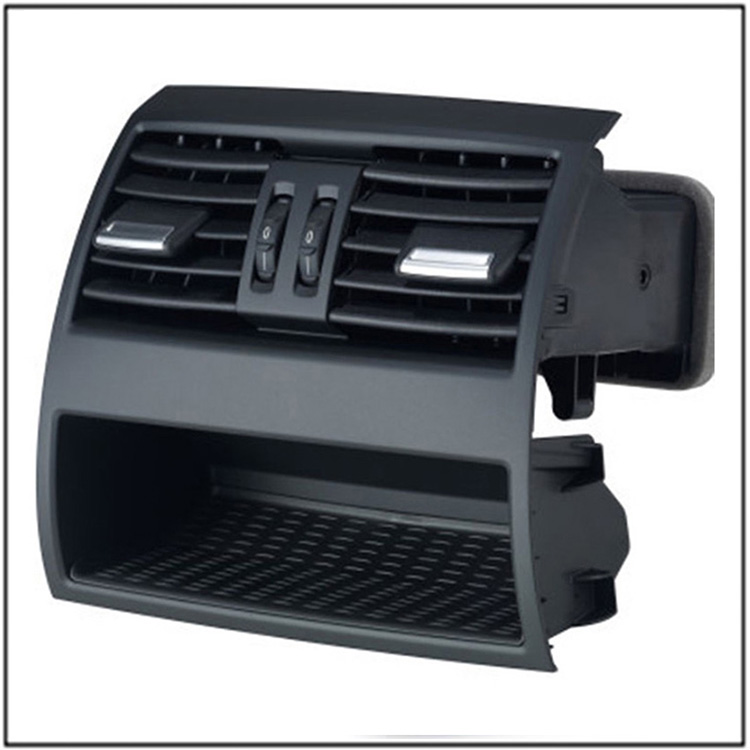
How to Distinguish Between Compression Molding and Injection Molding
Compression molding and injection molding: Both have their own characteristics in plastic processing. Compression molding focuses on high precision and small batch production, and is formed through compression curing; Injection molding is skilled in large-scale, automated production, and high-pressure injection of molten plastic into molds. The two principles are different, each with its own advantages and disadvantages, and are applicable to different fields and needs. The following is a detailed distinction between these two molding methods:
1.Forming principle and process
1-1.Compression molding
Principle: Compression molding (also known as compression molding or compression molding) is the process of first placing powdered, granular, or fibrous plastic into a mold cavity at a molding temperature, then closing the mold and applying pressure to shape and solidify it.
Process: Put melted plastic or molded material into a mold, and under certain temperature and pressure, the plastic will be compressed into the desired shape of the product. The compression molding process utilizes the characteristics of each stage of resin curing reaction to achieve product molding, that is, the molding material is plasticized, flows, and filled into the mold cavity, and the resin is cured.
Principle: Injection molding is the process of using high pressure to inject melted plastic into a mold to form a product.
Process: The molten plastic is heated to a certain temperature in the injection machine and pushed into the mold through pressure. In the mold, the melted plastic will cool and solidify into the desired shape of the product. Mold companies for injection molding products usually consist of two parts, the upper mold and the lower mold.
2.Comparison of advantages and disadvantages
2-1: Compression molding
advantage:
A: Good product quality, high surface finish, suitable for small batch production.
B: The product has low internal stress, minimal distortion, and stable mechanical properties.
C: The wear of the mold cavity is small, and the maintenance cost of the mold is low.
D: It can form larger flat products with high production efficiency, making it easy to achieve specialized and automated production.
Disadvantages:
A: Mold manufacturing is complex, requires significant investment, and has relatively high costs, making it unsuitable for large-scale production.
B: The molding cycle in the production process is relatively long and the efficiency is relatively low.
C:Not suitable for molding complex products with dents, side slopes, or small holes.
Advantage:
A: Mass production has high efficiency and can achieve automated production.
B: High material utilization rate, good product size stability, and good surface quality.
C: Suitable for producing products of various sizes and shapes, with high precision.
Disadvantages:
A:Mold production and manufacturing are complex and costly. Low production leads to excessively high costs for a single product.
B: Not suitable for producing large-sized products.
3.Scope of application
Compression molding: More suitable for producing high demand, small-scale products, as well as larger flat products. Due to its smoother surface and more stable quality, it is also applied in some fields that require high product quality, such as weapons, aircraft, missiles, satellites, etc.
Injection molding: widely used in various industries, such as automotive parts, home appliances, daily necessities, medical devices, industrial components, and more. It can produce various complex plastic products with high production efficiency and relatively low cost.