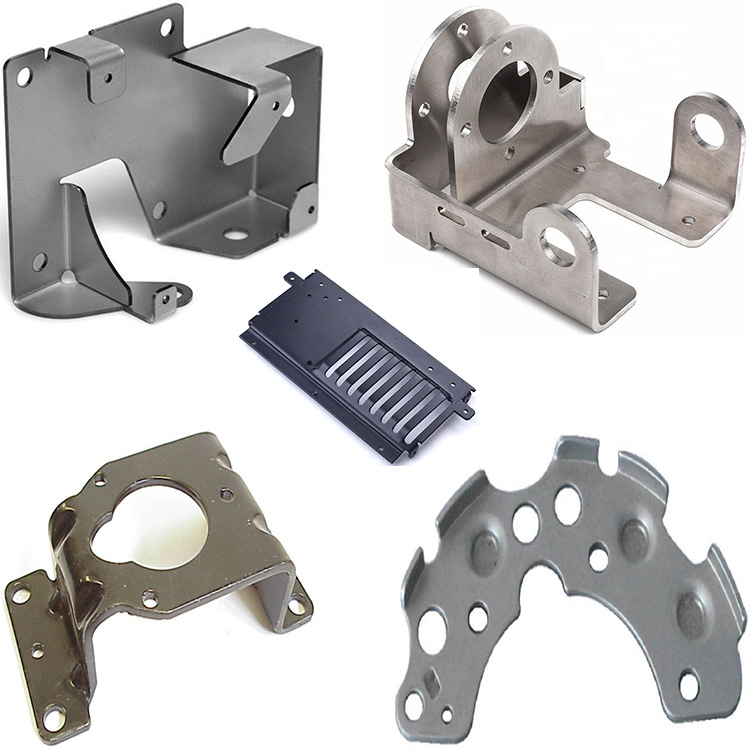
Metal Stamping Process: Cutting-edge Technology in Precision Manufacturing
Metal stamping, as a key technology in modern manufacturing, processes metal sheets into parts with specific shapes and sizes through precise molds and stamping equipment. This process plays an irreplaceable role in multiple industries such as automotive, aerospace, electronics, and building decoration.
Basic principles of metal stamping process
Metal stamping is a cold working process for metal sheets, which mainly includes the following basic steps:
Punching: Cutting metal sheets into parts of the desired shape through gaps in the mold.
Bending: causing plastic deformation of metal sheet without breaking, forming the desired bending shape.
Stretching: Under pressure, plastic flow occurs in a localized area of a metal sheet, forming a convex shape.
Flanging: A raised circular edge formed at the edge of a metal sheet to increase the strength of a component or to connect other components.
Mold Design and Manufacturing
Mold is the core of metal stamping technology, and its design and manufacturing directly affect the accuracy and quality of stamped parts. Modern mold design adopts high-precision CAD/CAM systems, which optimize mold design and achieve manufacturing accuracy through 3D modeling and simulation technology. The selection of mold materials is also crucial, usually using high-strength, high wear resistant alloy steel or hard alloy.
High precision stamping equipment
The accuracy and stability of stamping equipment are key to ensuring the quality of metal stamping parts. Modern stamping equipment adopts advanced servo motor drive and closed-loop control system to achieve high-precision positioning and pressure control. In addition, the rigidity and durability of the equipment are also important factors to consider when choosing stamping equipment.
Automation and Intelligent Production
The automated stamping production line achieves fully automated production from raw materials to finished products by integrating robotic arms, automatic feeding devices, and online detection systems. The intelligent production system integrates industrial Internet of Things (IIoT) technology to achieve real-time collection, analysis, and optimization of production data, improving production efficiency and product quality.
Quality Control and Testing
The quality control of metal stamping parts includes multiple aspects such as raw material inspection, mold debugging, process control, and finished product testing. Using high-precision measuring instruments such as coordinate measuring machines, optical projectors, etc., to detect the dimensional accuracy and shape accuracy of stamped parts. In addition, non-destructive testing techniques such as ultrasonic testing, X-ray testing, etc. are widely used to detect defects inside stamped parts.
Application of Materials Science
In the metal stamping process, the selection and performance of materials have a direct impact on the quality of the final product. The development of materials science has provided materials with higher strength, better plasticity, and better surface treatment performance for metal stamping. At the same time, surface treatment techniques for materials, such as galvanizing, chrome plating, spraying, etc., also play an important role in improving the corrosion resistance and decorative properties of stamped parts.
Environmentally friendly and sustainable development
The metal stamping industry is increasingly focusing on environmental protection and sustainable development while pursuing economic benefits. Adopting clean energy, reducing the use of harmful chemicals, improving material utilization, and recycling waste are all important ways to achieve green manufacturing.
epilogue
The metal stamping process has become an indispensable part of modern manufacturing due to its high precision, high efficiency, and high automation. With the continuous emergence of new materials and technologies, the metal stamping process will continue to develop towards greater precision, intelligence, and environmental friendliness, providing strong support for innovation and development in the manufacturing industry.