and more factories have introduced deburring machines. On the deburring equipment, the workpiece is adsorbed onto the conveyor belt and a brush with sandpaper is rotated to uniformly remove burrs.
Pressure bending machine
In a pressure bending machine, the convex die (punch) is connected to the upper part of the equipment, and the concave die (fixed die) is installed at the lower part. The upper part of the equipment is moved to apply downward pressure to bend the metal sheet. According to the different pressurization methods, it can be divided into mechanical, hydraulic, servo motor+ball screw, etc., but currently the commonly used models are those that can adjust the pressure size through a numerical control system. In recent years, models with adjustable rules (collision) that can be automatically moved according to the program have also become popular, which helps to improve bending accuracy. The materials, thickness, and length that can be processed depend on the maximum pressure (tonnage) and the range of machinable lengths.
Laser welding machine
Laser welding is a welding method that is not prone to thermal deformation, as it penetrates through thin and deep layers with a small heat affected layer. Among laser welding methods, the "YAG laser welding machine" was the first to become popular and is known as a welding method that can minimize deformation and maintain aesthetics. The "fiber laser welding machine" that emerged around 2015 solved the problem of insufficient strength in YAG laser welding and quickly became popular as a welding method that can weld with low deformation and high strength. The biggest advantage of laser welding is that even thin plates are not easily deformed, so even unskilled workers can perform processing and ultra-thin plate processing that only skilled technicians can use argon arc welding. If thin plate structures are adopted in the future with the lightweighting of equipment, laser welding is expected to be promoted as a more common process.
TIG welding machine
TIG welding (argon arc welding) is a type of electric arc welding that uses electricity and is currently the most commonly used welding method for mechanical sheet metal. Usually argon is used as an inert gas, so it is sometimes referred to as "argon welding". TIG welding is a process of melting and joining metals by applying high voltage to electrodes, thus it has the characteristics of good sealing and water tightness, and high welding strength. On the other hand, high heat input to the metal can create a large heat affected zone around the molten pool, leading to severe deformation of the product. The machining techniques of minimizing thermal deformation and eliminating strain during welding are both very difficult, so TIG welding is also known as the "craftsman process".
Materials and surface treatment for sheet metal processing
The materials used for sheet metal processing include stainless steel, steel (SPCC, SECC), and aluminum. Depending on the material, the thickness range of the board is between t0.1 and 22mm. When choosing, it is recommended to consider the actual application and processing characteristics of the product.
Regarding the materials and surface treatments used in sheet metal processing, please refer to the following article.
Detailed introduction by experts on the use, materials, processing procedures, etc. of sheet metal parts!
Advantages and disadvantages of sheet metal processing
The biggest advantage of sheet metal processing is that it is suitable for small batch and multi variety production. Stamping is a typical plastic processing method that is suitable for mass production of parts with the same shape, but requires the manufacture of specialized molds for each product. Unless produced in large quantities, it will increase the manufacturing cost of the product. In contrast, sheet metal processing uses universal equipment in all processes such as punching, bending, and welding, and also uses universal molds for bending. This allows for small-scale production of various products and flexible response to design changes. Another major advantage is that by combining "punching", "bending", and "welding", complex shaped products can be manufactured from a single piece of material. On the contrary, its disadvantage is that since the parts need to be processed one by one, if a large number of identical parts are made, production will require a lot of time. Especially in welding, it still relies heavily on manual skills and not everyone can process it, so it is not suitable for large-scale production.
Methods to reduce the cost of sheet metal processing
Here are four key points to reduce costs in sheet metal processing.
Order based on the expertise of the processing manufacturer
Although they can all be called "sheet metal processing manufacturers", the equipment of different companies is also not the same. By placing orders based on the characteristics of the processing equipment, costs can be reduced. For example, as mentioned earlier, laser cutting machines are good at high-speed processing of full circumference and long holes, while turret punch presses are good at processing and shaping a large number of hole shapes. If manufacturers who mainly use laser cutting machines for rough processing order products that focus on drilling and forming, the processing cost will increase; If we order the peripheral cutting of large-sized products from manufacturers who mainly use turret punch presses, the processing cost will increase. Therefore, simply understanding the manufacturer's areas of expertise to place an order is likely to reduce costs.
Reduce welding and use bending structures where they can be bent
As mentioned in the "TIG welding" section, the welding process of small batches and multiple varieties largely relies on the skilled skills of workers, which often increases the unit cost of the process. For example, if two boards need to be aligned at a 90 ° angle and can be bent, the bending structure often reduces the processing cost. It is recommended to choose based on the characteristics of the bending process, such as interference with materials or molds. In addition to bending, riveting can also reduce costs, but all components in the drawing must have no welding instructions.
Revisit the instructions for deburring
Although the requirement of "no burrs around the entire circumference" is clearly marked in the drawings, the processing manufacturer also spends a lot of equipment and labor costs on deburring. By limiting deburring instructions to truly necessary components, the cost of deburring processing in factories can be reduced. In addition, instead of blindly demanding high precision, it is better to find ways to reduce costs by discussing the actual precision level that the processing party can achieve and the acceptable deburring quality level of the ordering party.
Reconsider whether welding is necessary
When welding at a certain angle, it is usually required to weld overlay to ensure welding strength, but laser welding can easily achieve low deformation welding of thin plates, but it is not good at weld overlay. In recent years, methods such as fiber laser welding have become popular, and even base material welding can ensure sufficient strength. Therefore, considering changing the welding method instead of insisting on using overlay welding to ensure strength may also be a feasible cost saving measure.
Summary
Sheet metal processing is a process technology that can flexibly correspond to small batch and multi variety processing, but still requires workers' intuition in many aspects, so it is still a difficult processing field. In addition, due to different choices of processing equipment and methods, manufacturing costs also vary. Therefore, it is recommended that everyone fully understand the characteristics of sheet metal processing and choose reasonable processing equipment and methods for effective design.