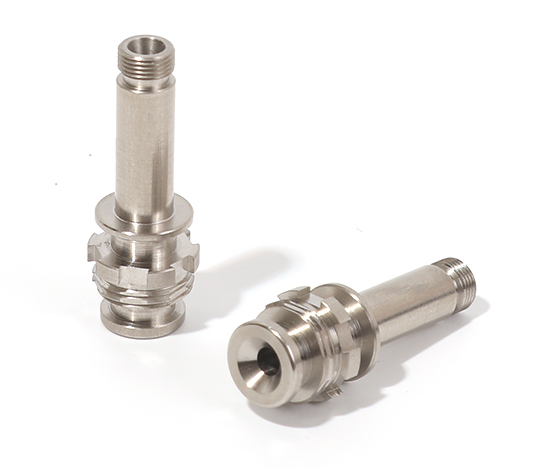
There are several major difficulties in CNC machining of medical parts and accessories
There are several major difficulties in CNC machining of medical parts and accessories:
1.Difficult to process titanium alloy materials
90% of implanted medical components are supported by Ti6AI-4V titanium alloy, which is the most commonly used material for medical implant devices due to its lightweight, high strength, and high biocompatibility.
Titanium alloy has the characteristic of work hardening; The machining process involves significant shear, resulting in thin chips and forming relatively small contact areas on the tool; In addition, the high cutting force during the machining process, combined with the frictional force during chip flow, will result in excessive local cutting heat of the tool. However, titanium alloy has poor thermal conductivity, which prevents cutting heat from being quickly dissipated.
2, Reliable and compact machine tool fixtures
Medical parts and accessories equipment need to be able to process small and complex parts made of difficult to machine materials with high precision requirements, such as substitute parts for processing bones and joints, which are quite complex; Due to the poor cutting performance of the processed material, the blank is usually a bar material - which means a large amount of metal needs to be removed.
Medical parts accessories have high requirements for workpiece materials, processing accuracy, and surface smoothness, which requires high reliability of the processing system; Therefore, extremely high requirements are put forward for machine tools, fixtures, cutting tools, CAM software, etc.
3,Stable and efficient cutting tools
3-1:The requirements for machine tools are relatively high; Advanced medical equipment processing equipment such as Swiss automatic lathes, multi spindle machine tools, and rotary workbenches are completely different from typical machining centers and lathes, as they are very small in size and compact in structure; In response to such requirements, the structure of the cutting tool also needs to have special design, requiring the size of the tool to be very small while ensuring the rigidity of the tool.
3-2:High requirements for processing efficiency; For medical devices, the most important thing is processing efficiency, that is, processing pace, which requires the ability to replace blades in the shortest possible time.
3-3:From the perspective of the workpiece itself, it has significant differences from other mechanical components; The medical devices implanted in the human body first require excellent smoothness, high precision, and no deviation. This requires the tool to meet high processing requirements from the design of the blade structure to the design of the blade coating.