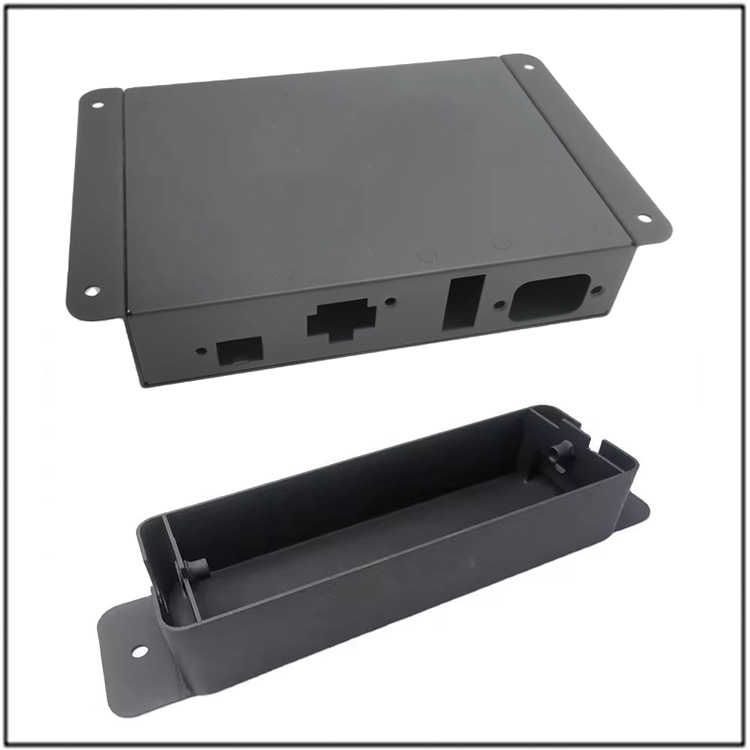
The Causes And Solutions of Common Burrs in Metal Stamping
1.Thick and high burrs are generated around the perimeter
The collapse angle and inclination angle of the shear section are large, while the middle presents a clear concave shape. The burrs are not only high, but also the section is triangular, which cannot be removed without the use of a file. These stamped parts are usually defective products.
Causes: (1) Excessive gap, (2) During multiple grinding, the verticality of the concave die decreases. For fully tapered concave dies, it is due to exceeding the tolerance caused by re grinding.
terms of settlement
Narrowing the gap: (1) Simple in shape, can be reworked when the volume is small; (2) Products with small and thin stamping can be subjected to electrical discharge hardening processing; (3) Annealing the mold, repairing the cutting edge, followed by heat treatment and grinding, (4) welding repair treatment, (5) using a mold pad when pressing the insert block, and processing after pressing out the cutting edge.
The causes and solutions of common burrs in metal stamping
2.Uneven height of burrs
If the gap is too large or too small, the height of burrs will increase. Among them, if the gap is too large, triangular burrs will be generated, and the thickness will increase. If the gap is too small, the burrs will be thin and high, resulting in secondary shear.
Causes: (1) Local inconsistency in gaps, (2) Local deviation caused by edge collapse, (3) Uneven height of burrs due to mold eccentricity, a. Poor mold installation, b. Poor assembly of guide columns, (4) Loose guide columns. (5) The accuracy of the press is poor.
Solution: (1) After deburring, if the cutting section shape of the product is uneven, it is because the gap is too large or too small locally, so it needs to be corrected. (2) The cutting edge is subject to local wear, or due to poor quenching hardness, local collapse occurs, and the root of burrs increases, so grinding is required. (3) The convex mold and concave mold are not concentric, which is due to half of the shear section being too large and the other half being too small. This is easy to understand. If it is due to poor assembly of the mold or guide column, adjustments can be made. However, if there is a change in the position of the mold core during each stroke, it is due to the loosening of the mold assembly part, and the mold core needs to be removed and tightened to correct the mouth (4). During stamping, due to the effect of thrust, non concentricity will occur. When the side bearing block or guide plate is subjected to force, in order to ensure accuracy, guide rods must be used. However, if the concentricity is not good after using guide columns, it is due to the difference in the quality of the guide columns. (5) The press is not good.
3.Large burrs (compression burrs) appear at the shear section
A noticeable tongue shaped part appears at a certain point of the shear section, which is called a compression burr.
Causes: (1) The overall gap is too small, and there is a corner collapse or gap at a certain point of the concave die edge. (2) There is a reverse taper at the back corner of the concave die. (8) The concave die hole is difficult to precision machine, with rough surfaces that crush the high part of the crack surface.
Solution: (1) Adjust the gap and grind the cutting edge. (2) Use a grinding wheel to remove the bright corner of the concave mold caused by repeated collisions. (3) Repair the part of the mold hole with severe contact spots on the vertical wall.
The causes and solutions of common burrs in metal stamping
4.The cutting section presents linear reinforcement bars
The so-called linear reinforcement refers to the phenomenon of convex or concave lines appearing at the cutting section.
Causes: (1) There is a gap or blade damage in a certain part of the concave mold, (2) Due to improper or insufficient selection of lubricant, the transverse tool is eroded, (3) Broken chips or foreign objects are mixed in and adhere to the mold.
Solution: (1) The mold gets stuck during the centering operation, or due to the high hardness of the mold, it may break or roll the blade. The former is best to grind and bite the dead part, while the latter is best to reduce the hardness of the mold, otherwise it will cause breakage and blade rolling again. (2) If the blank is stuck in the inner wall of the mold and scratches the mold due to heat generated during the stamping process, the lubricant must be changed while using the back corner. (3) If defects occur on the inner wall of the concave mold due to shrinkage or foreign matter melting, measures must be taken to prevent dirt from adhering to the blank.