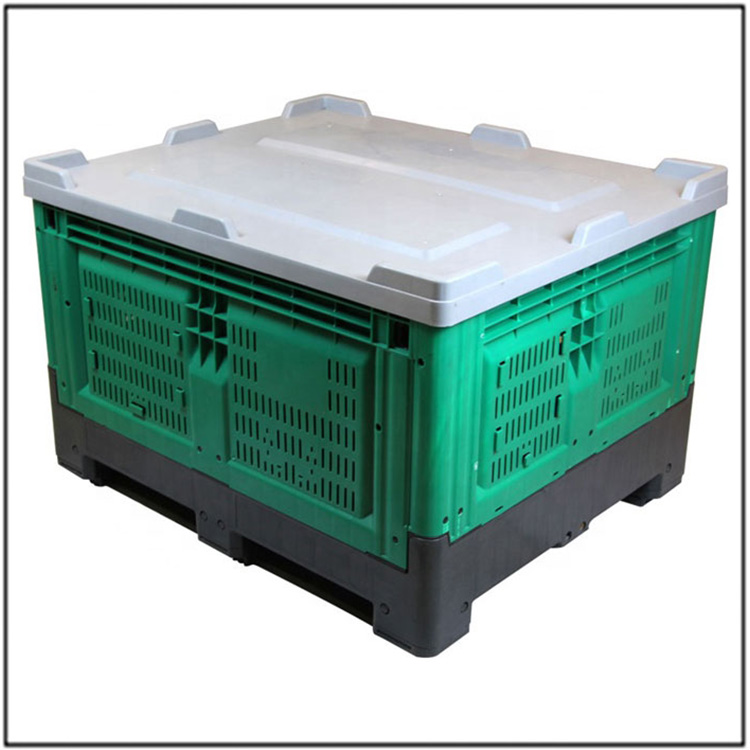
What Are The Main Steps and Types Required For Injection Molding?
Injection molding is one of the most commonly used processes in plastic processing, covering almost every field from daily necessities to high-tech products. It forms various shapes of products by injecting molten plastic into a mold, cooling and solidifying it. So, what are the main steps of injection molding? What are the common types? Let's comprehensively analyze this efficient process from basics to applications!
Firstly, the main steps of injection molding can be divided into the following stages. The first step is raw material preparation. Plastic particles or powders need to be dried to remove moisture and avoid bubbles or defects during the molding process. The second step is heating and plasticizing. The plastic raw material is heated and melted in the barrel of the injection molding machine, and a uniform melt is formed through the rotation and shearing of the screw. The third step is injection and pressure holding. The molten plastic is injected into the mold cavity under high pressure, and after filling, a certain pressure is maintained to ensure that the product is dense and defect free. The fourth step is cooling and solidification, where the plastic in the mold gradually solidifies into shape with the help of a cooling system. The final step is mold opening and ejection. The mold is opened and the product is ejected by the ejection mechanism, completing the entire injection molding process.
Secondly, the types of injection molding can be classified into multiple types based on the different processes and products. The most common is ordinary injection molding, which is suitable for the production of most plastic products, such as daily necessities, electronic casings, etc. Next is two-color injection molding, which combines two different colors or materials of plastic together through two injection molding processes. It is commonly used to make products such as buttons and handles. There is also gas assisted injection molding, in which gas is injected during the injection process to form a hollow structure, reducing material usage and improving product strength, suitable for large or thick walled products. In addition, there is also micro injection molding used for producing micro parts such as medical devices, optical components, etc.
In actual production, the steps and types of injection molding need to be adjusted according to the specific needs of the product. For example, high-precision products may require longer cooling times and higher injection pressures, while complex structured products may require the use of multi cavity molds or hot runner systems to improve production efficiency.