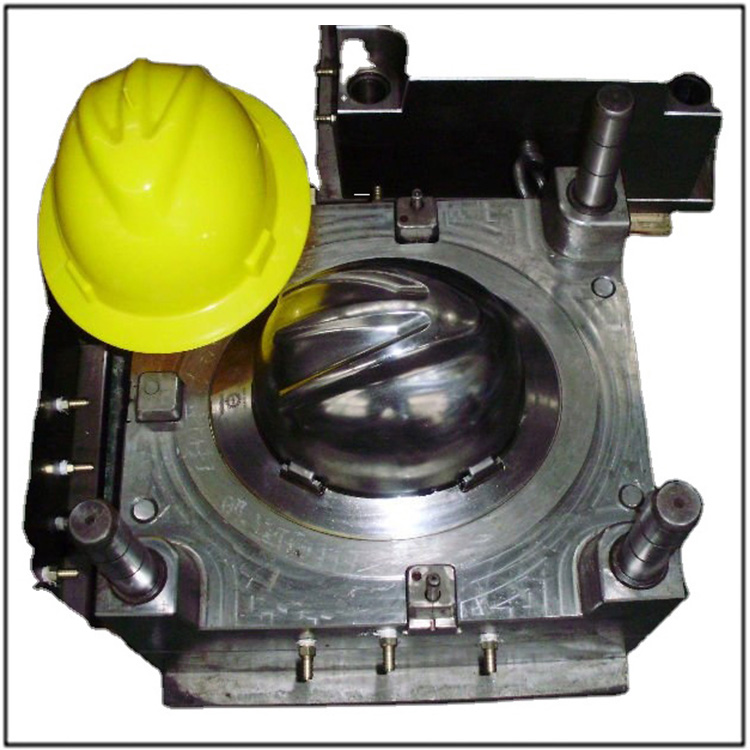
What Are The Produce Conditions For PET Injection Molding?
PET (polyethylene terephthalate) is a common engineering plastic widely used in food packaging, beverage bottles, electronic components, and other fields due to its high transparency, good strength, and strong chemical resistance. However, the process conditions for PET injection molding are relatively strict, and even a slight mistake may lead to product defects. So, what are the key points of PET injection molding process conditions? Let's analyze step by step from raw materials to molding!
Firstly, drying of raw materials is the first and most important step in PET injection molding. PET material is highly hygroscopic. If the raw material contains too much moisture, defects such as bubbles and silver lines will occur during the injection molding process, seriously affecting product quality. Therefore, PET raw materials need to be dried at 65-70 ℃ for 4-6 hours before injection molding to ensure a moisture content below 0.02%.
Secondly, the control of injection molding temperature is crucial. The melting temperature range of PET is relatively narrow, usually controlled between 260-290 ℃. The temperature distribution of the material barrel needs to gradually increase from the feeding port to the nozzle to ensure uniform melting of the plastic. The nozzle temperature is generally slightly lower than the temperature at the front end of the barrel to prevent drooling or wire drawing. The mold temperature should be controlled between 10-50 ℃. Excessive mold temperature will prolong the cooling time, while excessively low temperature may lead to increased internal stress in the product.
The next step is to adjust the injection pressure and injection speed. PET has good fluidity, but the injection pressure still needs to be controlled between 80-120MPa to ensure that the melt can fully fill the mold cavity. The injection speed needs to be adjusted according to the product structure and wall thickness, usually using medium to high speed injection to avoid insufficient filling caused by rapid cooling of the melt.
The holding pressure and holding time are also key parameters in PET injection molding. The holding pressure is usually 50% -70% of the injection pressure, and the holding time is determined based on the product wall thickness and cooling rate, usually 5-15 seconds. Proper pressure maintenance can effectively reduce product shrinkage and deformation, and improve dimensional accuracy.
In addition, the setting of cooling time directly affects production efficiency and product quality. The cooling time of PET is usually longer, depending on the product wall thickness and mold temperature. Insufficient cooling may cause product deformation, while excessive cooling can prolong the production cycle. Therefore, it is necessary to optimize the cooling time according to the actual situation.