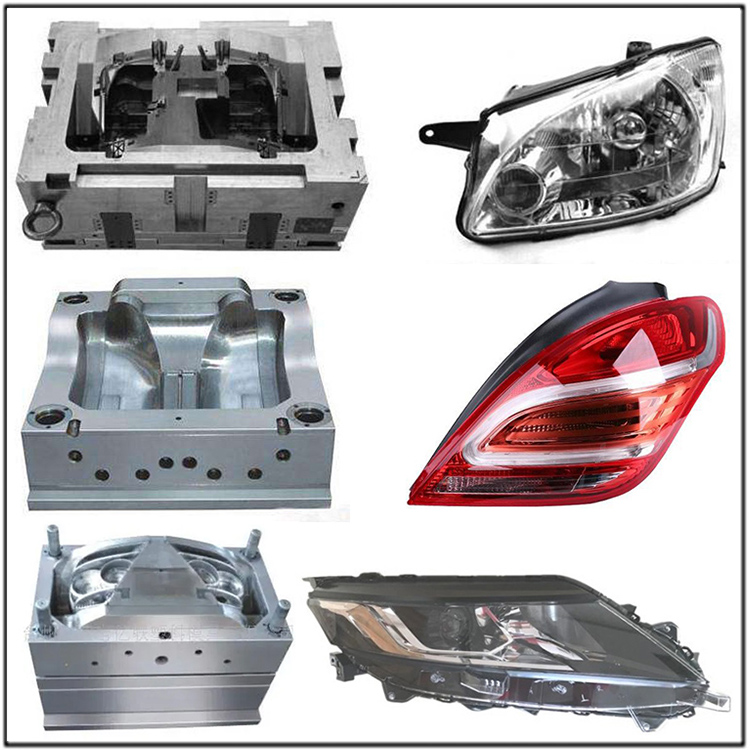
What are The Common Defects and Causes of Injection Parts?
In the injection molding industry, the quality of injection molded parts has always been a focus of attention for manufacturers. Understanding the common defects and their causes in injection molded parts is of great significance for improving product quality and reducing production costs.
1,Shrinking
Shrinkage is one of the common defects in injection molded parts. It is manifested as local depressions on the surface of the product.
The main reasons include: insufficient injection volume, shrinkage of plastic during cooling in the mold, and insufficient amount of replenished plastic; The holding time is too short to effectively compensate for the shrinkage of plastic parts; The mold temperature is too high, causing slow cooling and increased shrinkage of the plastic.
For example, in the production of mobile phone cases, if the injection volume is not set properly, shrinkage may occur at the corners of the case.
2,Flying edge
Flying edge, also known as overflow edge or sharp edge, refers to the excess plastic appearing at the edge of an injection molded part. This is usually due to insufficient mold clamping force, which cannot effectively lock the mold; Excessive injection pressure leads to plastic extrusion from the parting surface; The clearance between the molds is too large, which makes it easy for plastic to overflow.
For example, when manufacturing plastic toys, if the precision of the mold fit is not sufficient, it may cause burrs at the joints of the toy.
3,Bubble
Bubbles form inside or on the surface of injection plastic parts, affecting their appearance and performance. The cause may be insufficient drying of the plastic, which contains moisture and vaporizes to form bubbles during injection; The injection speed is too fast and it gets sucked into the air; Poor exhaust of the mold, unable to release gas.
Taking the production of plastic tableware as an example, if the plastic raw materials are not fully dried, bubbles may appear on the surface of the tableware. 4、 Silver thread pattern
Silver streaks are manifested as silver stripes on the surface of the product. The main reasons are that plastic decomposes and produces gases, impurities are present in the material, and the mold temperature is too low, which causes the plastic to condense too quickly.
If contaminated plastic materials are used in the production of automotive interior parts, silver wire defects may occur.
4,Weld mark
Weld marks refer to the marks formed at the confluence of two plastic streams. The reasons for this include unreasonable gate position, slow injection speed, and low mold temperature. When manufacturing plastic water buckets, if the sprue is not properly set, obvious weld marks may appear on the surface of the bucket.
5,Warping and deformation
Warping deformation refers to the twisting or bending of the shape of injection molded parts. This may be due to uneven cooling and inconsistent plastic shrinkage; Unreasonable mold structure leads to uneven force distribution on the product; Improper setting of injection molding process parameters.
For example, when producing plastic tablets, if the cooling system design is poor, the tablets may warp.
In short, understanding common defects and their causes in injection molded parts can help manufacturers take targeted measures for improvement, thereby improving the quality and production efficiency of injection molded products.