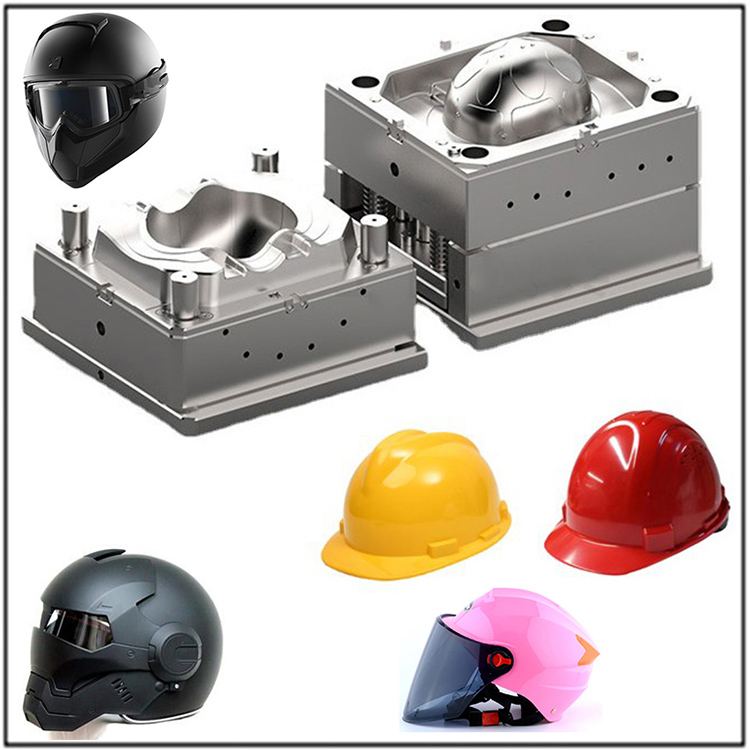
Thermoplastic Injection Molding Mold: Disassembly of 6 Core Components
The structural design of injection molding molds directly determines the success or failure of production behind injection molded products such as phone cases and car lampshades. A standard set of thermoplastic injection molding molds typically consists of six modules, each with hidden secrets to cost reduction and efficiency improvement.
1.Shaped parts: the "soul" that determines the shape of the product
The core (convex mold) and cavity (concave mold) are the core of the mold, directly shaping the shape of the product. For example, the cavity of a mobile phone case mold needs to be accurately replicated with a curved surface curvature, with a tolerance controlled within ± 0.05mm. A certain mold factory once suffered a loss of 200000 yuan in orders due to insufficient polishing of the mold cavity, resulting in the appearance of "orange peel patterns" on the outer shell.
2.Pouring system: the "highway" of melt flow
Including main channels, branch channels, and gates. Taking a mineral water bottle mold as an example, the diameter of the sprue is only 1.2mm, but the melt needs to be injected into the mold cavity within 0.3 seconds. Unreasonable channel design can lead to weld marks, such as a 30% decrease in product strength due to excessively long branch channels on a household appliance casing.
3.Guiding mechanism: the "sea fixing needle" for mold precision
The fitting accuracy of the guide post and guide sleeve should reach H7/f6, which is equivalent to 1/5 of the thickness of a human hair. A certain car mold was not replaced due to the wear and tear of the guide column, resulting in a misalignment of 0.1mm during mold closing and flying edges, consuming an additional 80 kilograms of raw materials per day.
4.Demoulding mechanism: Avoid the "gentle pushing hand" of the top white
The ejector pin, push plate, and other components form the demolding system. Laptop shell molds commonly use flat top pins, which increase the area by three times to avoid top whitening. A certain factory once had an uneven distribution of top pins, resulting in a deformation rate of up to 15% for the shell.
5.Temperature control system: the "invisible engine" of cooling efficiency
The diameter and layout of water pipes affect the cooling time. Like the mold for mobile phone battery cases, the spiral waterway cools 40% faster than the straight waterway, and the daily output of single-mode is increased by 2000 pieces.
6.Supporting structure: the "skeletal framework" of the mold
The mold frame and cushion block can withstand injection pressure (usually 100-150MPa). A thin-walled plastic mold was forced to be scrapped in advance due to insufficient rigidity of the mold frame, resulting in deformation of the mold cavity after 50000 production cycles.
Industry data: According to the Injection Molding Association, 80% of mold failures are caused by component compatibility issues. A precision mold factory has increased the lifespan of molds from 800000 to 1.2 million times and reduced maintenance costs by 40% through standardized assembly of six major modules.