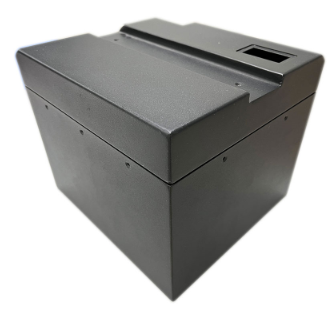
Metal Battery Shell For New Energy Vehicles
The electrification of automobiles continues to deepen, and the power battery industry is entering a new cycle of prosperity. Structural components, as the core safety components of power batteries, will experience rapid development. Hard shell structural components consist of a cover plate and a shell, which can be divided into cylindrical and square types according to packaging technology. They have functions such as energy transmission, fixed support, power-off and pressure relief.
In hard shell structural components, the cover plate has rich functions, and explosion-proof valves and flip plates are the main safety components with strict sensitivity requirements. The cover plate has functions such as current conduction, pressure relief, fuse protection, and reducing electrical corrosion. The material has changed from stainless steel to copper aluminum composite material. Among them, the explosion-proof valve design plays a major role in battery safety protection. When the internal pressure exceeds the opening pressure of the explosion-proof valve, the explosion-proof valve will rupture from the scratch and release pressure. The top cover of lithium iron phosphate batteries often adopts a single explosion-proof valve structure, and the opening pressure of the explosion-proof valve is 0.4~0.8MPa; The ternary system battery adopts a dual protection form of explosion-proof valve and SSD. The SSD flipping pressure is between 0.45~0.55MPa, which is lower than the opening pressure of the explosion-proof valve (0.75~1.05MPa). When the battery is abnormal, it will fuse before the explosion-proof plate for protection. Therefore, the stability of the opening pressure of explosion-proof valves and flip plates is a key technical indicator, and generally requires PPK ≥ 1.67.
The composite pole top cover structure improves space occupancy. The battery capacity and energy density are directly affected by the occupancy rate and weight of the top cover space. With the continuous improvement of processing technology, the composite pole top cover structure used in hard shell structural components reduces the height from the pole to the top cover plate to 3.3mm, which is 4.0mm lower than the injection molded top cover structure. The design space occupancy rate of the top cover continues to increase, and the height of the battery cell pole pieces increases accordingly, thereby improving the battery capacity and energy density.
The processing technology is constantly improving, and the manufacturing process of the cover plate is becoming more complex. The manufacturing of lithium battery structural components belongs to precision manufacturing, among which the production process of hard shell structural component cover plate is more complex than that of shell, including stamping, cleaning, welding, injection molding and other process steps. High performance cover plates require laser welding technology and friction welding technology support and corresponding processing equipment, so there are certain technical barriers in manufacturing.
We are a hardware stamping and processing enterprise serving the automotive, industrial, medical, new energy, photovoltaic and other industries. We specialize in hardware mold design, mold making, precision hardware stamping, battery cells, heat sinks, sheet metal processing, chassis and cabinets, CNC punch sampling, bending prototype and other one-stop services for hardware parts. With strong research and development capabilities, new products in new technologies, materials, and molding processes are constantly emerging and receiving widespread praise in the industry.