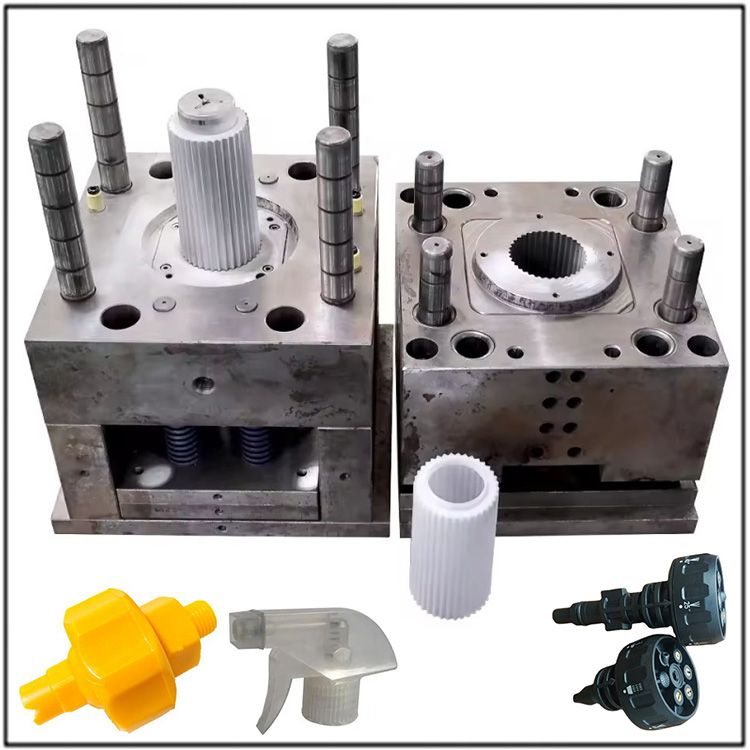
Injection Mold Fitting ! 5 Keys Points to Avoid 90% of Production Problems
The assembly accuracy of injection molds directly determines the quality and production efficiency of plastic products. Whether it is new mold debugging or old mold maintenance, mastering these 5 assembly points can significantly reduce common problems such as burrs, material shortages, and mold jamming.
1.Parts cleaning: Dust is the invisible killer of molds
Before assembly, it is necessary to clean the oil stains and metal debris on the surface of the core and cavity with alcohol or compressed air. A factory once had sand particles embedded in the mold of a phone case during plastic mold closing due to incomplete cleaning, resulting in the appearance of pockmarks on the surface of the product and a 20% increase in scrap rate. Pay special attention to the gaps between precision components such as sliders and top pins to avoid foreign objects getting stuck in the moving mechanism.
2.Accurate positioning: 0.02mm error affects the overall situation
The positioning ring and guide column sleeve of the mold must be welded tightly. Taking the car bumper mold as an example, if the parting surface is misaligned by more than 0.05mm, flying edges will occur during injection molding, and the cost of later mold repair will increase threefold. During assembly, red lead powder can be used to check the contact area to ensure that the positioning surface adhesion rate is greater than 95%.
3.Tightening torque: The tighter the screw, the better
The screws of the core fixing plate, mold foot and other components need to be tightened according to the drawing torque (such as M12 screws, which are usually 50N · m). A certain household appliance mold factory once caused deformation of the template due to overly tight screws, resulting in shrinkage marks on the injection molded parts. The problem was eventually solved by replacing the entire set of templates. It is recommended to use a torque wrench to avoid manual operation. 4. Sports test: Simulate 100 times of opening and closing the mold
After assembly, manually push the slider and ejector pin to check for any jamming. A certain toy mold had a needle hole that was not chamfered, causing the needle to break during testing and the core to be pulled by debris from the needle. Recommend lubricating moving parts with butter, observing whether the return is smooth, and recording whether the ejection stroke meets the design value.
4.Trial mold verification: Three dimensions of first article inspection
① Size: Use three coordinate measurement to determine the key hole position. For example, the deviation of the camera hole on the phone case should be less than ± 0.08mm;
② Appearance: Check if the parting line is uniform and if the flash thickness is less than 0.03mm;
③ Function: Test the assembly feel of buckles and bolts. For example, the buckle of a laptop case should be able to withstand 50 times of opening and closing without loosening.