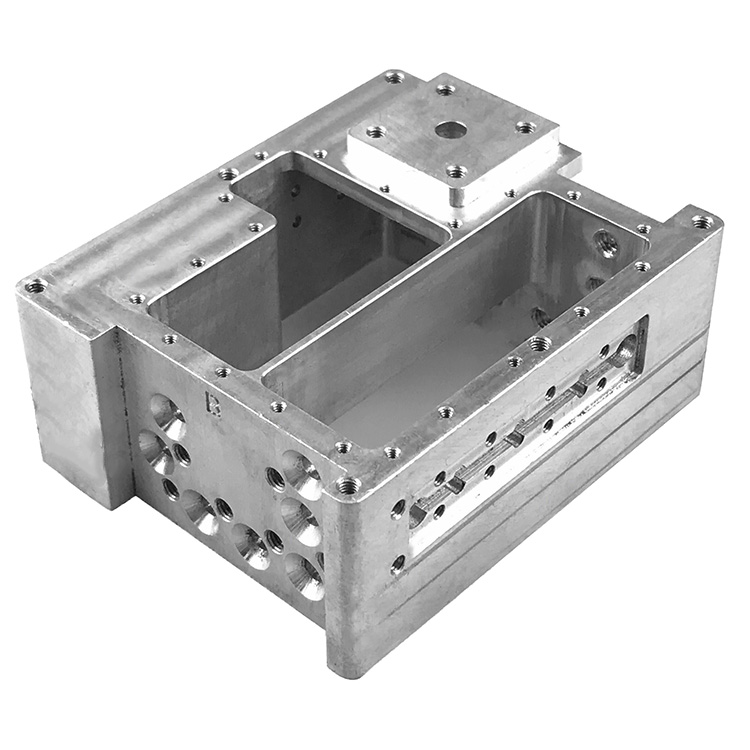
Aluminum Alloy CNC Machining Guide
1. Material selection:
1.1 Aluminum alloy selection:
Common aluminum alloys include 6061, 7075, etc. Choose the appropriate alloy based on the requirements of part strength, corrosion resistance, and machinability.
1.2 Material Status:
Considering the material state, T6 state can provide higher strength and hardness.
2. Parts that can be made:
2.1 Structural components:
Aircraft components, automotive body structures, etc.
2.2 Aviation parts:
Engine components, wing connectors, etc.
2.3 Electronic device casing:
High strength and lightweight shell components.
3. Applied process:
3.1 CNC milling:
Used for making parts with flat surfaces, grooves, and complex contours.
3.2 CNC Drilling:
Used for hole machining on aluminum alloys, such as hole rows and positioning holes.
3.3 CNC turning:
Produce cylindrical parts and rotationally symmetric parts.
4. Quality inspection requirements:
4.1 Dimensional measurement:
Use coordinate measuring machines and other equipment to accurately measure the dimensions of parts.
4.2 Surface quality inspection:
Visually inspect the surface to ensure there are no defects, scratches, or other imperfections.
4.3 Hardness testing:
Conduct hardness testing to ensure compliance with design requirements.
5. Transportation requirements:
5.1 Packaging:
Use shock-absorbing materials for packaging to ensure that the parts are not damaged during transportation.
5.2 Labels and Documents:
Attach clear labels and handling instructions on the packaging.
Provide detailed documents, including CAD files, manufacturing process instructions, and quality inspection reports.
Conclusion:
By following this aluminum alloy CNC machining guide, you will be able to efficiently produce aluminum alloy parts that meet high-quality standards, ensuring their reliability and accuracy during design, manufacturing, and transportation.