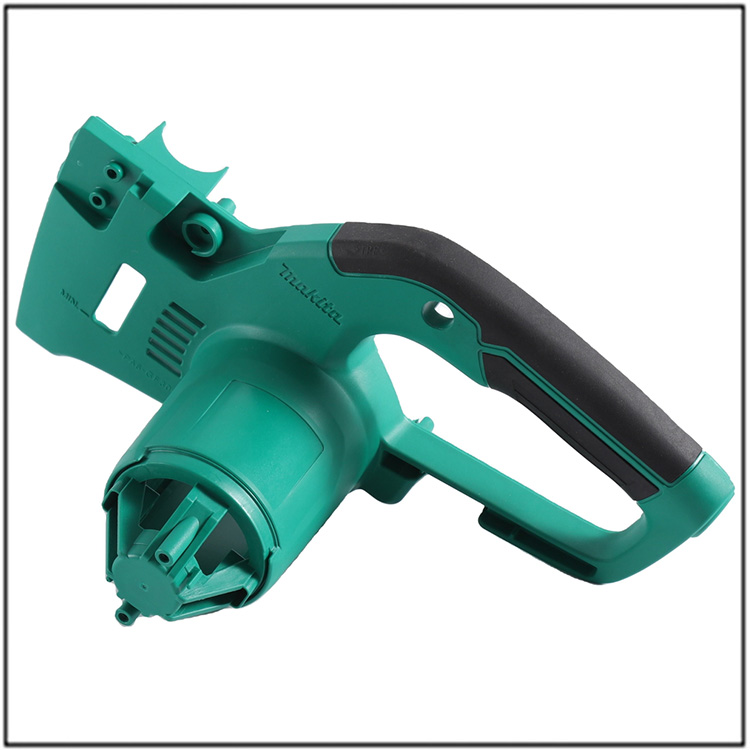
The Runner of the Plastic Molds
In the world of plastic molds, there is a crucial but often overlooked part - the flow channel. Perhaps you are not unfamiliar with plastic molds. Plastic water bottles, plastic toys, etc. used in daily life are all injection molded through plastic molds, and flow channels play an indispensable role in them.
Simply put, the flow channel is the passage in a plastic mold that guides the plastic melt from the injection molding machine nozzle into the mold cavity, just like the transportation road in the city, bearing the heavy responsibility of transportation. In the process of injection molding, plastic raw materials are heated and melted, and must pass through flow channels to reach various cavities of the mold, and then cooled and molded into the plastic products we need.
The function of a channel is not simple. Firstly, it ensures that the plastic melt can be evenly distributed to each cavity. In multi cavity molds, if the flow channel design is not reasonable, some cavities may be filled first, some cavities may be filled later, and even some cavities may not be completely filled. This can lead to uneven quality of plastic products, inconsistent size and weight, and possible defects such as missing materials and burrs. Secondly, the flow channel can reduce the pressure loss and heat dissipation of plastic melt during the flow process. Reasonable channel size and shape can reduce the flow resistance of the melt, allowing it to flow more smoothly while maintaining an appropriate temperature, which is beneficial for molding.
The types of flow channels are diverse and abundant. The common channel is the main channel that connects the injection molding machine nozzle with the diversion channel or cavity, usually conical in shape, facilitating the flow and demolding of plastic melt. The diversion channel distributes the plastic melt sent by the main channel to various cavities. Depending on the structure and cavity layout of the mold, the shape and size of the diversion channel vary, commonly including circular, trapezoidal, U-shaped, etc. The ratio of surface area to volume of a circular channel is the smallest, resulting in minimal heat loss and pressure drop when the melt flows through it, making it an ideal shape. However, in practical processing, due to limitations such as mold structure, other shapes may also be used.
The design of the flow channel is crucial in the design and manufacturing of plastic molds. It is necessary to comprehensively consider factors such as the type of plastic, the shape and size of the product, and the structure of the mold, and carefully design the length, diameter, shape of the runner, as well as the position and size of the sprue (the connection part between the runner and the mold cavity). Only by designing a reasonable flow channel system can the injection molding process proceed smoothly and produce high-quality plastic products.