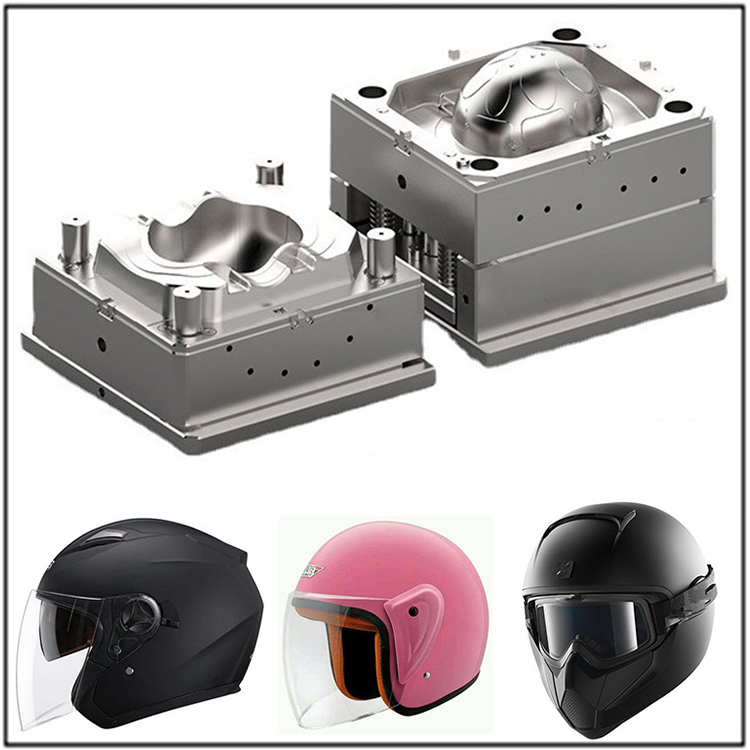
How Can Mold Manufacturing Become The Core Driving Force For Industrial Upgrading?
With the intensification of market competition, enterprises have increasingly high requirements for mold accuracy, efficiency, and cost control. Advanced mold manufacturing technology is reshaping the industry landscape in a digital and intelligent way, providing better solutions for customers in various fields.
The precision of mold manufacturing directly affects the quality and performance of the final product. The modern machining process with numerical control technology (CNC) as its core achieves micrometer level precision cutting and forming through computer programming, especially suitable for fields such as automobiles, electronics, medical equipment, etc. that require extremely high levels of complex structures. For example, in the manufacturing of automotive panel molds, five axis linkage CNC machine tools can complete multi angle surface machining at once, avoiding the accumulation of errors caused by multiple clamping in traditional processes, and ensuring the consistency and smoothness of the mold surface. In addition, the application of CAD/CAM software directly converts design data into machining paths, further shortening the R&D cycle, reducing trial and error costs, and shifting mold manufacturing from experience driven to data-driven.
Efficiency improvement is another important direction for the iteration of mold manufacturing technology. High speed cutting (HSM) technology combined with high hardness tool materials can reduce machining time while extending mold life. A certain household appliance enterprise has reduced the delivery cycle of injection molds from 30 days to 18 days by introducing intelligent production lines, resulting in a 12% increase in yield rate. This efficiency innovation is not only reflected in the processing stage, but also runs through the entire lifecycle management - monitoring the mold usage status in real time through IoT technology, predicting maintenance needs, and avoiding losses caused by unplanned downtime. For mass production scenarios, mold manufacturing companies can also adopt modular design concepts to achieve rapid cavity replacement and meet the flexible production needs of multiple varieties and small batches.
At the industry application level, innovation in mold manufacturing is breaking through traditional boundaries. Taking the field of new energy as an example, precision molds for power battery casings need to balance lightweight and structural strength. Through topology optimization design and simulation analysis, the enterprise has successfully reduced the weight of the casing by 15% while maintaining impact resistance. In the consumer electronics industry, the nano injection mold for the phone frame achieves seamless integration of metal and plastic through micro hole processing technology, significantly improving product aesthetics and durability. These cases indicate that mold manufacturing has evolved from a single processing service to an integrated solution of "design manufacturing optimization", becoming an important partner for customer product innovation.
Faced with future challenges, mold manufacturing enterprises need to continuously strengthen their technological accumulation and service capabilities. From breakthroughs in materials science, such as the application of 3D printed metal powders, to the integration of process chains, such as the composite application of electrical discharge machining and laser cladding, technological fusion is opening up new possibilities. At the same time, building a transparent service system and providing rapid response support will be the key to winning customer trust.