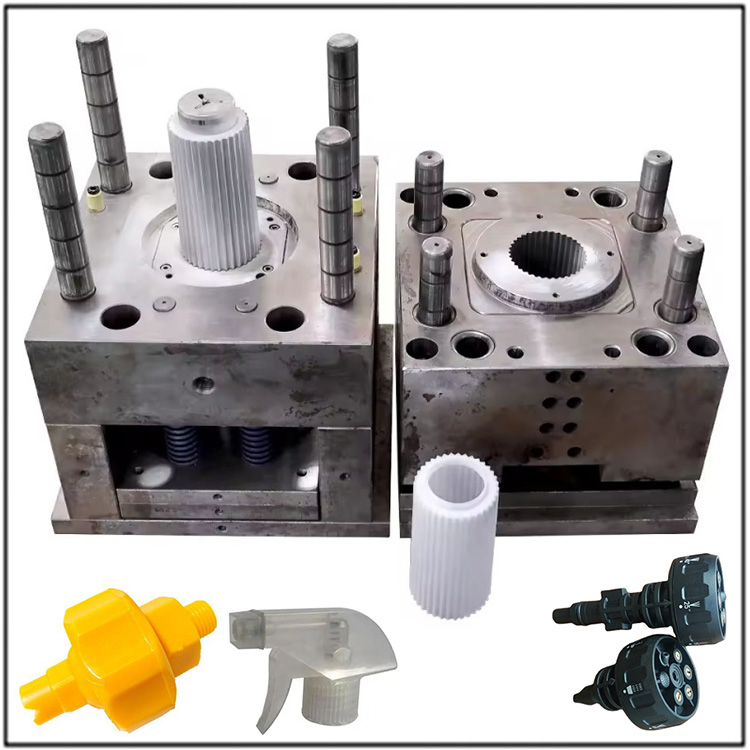
How to Connect The Plastic Mold Slide Block to The Insert?
In the world of plastic molds, the connection method between the slider seat and the insert is crucial. Their proper connection not only affects the performance of the mold, but also determines the quality of the product. Today, let's delve into several common ways of connecting plastic mold slider seats to inserts.
1,Screw connection is a common connection method. By machining screw holes separately on the slider seat and insert, use screws to tightly fix them together. This connection method has the advantages of firm connection and easy disassembly. When replacing inserts or repairing molds, screws can be easily unscrewed for operation. At the same time, screw connections can also withstand a certain injection pressure, ensuring that there will be no loosening during the production process.
2,Swallowtail groove connection is a high-precision connection method. Process a dovetail groove shape on the slider seat, and design the insert to match it. Connect the two by inserting the insert into the dovetail groove. The advantage of this connection method is that it is tightly connected, has high accuracy, and can effectively prevent displacement of the inserts during the production process. In addition, the dovetail groove connection can also withstand significant lateral forces, making it suitable for some plastic molds that require high precision.
3, Hanging table connection is a simple and effective connection method. Design a hanging platform on the insert, and process corresponding grooves on the slider seat. Insert the mounting bracket of the insert into the groove of the slider seat to achieve the connection. The advantage of this connection method is that it is easy to install and does not require screws or other connectors, which can save the installation time of the mold. At the same time, the hanging platform connection also has a certain strength, which can meet the production needs of general plastic molds.
4,Hot press connection is a connection method that utilizes the principle of thermal expansion and contraction. Heat the slider seat and insert to a certain temperature to cause their dimensions to expand. Then quickly insert the insert into the slider seat, and after cooling, the two will be tightly connected together. The advantage of this connection method is that the connection is firm and there will be no looseness. However, hot pressing connection requires the use of professional heating equipment, and the operation is relatively complex.
When choosing a connection method, it is necessary to comprehensively consider factors such as specific mold structure, production requirements, and cost. Only by choosing the appropriate connection method can the performance of plastic molds and the quality of products be ensured. In the manufacturing and use of plastic molds, we should fully recognize the importance of connecting the slider seat with the insert, constantly explore and innovate connection methods, and provide more reliable guarantees for the production of plastic products.