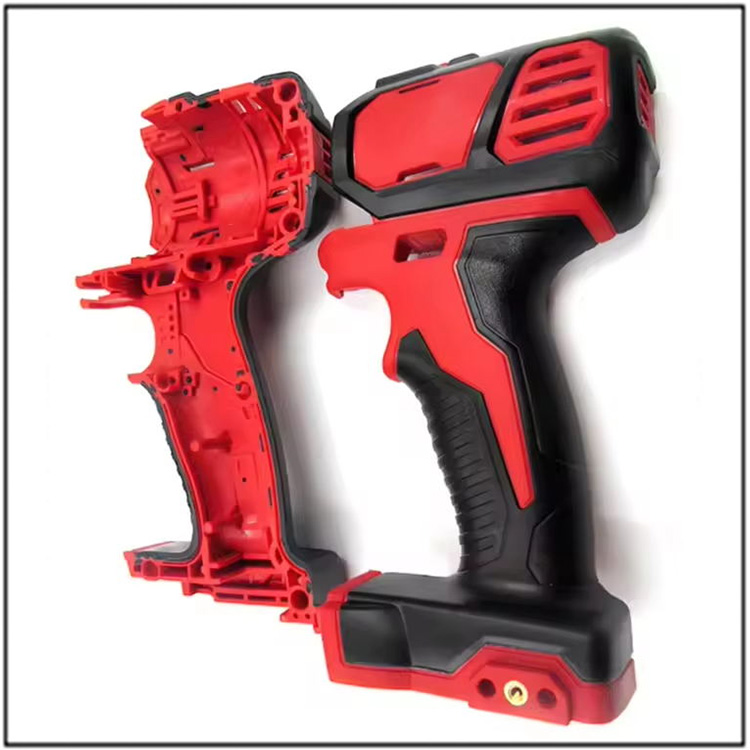
How to SolveThe Color Difference Problem in Injection Molding?
Color difference is a common and headache inducing issue in the injection molding process. Color difference not only affects the appearance of the product, but may also lead to customer complaints and returns. Therefore, solving the color difference problem in injection molding is the key to ensuring product quality. This article will share several effective methods to help you solve color difference problems in injection molding.
1.The selection of raw materials is the first step in solving color difference problems. In injection molding, different batches of raw materials may cause color differences. Therefore, it is recommended to choose raw material suppliers with stable quality to ensure the consistency of raw materials. In addition, the occurrence of color differences can be reduced by strictly controlling the color and quality of raw materials.
2.Changes in production process parameters can also cause color differences. During the injection molding process, parameters such as injection speed, injection pressure, mold temperature, and cooling time should be strictly controlled. Maintaining the stability of these parameters can effectively reduce color differences. For example, in the production process, the stability of the injection molding machine can be ensured by regularly checking and adjusting its process parameters.
3.Color masterbatch is an important factor in determining the color of injection molded products. To avoid color difference, it is necessary to choose a supplier of color masterbatch with stable quality to ensure the consistency of the color masterbatch. In addition, when using color masterbatch, the following points should be noted:
-Uniform mixing: Ensure that the color masterbatch and base material are mixed evenly, which can reduce color difference.
-Addition ratio: Strictly add color masterbatch according to the formula requirements to avoid color difference caused by improper addition ratio.
-Storage conditions: Color masterbatch should be stored in a dry and cool environment to avoid moisture and deterioration.
The stability of the equipment also has a significant impact on color difference control in injection molding processing. Regular maintenance and calibration of equipment to ensure the normal operation of injection molding machines and molds can reduce color differences caused by equipment failures. For example, key components such as the temperature control system and pressure system of the injection molding machine can be regularly inspected to ensure their good working condition.
Strengthening quality inspection is an important means to solve the problem of color difference in the injection molding process. By establishing a strict quality inspection process, color difference issues can be detected and resolved in a timely manner. For example, color sampling can be conducted during the production process to adjust production parameters in a timely manner and ensure the consistency of product colors. In addition, professional testing equipment such as colorimeters can be used to accurately measure the color of the product to ensure that it meets the requirements.