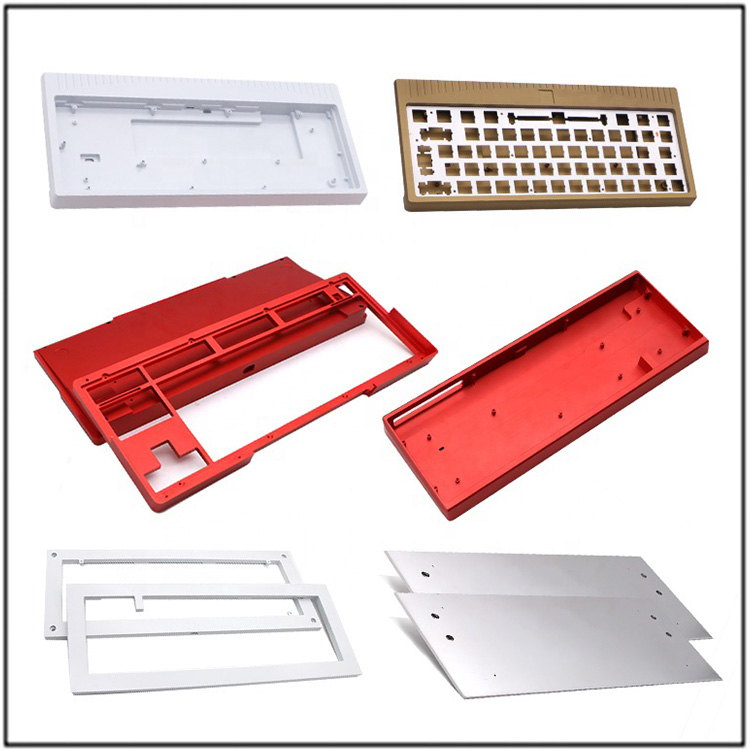
Characteristics and Processes of Machining Center Machining
Machining center is a process of automatically processing materials according to a program, and the machine tool that can perform this type of processing is called a machining center machine tool.
This section will introduce the characteristics and processes of using machining center machines for mechanical processing.
What is machining center machining?
Machining on a machining center is a type of cutting process performed using a machining center. The position of the cutting tool is automatically controlled based on the input program and the shape of the 3D graphics. In addition, the cutting tools can be automatically replaced, so there is no need to use different equipment or change the tools every time processing, and the processing speed of complex shapes is also faster. The advantage of doing this is that previously required a large amount of equipment for processing, but now only fewer equipment are needed to complete it, and complex shapes that are difficult to process with traditional equipment can also be processed.
Characteristics of machine tools used in machining center machining
During the machining process using a machining center, the cutting tool rotates at high speed to cut the material into the desired shape. It can be regarded as a type of milling machining. Its main feature is that it can perform automatic machining by setting the machining program (NC program), and can automatically replace multiple cutting tools. It can automatically switch to a tool that corresponds to the desired material and conditions according to a pre-set program, for cutting surfaces, slotting, drilling, etc. The equipment used for milling processing includes not only machining center machines, but also general-purpose milling machines and CNC milling machines. If they are compared with the machining of machining center machines, universal milling machines do not have automatic tool changing function and cannot perform automatic machining according to the set program; CNC milling machines can perform automatic machining, but cannot automatically change tools.
Types of machining center machine tools
The machining center machines used in machining can be divided into the following four types.
Vertical machining center
Horizontal machining center
Longmen machining center
Five axis machining center
Below are the characteristics of vertical, horizontal, gantry, and five axis machining center machine tools.
Vertical machining center
The cutting tools of the vertical machining center are perpendicular to the direction of the equipment's ground plane, processing materials from top to bottom. The rotation axis of the tool installation can move in the longitudinal, transverse, and height directions, so the machining process can be observed from above. Compared to horizontal machine tools, this type of machine tool has a more compact structure and can be deployed in a smaller space. Although this type of machine tool is widely used, the chips generated during the machining process are difficult to discharge, making it more prone to malfunctions caused by chips. Compared to mass production, it is more suitable for multi variety and small batch production.
