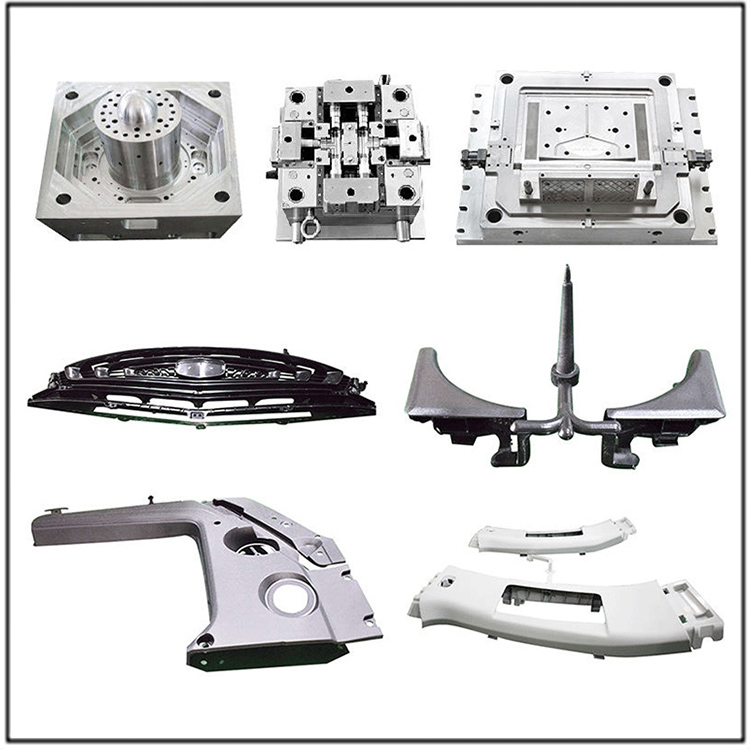
How to Set the Mold Temperature in Injection Molding?
In the precision process of injection molding, the setting and control of mold temperature is like the delicate strokes of carving art, directly determining the quality and performance of the final product. Reasonable and accurate mold temperature can not only optimize the flowability and crystallization process of plastic materials, but also significantly improve the dimensional accuracy, surface smoothness, and physical properties of products. This article will delve into optimization strategies for mold temperature settings in injection molding, helping enterprises achieve efficient production and quality improvement.
1.Accurately match material characteristics
For example, for thermoplastic materials such as ABS, the mold temperature is usually between 20 ° C and 80 ° C, while high-temperature resistant nylon materials may require higher mold temperatures to ensure sufficient crystallization. Therefore, when setting the mold temperature, the primary task is to have a deep understanding and accurately match the optimal processing temperature range of the plastic material used.
2.Product performance requirement orientation
For products that require high strength and good dimensional stability, higher mold temperatures help reduce shrinkage and internal stress; For products that require a high gloss surface, it is necessary to ensure that the mold temperature is uniform and moderate to avoid surface defects.
3.Collaborative injection molding process parameters
The setting of mold temperature also needs to be closely coordinated with other parameters of the injection molding process, such as melt temperature, injection speed, holding time, etc. These parameters interact with each other and together determine the flow and solidification behavior of plastic materials in the mold.
Optimization strategy for mold temperature control
1.Adopt advanced mold temperature machine
Modern mold temperature control machines are usually equipped with intelligent temperature control systems that can monitor and adjust the mold temperature in real time, ensuring that it fluctuates within a preset range. In addition, some high-end mold temperature machines also have dual functions of preheating and cooling, which can significantly shorten production preparation time and improve production efficiency.
2.Implement precise temperature control layout
By setting up reasonable cooling channels and heating elements inside the mold, the temperature of each part of the mold can be ensured to be uniform and consistent, avoiding product quality problems caused by local overheating or undercooling. At the same time, by adopting zone temperature control technology, different temperature zones can be set according to the needs of different parts of the product, further improving the uniformity of product quality.
3.Continuous monitoring and adjustment
By installing temperature sensors and data acquisition systems, real-time mold temperature data can be obtained and compared with preset values for analysis. Once significant temperature deviation or abnormal fluctuations are detected, immediate measures should be taken to adjust and ensure that the mold temperature remains within the optimal range.