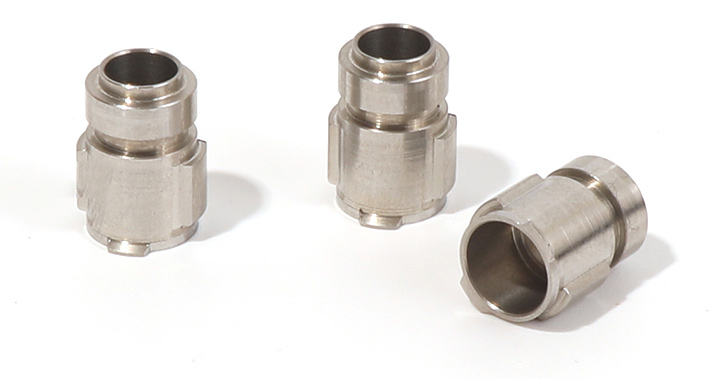
Automotive Parts Processing Technology
A car is composed of numerous components, each of which plays a different role and requires different processing techniques to be processed before it can be installed on the car for use. What are the processing techniques for automotive components?
1,Forging and processing of automotive parts
In the process of automobile manufacturing, forging is widely used as a processing method. The forging methods are divided into free forging and model forging. Free forging is a processing method in which a metal billet is placed on an anvil and subjected to impact or pressure to form a shape (commonly known as "forging"). The blanks of gears and shafts in automobiles are processed using free forging methods.
Model forging is a processing method in which a metal billet is placed in the mold cavity of a forging die and subjected to impact or pressure to form a shape. Model forging is somewhat like the process of pressing dough into the shape of a cookie inside a mold. Compared to free forging, forging produces workpieces with more complex shapes and more precise dimensions. Typical examples of forged parts for automobiles include engine connecting rods and crankshafts, steering knuckles, and automobile front axles.
2,Automotive parts casting and processing
Casting is a production method in which molten metal is poured into the cavity of a mold, cooled and solidified to obtain a product. In the process of automobile parts processing and manufacturing, there are many parts made of cast iron blanks, which account for about 10% of the total weight of the vehicle, such as cylinder block, transmission case, steering gear housing, rear axle housing, brake drum, various brackets, etc.
Sand molds are commonly used for manufacturing cast iron parts. The raw material for sand molds is mainly sand, mixed with binders, water, etc. Sand mold materials must have a certain adhesive strength in order to be molded into the desired shape and withstand the erosion of high-temperature molten iron without collapsing. In order to shape a cavity in the sand mold that matches the shape of the casting, a model must first be made of wood, called a wooden mold. After the hot molten iron cools, its volume will shrink. Therefore, the size of the wooden mold needs to be increased according to the shrinkage rate based on the original size of the casting, and the surface that needs to be cut and processed will be correspondingly thickened.
Heat treatment processes include annealing, normalizing, quenching, and tempering. Annealing is the process of heating and holding a steel component for a certain period of time, followed by slow cooling along with the furnace to obtain a finer and more uniform structure, reduce hardness, and facilitate cutting processing. Normalization is the process of heating and insulating steel components, removing them from the furnace, and then cooling them in air. It is suitable for refining low-carbon steel. Quenching is the process of heating and insulating steel components, followed by rapid cooling in water or oil to increase their hardness. Tempering is usually the subsequent process of quenching, in which the quenched steel is reheated, insulated, and cooled to stabilize the structure and eliminate brittleness. Many automotive parts require surface high-frequency quenching, carburizing, cyanide and other heat treatment processes to maintain the toughness of the core while changing the surface structure to improve hardness.