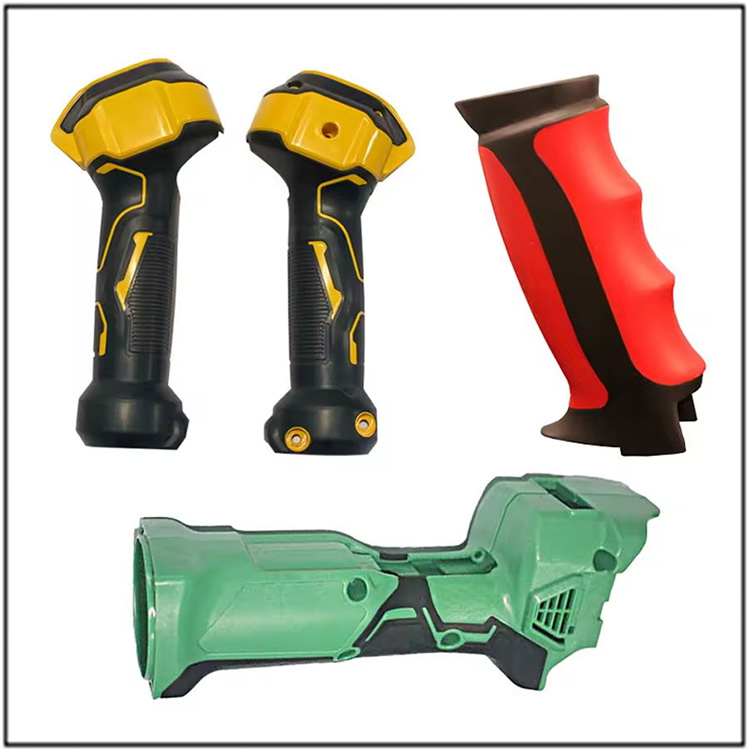
How Do Shrinkage Marks Occur in Injection Molding?
In the field of injection molding, shrinkage marks are a common and headache inducing issue. So, what exactly are shrinkage marks? How was it generated? Today, let's explore this topic together and provide some practical solutions for everyone.
Firstly, let's understand the definition of shrinkage marks. Shrinkage marks, also known as dents, sinkholes, or settlement spots, are a local collapse phenomenon that occurs on the surface of injection molded parts. It usually appears far away from the sprue, as well as at the thick walls, ribs, protrusions, and embedded parts of the product. Shrinkage marks not only affect the appearance quality of the product, but may also have adverse effects on its performance and structure.
So, how do shrinkage marks occur? This mainly involves multiple aspects such as materials, molds, injection molding machines, and processes.
From a material perspective, excessive shrinkage of plastic is an important reason for the formation of shrinkage marks. When plastic material is filled into the mold cavity in a molten state, it gradually cools and solidifies, and undergoes volume shrinkage. If the shrinkage rate of plastic is too high, shrinkage marks are prone to occur during the cooling process.
Mold design is also an important factor affecting the occurrence of shrinkage marks. Unreasonable product design, excessive or uneven product wall thickness, unreasonable gate position, too small gate, and uneven mold cooling can all lead to the formation of shrinkage marks. For example, excessive or uneven wall thickness of the product can lead to inconsistent shrinkage of various parts during the cooling process, resulting in shrinkage marks; If the gate position is unreasonable or the gate is too small, it will affect the flowability and filling effect of the plastic, and it is also easy to produce shrinkage marks.
The performance status of injection molding machines can also affect the generation of shrinkage marks. Severe wear of the check ring, screw, or plunger can cause injection pressure to be unable to be transmitted to the mold cavity, resulting in insufficient feeding; Leakage of molten material during injection and pressure maintenance can also reduce the filling pressure and material quantity, further leading to the formation of shrinkage marks.
In addition, the setting of process parameters is also an important factor affecting the occurrence of shrinkage marks. Unreasonable process parameter settings such as high melt temperature, short injection time or holding time, low injection pressure or holding pressure, and too fast injection speed can all lead to the formation of shrinkage marks.
So, how to avoid shrinkage marks in injection molding? Firstly, we can start with material selection and try to choose plastic materials with lower shrinkage rates. Secondly, in terms of mold design, it is necessary to design the product structure reasonably, optimize the gate position and size, and ensure uniform cooling of the mold. In addition, we also need to regularly inspect and maintain the injection molding machine equipment to ensure its normal operation. In terms of process parameter settings, it is necessary to adjust the melt temperature, injection time, holding time, injection pressure, and injection speed according to the actual situation to reduce the occurrence of shrinkage marks.
Finally, I would like to say that although shrinkage marks are common in injection molding, they are not inevitable. As long as we master the correct solutions and techniques, we can effectively reduce the occurrence of shrinkage marks and improve the quality and performance of products.