Horizontal machining center
The tool of the horizontal machining center is installed horizontally, processing materials from the side in a direction parallel to the equipment ground plane. The chips generated during the machining process fall downwards, so compared to vertical machining centers, chip related problems are less likely to occur. Depending on the equipment, automatic transmission devices for parts can also be added. This allows for continuous processing of materials, suitable for mass production of the same product.
Longmen machining center
Like vertical machining centers, the cutting tools of gantry machining centers are also installed perpendicular to the equipment ground plane. However, the cutting tool shaft of a vertical machining center is cantilevered, while a gantry machining center is supported from both sides by two pillars that span the workpiece in a "gantry style". The characteristic of this machining center is that it can process large workpieces over a few meters long, but the machining center itself is also very large.
Five axis machining center (five axis linkage machine tool)
The five axis machining center (five axis linkage machine tool) is the latest equipment in the field of cutting technology, which is a machining center that adds two rotary axes in addition to the vertical axis, horizontal axis, and height axis. The machining operation that requires manual rotation and repositioning of materials by the operator on a vertical or horizontal machining center can be automatically completed on a five axis machining center without the need for manual intervention by the operator. In addition, the equipment does not need to be shut down for setting changes, so it can be continuously processed. Although most machine tools are vertical, some gantry machining centers can also rotate the machine head to achieve five axis machining and are used for manufacturing aircraft components. Improved processing efficiency and reduced setting errors, resulting in improved quality. On the other hand, its disadvantages include the high cost of the machine tool itself, resulting in relatively high processing fees, and heavy cutting is not its strong point. It is rare to complete all processes on one machine tool. In addition, the difficulty of developing machining programs, including rotation, is also a barrier to introducing this equipment.
Please refer to the following text for detailed differences between three-axis machining centers and five axis machining centers.
What is a good method for machining shaft type workpieces? Introduce the differences between 3-axis machining centers and 5-axis machining centers.
The process of machining on a machining center
When using a machining center for machining, the following steps need to be taken.
1.Writing and reading of processing programs
In order to process materials as expected, a program needs to be written to instruct the machining center on how to operate. The program is written based on product drawings and 3D data, which not only includes shape, but also cutting direction, cutting path, tool movement speed, etc.
After the program is written, load it onto the machining center.
2.Setting of workpiece materials and cutting tools (positioning and assembly)
Set the materials to be processed and the tools to be used on the machining center. At this point, if the position of the material and tool is incorrect, it will not be possible to process with the expected accuracy, so reliable calibration must be performed.
3.Material processing (program execution)
After preparation, start processing the materials. The processing is carried out according to the set program, but it is necessary to check whether the material is processed as expected. The cutting sequence is rough machining first, cutting out the rough shape; Then precision machining is carried out to produce the required size and shape. After processing, check if the shape and accuracy meet expectations.
Representative materials that can be processed by machining centers
During the machining process using machining center machines, commonly used materials include metals such as iron, copper, aluminum, and their alloys. The material generates a large amount of chips during the cutting process, making it unsuitable for processing expensive materials such as gold and silver. In addition, if the type of cutting tool and processing conditions permit, brittle materials such as glass, resin, and ceramics can also be processed.
Precautions for machining on machining centers
When using machining center machines for machining, the machining process must be considered in the design stage. There will be significant differences in quality, production time, and cost depending on the processing sequence and the angle relationship of chamfers in the finished product shape. Specifically, the cutting depth should be as shallow as possible and can be machined from both sides. If deeper shapes need to be processed, the accuracy may deteriorate due to unstable cutting tools. In addition, if the side of the hole to be processed is in a linear state, the bottom of the hole needs to have an R shape, and it is difficult to process holes with both the side and bottom surfaces in a linear shape.
Summary
Machining on a machining center refers to a machining method performed using a machining center machine tool. By using a machining center machine tool for machining, it is possible to automatically replace cutting tools during the machining process through program settings, thereby producing high-quality products in a short period of time. It is very important to consider the processing flow and sequence from the design stage when using machining centers for machining.