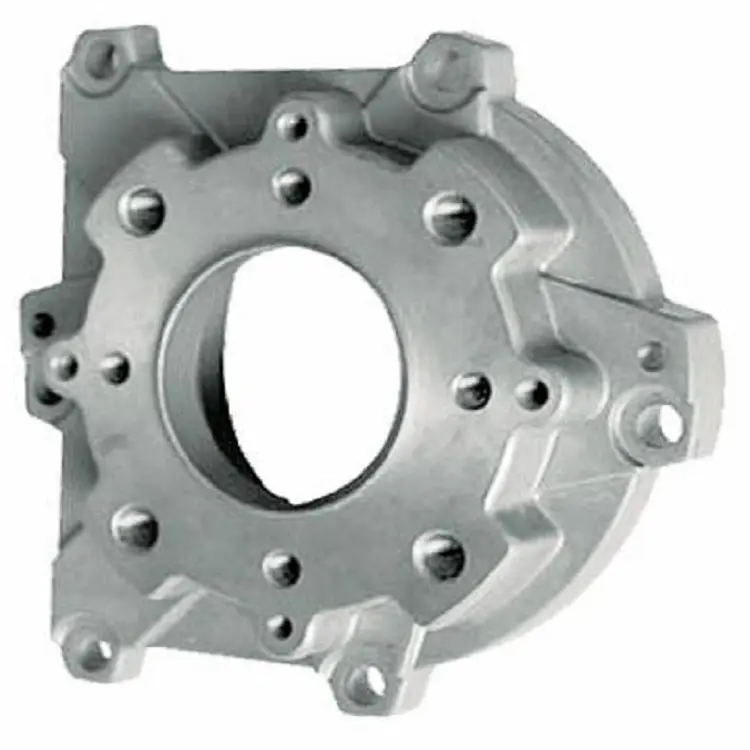
CNC Machining Stainless Steel Complex Parts
Stainless steel CNC machining complex parts should avoid those problems as much as possible
When machining complex parts with stainless steel CNC, special attention should be paid to the following issues, including chamfering, roughness, surface treatment, accuracy, and wall thickness:
1.Chamfering issue: Avoid uneven chamfering or situations where it does not meet design specifications. Ensure that the angle and size of the chamfer are consistent with the design requirements to improve safety and appearance.
2.Roughness control: Stainless steel is usually difficult to process and can easily produce high surface roughness. Use appropriate cutting speed, feed rate, and tools to reduce roughness, and consider surface treatment after machining to improve quality.
3.Surface treatment: Stainless steel typically requires additional surface treatments such as polishing, grinding, or sandblasting to improve appearance and enhance surface quality. Ensure that the surface treatment meets the design requirements.
4.Accuracy issue: Ensure that CNC programming and settings are very accurate to ensure that the size and shape of the parts meet the design specifications. Avoid error accumulation and dimensional instability.
5.Wall thickness control: Pay attention to the wall thickness of stainless steel parts to ensure consistency throughout the entire part to avoid material unevenness.
6.Hot deformation: Stainless steel is easily affected by heat during processing, which may lead to hot deformation. Control cutting parameters and cooling methods to reduce thermal effects.
7.Tool selection: Use high-quality tools suitable for stainless steel materials, and regularly inspect and replace the tools to ensure cutting effectiveness and tool life.
8.Vibration and resonance: Avoid vibration and resonance, which may cause uneven surfaces or dimensional deviations. Ensure the stability of the machine tool.
9.Debris control: Ensure effective debris control to prevent debris from entering the cutting area, affecting surface quality and tool life.
10.Quality inspection: Conduct strict quality inspections, including dimension measurement, roughness measurement, and surface treatment evaluation, to ensure that the parts meet the requirements.
By carefully paying attention to the above issues, it is possible to ensure high quality and precision in stainless steel CNC machining of complex parts, while improving production efficiency and product reliability.