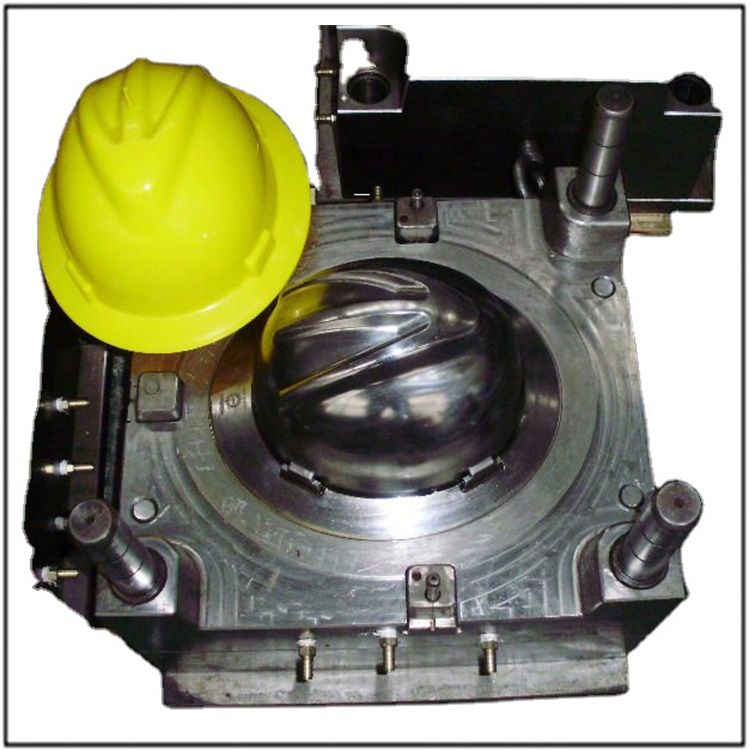
The Top of Ten Plastic Molding Processes
In modern industry, plastic products are ubiquitous, playing an important role in everything from daily necessities to high-tech fields. Understanding plastic molding technology is essential knowledge for professionals in related industries and friends interested in plastic processing. Next, let's take one minute to master the top ten plastic molding processes in detail!
1.Injection molding
Injection molding is one of the most commonly used methods in plastic processing. It heats the plastic to a molten state and then injects it into a closed mold cavity under high pressure. After the plastic cools and solidifies, the mold can be opened to obtain the molded plastic product. This process is suitable for manufacturing various products with complex shapes and high dimensional accuracy requirements, such as mobile phone cases, automotive parts, etc.
2.Extrusion molding
Extrusion molding is the process of using a screw or plunger to extrude hot melt plastic, which is continuously molded into a continuous profile with a constant cross-section under pressure. Common extruded products include pipes, sheets, films, wires and cables, etc.
3.Blow molding
Blow molding is mainly used to manufacture hollow plastic products. Firstly, the plastic preform is extruded or injection molded, then placed in a mold and inflated with compressed air until it adheres tightly to the mold cavity wall. After cooling and shaping, the product is obtained. For example, plastic bottles, containers, etc. usually use this process.
4.Compression molding
Directly add plastic into the open mold cavity, then close the mold. Under the action of heating and pressure, the plastic melts and fills the cavity, and after solidification and shaping, the product is obtained. This process is suitable for molding plastic products with simple shapes and large sizes.
Injection molding is an improvement on the basis of compression molding. Plastic is heated and melted in the feeding chamber, and under pressure, it enters the closed mold cavity through the pouring system. This process has high production efficiency and good dimensional accuracy of the products.
6.Roll molding
Roll molding is the process of loading plastic powder into a mold, and then slowly rotating the mold in a heating furnace to evenly adhere the plastic powder to the inner wall of the mold. After heating, cooling, and other processes, hollow plastic products such as large storage tanks and toys are finally obtained.
7.Enamel molding
Pour the paste plastic into the mold preheated to a certain temperature, and the paste plastic near the inner side of the mold cavity will be gel due to heat. Subsequently, pour out the unglued plastic paste, and after cooling the gelatinized plastic paste attached to the inner wall of the mold cavity, the hollow product can be obtained from the mold. Common enamel molded products include children's toys, car interiors, etc.
Inject liquid monomers or prepolymers into the mold, and under certain conditions, undergo polymerization or solidification reactions to form the product. This process is commonly used for manufacturing large or complex shaped products.
9.Transfer molding
First, heat and melt the plastic in the feeding chamber, and then enter the closed mold cavity through the pouring system under pressure. This process can produce some thin-walled products with high precision requirements.
10.Hot forming
Heat the plastic sheet to a softened state, and then shape it through methods such as molds, vacuum, or pressure. Common thermoformed products include food packaging, disposable tableware, etc. Mastering these technological knowledge will enable you to excel in the field of plastic processing, whether it is product design or production manufacturing, making you more proficient.