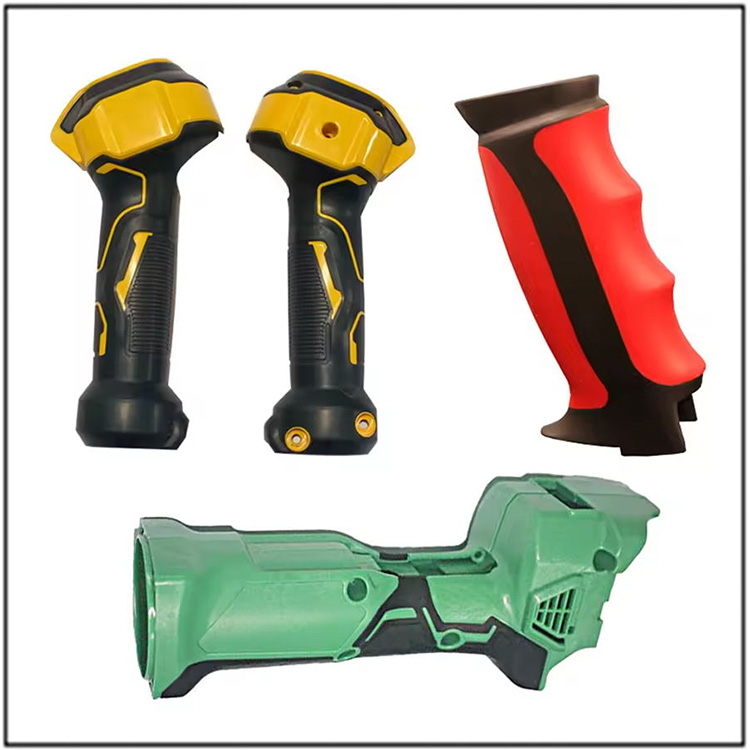
Why is TPE Overed ABS to Breakage and Peeling During Injection Molding?
In injection molding, the reason why TPE overed ABS is prone to gate breakage and peeling can be attributed to multiple factors, including material characteristics, mold design, process parameters, and operating procedures. The following is a specific analysis of these reasons:
1.Material characteristics
Compatibility issue: The compatibility between TPE and ABS may not be ideal, resulting in weak bonding between the two materials during injection molding, which can easily lead to delamination or peeling. In addition, the hardness, elasticity, and other characteristics of TPE materials can also affect their bonding effect with ABS.
Material strength: If the strength of TPE material is insufficient, or if the material performance decreases due to improper storage (such as moisture content, aging degradation, etc.), it is easy to cause fracture or peeling problems during the injection molding process.
Gate design: If the gate size is too small or the position is improper, it will cause excessive shear force when the melt passes through the gate, resulting in peeling or fracture. In addition, the design of mold flow channels should also minimize edges and stress concentration points to avoid easy breakage of the nozzle.
Mold temperature: Mold temperature has a significant impact on the cooling and curing process of TPE materials. If the mold temperature is too high or the cooling time is insufficient, TPE material may be pulled out of the gate before its strength is fully formed, which can easily lead to fracture.
3.Process parameters
Injection speed and pressure: Excessive injection speed and pressure can cause significant tensile stress in the melt during the flow process, increasing the risk of fracture. Meanwhile, excessively high shear rates may also lead to peeling or delamination of TPE materials.
Injection molding temperature: Excessive injection molding temperature can degrade TPE materials, reduce toughness, and increase the possibility of fracture. If the temperature is too low, it will affect the fluidity of the material, leading to insufficient filling or a decrease in surface quality.
4.Operation process
Drying treatment: If TPE materials are not sufficiently dried before injection molding to remove moisture and volatile substances from the material, problems such as bubbles, peeling, or breakage are prone to occur during the injection molding process.
Shutdown time: When restarting the injection molding machine after a long shutdown, the molten material may age and degrade due to prolonged residence time in the barrel, leading to a decrease in the quality of subsequent injection molded products.