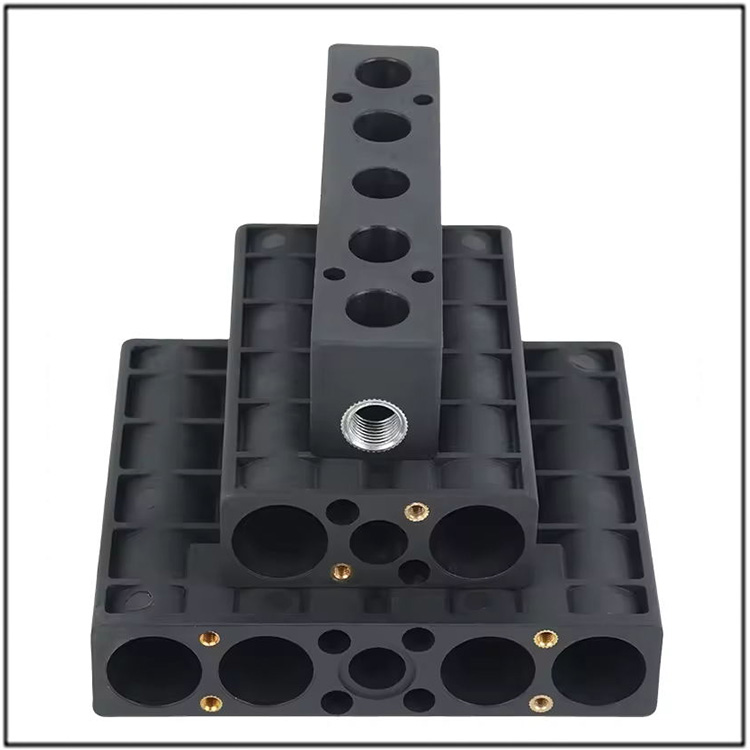
The Five Major Conditions For Injection Molding?
In the manufacturing industry, injection molding is a common and important processing technique. Plastic products commonly found in daily life, such as plastic water bottles, toys, electronic product casings, etc., are mostly manufactured through injection molding. To successfully complete injection molding, the following five key conditions are essential.
1.Suitable plastic raw materials
Different types of plastics have different characteristics. For example, polyethylene (PE) has good chemical resistance and flexibility, and is commonly used in the manufacture of plastic bags, plastic films, and other products; Polycarbonate (PC) has high strength, high transparency, and good heat resistance, and is often used in the production of eyeglass lenses, car lampshades, and so on. Before injection molding, it is necessary to select suitable plastic raw materials based on the product's usage and performance requirements to ensure the quality and performance of the final product.
2.Accurate temperature control
On the one hand, it is necessary to heat the plastic raw materials to a molten state so that they can flow smoothly inside the injection molding machine and fill the mold cavity. The melting points of different plastics are different, for example, the melting point of polypropylene (PP) is about 160-170 ℃, while the melting point of polystyrene (PS) is around 100-110 ℃. Therefore, it is necessary to accurately control the temperature of the injection molding machine barrel to ensure that the plastic reaches the appropriate melting state. On the other hand, the temperature of the mold also needs to be controlled. A suitable mold temperature helps to evenly cool and solidify the plastic melt, avoiding defects such as deformation and shrinkage marks in the product.
3.Proper pressure regulation
Injection pressure is the driving force for rapidly filling the mold cavity with plastic melt. If the pressure is too low, the plastic melt may not be able to fill the entire cavity, resulting in product shortage; Excessive pressure may cause the product to flash and even damage the mold. The holding pressure is the pressure applied after the plastic melt fills the mold cavity to compensate for the cooling shrinkage of the plastic. Appropriate holding pressure can reduce the shrinkage marks and internal voids of the product, and improve the dimensional accuracy and density of the product.
4.Reasonable time setting
The injection time determines the speed at which the plastic melt fills the mold cavity. If it is too short, it may lead to insufficient filling, while if it is too long, it will affect production efficiency. The holding time should be determined based on the wall thickness of the product and the characteristics of the plastic to ensure that the plastic is adequately replenished during the cooling shrinkage process. Cooling time is to allow plastic products to fully cool and solidify in the mold, reaching a strength that can be demolded. If the cooling time is insufficient, the plastic product is prone to deformation, and if the cooling time is too long, it will reduce production efficiency.
5.Precise mold design and manufacturing
A precision mold needs to have a reasonable flow channel system to ensure that the plastic melt can be evenly distributed to each cavity; Accurate cavity size ensures that the dimensional accuracy of the product meets the requirements; A good demolding mechanism enables the product to smoothly detach from the mold without damage. For example, when producing plastic toys with complex shapes, the design of the mold should fully consider the structural characteristics of the toy, and reasonably set the parting surface and core pulling mechanism to ensure the smooth molding of the toy.