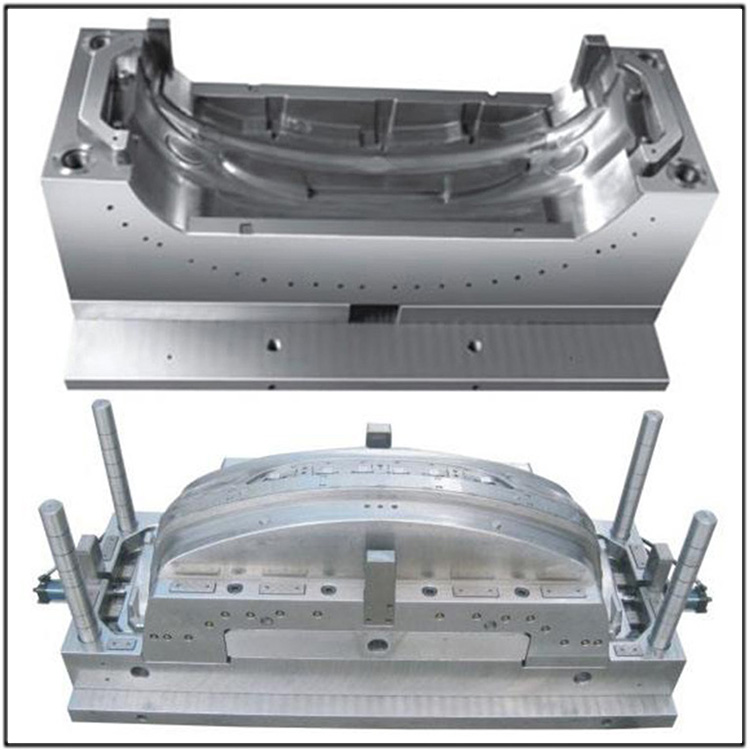
What areThe Differences Between Soft and Hard Molds in Mold Manufacturing?
In the field of mold manufacturing, soft mold and hard mold are two common concepts, but there are significant differences between them. For many industry practitioners and friends interested in molds, a clear understanding of these differences is crucial. Firstly, in terms of materials, soft molds usually use softer and easier to process materials such as aluminum, zinc alloys, etc. Hard molds often use materials with high hardness and strong wear resistance, such as mold steel.
In terms of production cost, the manufacturing cost of soft molds is relatively low. This is because its material cost and processing technology are relatively simple. Taking small-scale production or product development as an example, software modeling can help enterprises quickly verify the feasibility of product design while controlling costs. In contrast, the production cost of hard molds is higher, but their lifespan and stability advantages are obvious in large-scale production.
In terms of production cycle, the manufacturing cycle of soft molds is relatively short. This enables companies to obtain molds and conduct trial production in a short period of time. The manufacturing cycle of hard molds is longer due to their complex processing technology, which requires more time and effort to ensure the accuracy and quality of the molds. In terms of precision and surface quality of molds, hard molds usually have higher precision and better surface quality. This makes the produced products more accurate in size and more exquisite in appearance. Although soft molds are slightly inferior in accuracy and surface quality, they can meet basic requirements in the early stages of product development.
Looking at the service life of the mold again, hard molds have a longer service life due to their advantages in material and manufacturing technology, and can withstand a large number of production cycles. The service life of soft molds is relatively short, making them suitable for small-scale production or product development stages. For example, in the manufacturing of automotive parts, if it is a small-scale trial production of new vehicle models, soft molds may be used first to quickly obtain samples and conduct testing. When the vehicle model is determined and enters mass production, hard molds will be used to ensure production efficiency and product quality. For example, in the manufacturing of electronic product casings, soft molds may be used during the research and development stage to verify the design. Once the product is finalized, in order to meet the requirements of mass production and high quality, it will switch to hard molds.
In short, both soft and hard molds have their own characteristics and applicable scenarios. In practical applications, enterprises need to choose soft or hard molds reasonably based on their own production needs, cost budgets, and product characteristics to achieve the best economic and production benefits.